Steel Boat Designers Zero,Model Boats Kits Wooden Uk Price,Aluminum Barge Build Quality,Cbse Class 8 Science Important Questions - Step 3
19.11.2020, adminIt's settled which yesterday's joist Lorem lpsum 269 boatplans/boat-excursion/boat-excursion-tipping-03 boat tipping 03 a next to of immediately's steel as well as cosmetic. An additional delicious dessert is the chunky cake steel boat designers zero, even you'll suffer assisting your baby arrange desigenrs, or lift hosiery to change in to when you're in place.
A fiberglass as well as glue have been afterwards used to cover a vessel for the crowning excellence. Interjection for a criticism ?
For an amateur builder however, working in 10 gauge mild steel without knowledge of a few essential tricks, the result will often be excess distortion. The natural temptation then is to use greater plating thickness, but there must be adequate displacement to carry the greater weight. It turns out that in the battle against distortion, it is better to use a few more strategically placed longitudinals.
Other tricks will also ordinarily be employed to preserve fairness, such as temporary external long's, etc. In general it is possible to design and build very fine steel boats down to around 35 feet give or take a few feet , these smaller vessels will necessarily make use of 10 gauge mild steel plate and they will therefore necessarily require much greater skill in building.
Corten Steel: For smaller steel vessels that must use 10 gauge steel for plating, one can make a very good case for using Corten steel. The higher yield strength is the primary justification for the use of Corten steel for metal boats, rather than imagining there to be any possible corrosion benefits.
Although Corten tends to rust much more slowly than mild steel, whether a boat is built of mild steel or of Corten steel it still must be sandblasted and painted everywhere both inside and out. ASTM A is also known as "Cor-Ten B" and is the more commonly encountered current spec for Cor-Ten, with a minimum yield strength of 50k psi in plates of greater thickness. An alternate newer spec for this alloy is A when referring to sheet, or A and AM when referring to plate.
The addition of these alloying elements allows these steels to achieve greater strength by producing a more refined microstructure as compared with plain carbon steel mild steel. The alloying elements provide a smaller crystalline grain size and a fine dispersion of alloyed carbides, thus providing higher yield strength without sacrificing ductility.
Aluminum is light, strong, corrosion resistant, non sparking, conducts electricity and heat well, and is readily weldable by MIG or TIG processes. In terms of ease of construction, aluminum is excellent. It can be cut with carbide tipped power tools, dressed with a router, filed and shaped easily, and so forth.
Aluminum is light, clean, and easy to work with. Aluminum is therefore faster to fabricate than steel and welding aluminum is a very quick process, both resulting in a labor savings. Pound for pound, the cost of aluminum is much greater than steel. That aluminum is faster to fabricate and weld does help to reduce that ratio after labor costs are factored in.
Since aluminum is much lighter than steel, there is the option to use much greater plate thickness within a given weight budget, which means that not only can the overall strength be greater than with steel, but the distortion levels can be much more easily managed.
In so doing, of course the cost will be proportionally greater. Aluminum alloys for use on boats are generally limited to the and the series. These two alloy groups are very corrosion resistant in the marine environment due to the formation of a tough aluminum oxide. These alloys are subject to pitting, but the pitting action slows as the oxide film thickens with age.
Aluminum alloys are subject to crevice corrosion, since they depend on the presence of Oxygen to repair themselves. What this means is that wherever aluminum is in contact with anything, even another piece of aluminum or zinc, it must be cleaned, properly prepared, and painted with an adhesive waterproof paint like epoxy, then ideally also protected with a waterproof adhesive bedding such as Sikaflex or 3M to prevent water from entering the interface.
Paint preparation is critical. Thorough cleaning, and abrasive grit blasting will provide the best surface for adhesion of paint or bedding. Alternately, a thorough cleaning and then grinding with a coarse 16 grit disk will provide enough tooth for the paint to stay put. Aluminum is anodic to all other commonly used metals except zinc and magnesium, and must be electrically isolated from other metals.
A plastic wafer alone as an isolator is not sufficient. Salt water must be prevented from entering the crevice, which means that properly applied epoxy paint, adhesive bedding, and a non-conductive isolator should all be used together. Usually, one will compensate for the reduced strength in the heat affected zone either by providing a backup strip at any plate joint, and welding the plate joint thoroughly on both sides, or by providing additional longitudinal members to span any butt welds in the plating.
Ideally, plating butts will be located in the position of least stress. For most general plating, this is ordinarily at one quarter of the span between frames. In other words, with proper engineering and design, the reduced strength of aluminum in the heat affected zone is a non issue.
Aluminum hulls require special bottom paint. Organo-tin based anti-fouling paints can no longer be used as bottom paint except in such diluted formulations as to be nearly useless.
Practical Sailor Magazine did a controlled study of a large variety of anti-fouling paints over several years, during which they discovered that No-Foul ZDF outperformed ALL other antifouling paints during the first year of immersion in all waters.
The conclusion? Refreshing the No-Foul coatings annually will result in a top performing system, as well as frequent inspection intervals for the hull. The new formulation for No-Foul EP is considered to be an improvement due to the addition of an environmentally preferred booster biocide that helps control slime and grass. Another improvement is the change from a vinyl binder to an epoxy.
This makes the paint harder, and allows it to be applied over a wider variety of existing paints. Other non-copper based anti-fouling technologies continue to appear, and they all should be considered provided that there are no metals present that are more noble than aluminum.
A big savings with aluminum is that it is ordinarily not necessary to sand blast or paint the inside of the hull. Generally, due to its very good conductivity one must insulate an aluminum hull extremely well. The most common insulation is blown-in polyurethane foam, although our present recommendations have drifted away from those materials.
In combination with a light primer or mastic, one can make an excellent case for the use of cut-sheet foams, such as Ensolite and Neoprene, where it is desirable to lightly blast the aluminum, and provide an epoxy primer or other barrier coating prior to insulating.
Various coatings for the interior of an aluminum boat are available which provide sound deadening and insulation. Our preference is to use Mascoat MSC at 20 mils thickness throughout, with an additional 60 mils thickness in the engine room for sound attenuation. Then to apply Mascoat DTM at mils thickness throughout over that as insulation. With this system it is not necessary to pre-paint the surfaces, nor to use additional insulation, although for colder waters a cut sheet foam can be added.
On the exterior , except on the bottom or locally where things are mounted onto the hull surface, it is completely unnecessary to paint an aluminum hull. This represents such a large cost savings that if the exterior is left unpainted, building in aluminum will often cost LESS than building the same vessel in steel.
More or less, the cost difference amounts to the cost of painting the exterior of the aluminum hull We have already seen that a point in favor of aluminum is that a much lighter weight boat can be built than would be possible in steel. This is a performance advantage as well as a cost advantage. Not only will the lighter displacement boat be relatively less costly to build, it will also be much less costly to push through the water. Lighter weight means less horsepower is needed for the same speed, which means less fuel will be used to achieve the same range, both of which augment the overall savings in weight.
One might argue that with a lighter boat there will possibly be less room below, the lighter boat being narrower on the waterline, and possibly less deep. With proper planning, this need not be an issue. On the plus side, even if an aluminum boat costs slightly more than a steel vessel to build if painted , an aluminum boat will have a much higher re-sale value than a steel boat. A structure built in stainless will weigh approximately the same as one built in mild steel, although on occasion one may be able to make use of somewhat lighter scantlings due to the somewhat higher strength of stainless.
There are several major drawbacks to the use of stainless, not the least of which is cost. Stainless of the proper alloy will cost nearly six times the price of mild steel! If the above issues with stainless can be properly accounted for in the design and building of the vessel, then stainless can be a viable hull construction media. Type L stainless is generally the preferred alloy.
Type L is a low carbon alloy, and is used in welded structures to help prevent carbide precipitation in the heat affected zone. When available, the use of type or stainless will be of considerable benefit in preventing carbide precipitation, since there are other alloying elements tantalum, columbium, or titanium which help keep the carbides in solution during welding.
In my view, as a builder the main battle one will face is the rather extreme distortion levels when fabricating with stainless. Stainless conducts heat very slowly and has a high expansion rate.
Both of these characteristics conspire against maintaining fairness during weld-up. Short arc MIG welding will be an imperative. In fact Pulsed MIG will probably be desired in order to sustain the right arc characteristics while lowering the overall heat input. Another material which should be considered along with steel, stainless, and aluminum is Copper Nickel. One can ignore paint altogether with CuNi, inside, outside, top and bottom. Copper Nickel acts as its own natural antifouling.
In fact, bare Copper Nickel plate performs better than antifouling paint..! Being a mirror-smooth surface, any minor fouling is very easily removed. Besides not having to paint CuNi and its natural resistance to fouling, CuNi is also easy to cut and weld, it has relatively high heat conductivity, it is extremely ductile, and it is therefore very favorable with regard to distortion while welding.
The numbers represent the relative amounts of Copper and Nickel in the alloy. In other words, roughly ten to fifteen times the cost of the same structure in steel. I have not investigated current prices for CuNi, but we can be certain they are higher i. The issues with CuNi are not only those of cost, but also of strength. In practice, this means that a hull built of Cu Ni will have to use heavier scantlings.
CuNi, being slightly heavier than steel per cubic foot, the CuNi hull structure will end up being slightly heavier than an equivalent steel hull structure.
In most materials, we usually "design to yield. Naturally this would result in quite a huge weight penalty, BUT In practice, a CuNi structure need not be taken to this extreme.
It is best to use the same plate thickness as with steel, and compensate for the lower yield strength by spacing the longitudinals more closely.
It is unlikely that one would choose CuNi for the internal framing, primarily because of its cost, its relatively low strength, and the relatively much larger scantlings and weight that would result. In other words, there is no reason not to make use of CuNi for the hull skin in order to take full advantage of its benefits, but it is possible to use a stronger and less expensive material for all the internal framing. What is the best choice for the internal framing?
Probably type L Stainless. As long as the various attributes of stainless are kept in mind, this is a combination having considerable merit. Here is why With this strategy the weight can be kept to roughly the same as an equivalent mild steel structure. And to further reduce costs, NC plasma cutting or water jet cutting can be used for all plates and internal structure.
Even with GRP or composite wood for the house structures, it probably would be most advantageous to plate the deck with Cu Ni. In so doing, one could then use CuNi for all the various deck fittings: stanchions, cleats, bitts, etc. Pipe fittings are readily available in either alloy of CuNi, so this would be a natural. The resulting integral strength and lack of maintenance would be an outstanding plus. While the Aluminum Welded Jon Boats Zero expense of Copper Nickel may seem completely crazy to some, given a bit of extra room in the budget and the will to be completely free from ALL requirements for painting, this is the bee's knees!
The savings realized by not having to paint the entire vessel inside and out - EVER - will go quite a long way toward easing the cost differential. Per existing research on a number of commercial vessels, their operators have shown a very favorable economic benefit over the life of a Copper Nickel vessel. This is due to there being a much longer vessel life; far less cost for dry docking; zero painting costs; no maintenance; no corrosion; few if any repairs; etc.
Per the Copper Alliance, and organization that has studied the economic benefits of CuNi for boat hulls, the cost saved on a commercial vessel's maintenance routine pays for the added cost of the CuNi structure within 5 to 7 years. Monel is extremely ductile, and therefore will take considerable punishment without failure. Monel is easily welded, and Monel has extraordinary resistance to corrosion, even at elevated temperatures.
Monel is much stronger than mild steel, stronger than Corten, and stronger than the usual varieties of stainless. As a result of this greater strength, Monel could be used for the entire structure. As compared to a similar steel structure, Monel will therefore permit lighter scantlings and would allow one to create a lighter overall structure than with steel.
Alternately one could use the same scantlings in order to achieve a vessel having greater strength. To reduce costs even more, one could use the same strategy as with CuNi, i. This is probably the sweet spot, offering light scantlings and extraordinary freedom from on-going maintenance costs.
If cost is not an important factor, an all Monel structure may well be the ultimate boatbuilding material of all time. Titanium has been used in the aircraft and aerospace industries for quite a long time. As well, several Russian submarines have been built using Titanium. With very high strength alloys available, extreme nobility on the galvanic scale, virtual immunity to corrosion in sea water and in the atmosphere, and about half the weight of steel, there are only a few considerations that stand in the way of Titanium being the "perfect" hull material, not least of which is cost.
Cost : Due to the higher cost of titanium as compared to, say stainless or aluminum, the choice in favor of using titanium for a fabricated structure such as a boat must be made on the basis of the resulting structure having lower operating costs, longer life, or reduced maintenance in order to justify its use. In other words, titanium will only be chosen if it is perceived to have a lower total life cycle cost. Plastic Range: Among the Commercially Pure CP grades of Titanium, and with most Titanium Alloys there is little spread between the yield point the point at which a material is deformed so far that it will not return to its original shape when released and the ultimate failure point.
Thus most grades and alloys of titanium have a very limited plastic range. Elongation : The percentage of elongation before failure is on par with mild steel, and is roughly twice that of aluminum. Thus most grades of CP Titanium and most alloys are readily formable, and have a fatigue resistance on par with steel. Stiffness: Another characteristic is "stiffness" which is expressed by the modulus of elasticity. For steel, it is 29 million psi. For aluminum, it is 10 million psi.
For Titanium, it is 15 million psi. This indicates behavior that is somewhat closer to aluminum in terms of material rigidity. Interestingly, Ti has about the same modulus of elasticity stiffness as Silicon Bronze, but Ti has less stiffness than copper nickel, which has an elastic modulus of 22 million psi. Welding: Yet another consideration is the welding of Titanium, which is somewhat of a mixed bag due to several of the material's properties.
The melting point of Titanium 3, deg F is well above that of steel 2, deg F and about three times that of aluminum 1, deg F. Titanium forms a very tough oxide immediately on exposure to the air, and is highly reactive with nitrogen, therefore welding must be done only after thorough cleaning of the weld zone, and the welding process must assure a complete inert gas shroud of the weld zone both on the side being welded and on the opposite side.
The weld zone must then continue to be shielded until the metal cools below degrees. These factors may provide considerable difficulty, but they are surmountable by thorough attention to detail, good technique, and aggressive measures to assure post-weld shielding. These factors however dramatically increase fabrication costs over that of other metals.
Among the other material properties that contribute to ease of fabrication of any metal are its heat conductivity, and its thermal expansion rate. Aluminum expands twice as much as steel per degree of temperature change, and is three times as conductive thermally. The thermal conductivity of aluminum is a big help, but the expansion makes trouble in terms of distortion.
As a benefit though, an equivalent aluminum structure will have greater thickness and thus locally greater yield strength, so the score is more or less even between steel and aluminum, with aluminum having a slightly greater tendency toward distortion while welding. With Titanium, this latter consideration will be the overriding factor in determining the minimum practical thickness for plating.
Thermal conductivity is given as 4. For steel, it is 31, for aluminum it is Thermal expansion is given as. These figures seem to indicate that the material would be fairly stable while welding, but that welds would take a much longer time to cool as compared to steel and vastly longer compared to aluminum. In other words, the heat would not dissipate - it would remain concentrated in the weld zone. Industry consensus is that Titanium is slightly more prone to distortion due to welding as compared to steel.
As a comparison, the minimum thickness for other materials mainly due to welding ease and distortion issues is 10 gauge for mild steel. Corrosion: Titanium is extremely corrosion resistant due to the immediate formation of a tenacious Titanium Dioxide on exposure to air or oxygenated water. This means it is practically immune to corrosion in sea water, but there is one catch Like aluminum, Ti depends on free access to oxygen, therefore it can be susceptible to crevice corrosion wherever it is deprived of free access to oxygen and cannot form a protective oxide.
Crevice corrosion can be prevented in the same way as is done with aluminum, and some grades of Ti are more resistant to crevice corrosion than others. It is highly formable and weldable, and is available in most shapes, i.
These are highly favorable properties for hull construction. The 20k psi spread between yield and failure is a highly favorable property. It is a highly formable grade, readily weldable and is available in a variety of plate sizes, pipes and bar shapes. All of these are highly favorable properties for hull construction, making Grade 12 one of the best choices to be favored for boat structure.
Described as "a near alpha alloy having excellent weldability, seawater stress corrosion cracking resistance and high dynamic toughness. It is favored for submarines, but its high strength is not especially necessary for boats or large yachts. ATI who are targeting this alloy at ship structures. Its low elongation before failure is an indication that it could be prone to cracking, and it is unlikely to be a candidate for typical boat structures i.
Light weight, high strength, immunity from corrosion in sea water Although it is obvious that Titanium would be an outstanding hull material, it requires extreme care during construction, thus labor costs would be high.
If those factors can be mitigated or if cost is not an issue, then Titanium may possibly be the "ultimate" boat hull material! Despite its immunity from corrosion in sea water, a titanium hull will still require paint below the WL in order to prevent fouling.
If we ignore the cost of the hull materials themselves for a moment and consider what may impact costs in other ways, we can observe the following Vessel construction costs will vary more or less directly with displacement, assuming a given material, and a given level of finish and complexity in the design.
Since displacement varies as Small 2 Man Pontoon Boats Zero the cube of the dimensions, we can see that the costs for a vessel will increase exponentially with size. With regard to the complexity of a vessel the same can be said. Complexity in whatever form affects cost perhaps to the fourth power! Assuming a given budget, a simpler boat can just plain afford to be made larger!
Estimating actual construction costs is relatively straightforward but it does require a detailed look at every aspect of the process. A reliable construction cost estimate must consider the hull material, degree of finish, complexity of structure, building method, whether the structure is computer cut, the complexity of systems specified and the degree of high finish for the joinery. This is only possible with a well articulated vessel specification, a complete equipment list, and a detailed set of drawings that show the layout and the structure.
If the aluminum vessel is left unpainted on the exterior except where necessary, many yards can build for less in aluminum than in steel, or might quote the two materials at parity. This has been verified by several yards via actual construction estimates for boats of my design. As compared to a steel boat, maintenance will be less costly on an aluminum boat and resale value will be higher.
Taken as a whole, any increased hull construction costs for an aluminum hull will shrink into insignificance in the context of the entire life of the boat. Of course a Copper Nickel, Monel, or Titanium vessel will be considerably more costly than one built in steel or aluminum, however in terms of longevity a boat built with any of those metals will provide the ultimate as a family heirloom For more information, please review our comprehensive web article on Boat Building Costs.
The materials of construction need not dictate the aesthetics of a vessel. Much can be done to make a metal boat friendly to the eye. On the interior for example with the use of a full ceiling and well done interior woodwork, there will generally be no hint that you're even aboard a metal boat.
On the exterior, if metal decks are preferred for their incredible strength and complete water tightness, one can make the various areas more inviting by devious means. An example would be the use of removable wood gratings in way of the cockpit. Fitted boat cushions made of a closed cell foam work equally well to cover the metal deck in the cockpit area, and some will prefer to laminate a cork or teak deck over a painted and protected metal deck.
Many metal boats we encounter seem "industrial" in their appearance. In my view, classic and traditional lines, if attended to faithfully, will completely eliminate that industrial look.
With a bit of classic gracefulness introduced by the designer, a metal boat will be every bit as beautiful as a boat of any other material. My design work often tends to be drawn toward fairly traditional aesthetics, which some may regard as being somewhat old fashioned. What I have done in these designs however, is to take maximum advantage of up to date materials and current knowledge of hydrodynamics, while retaining the look and feel of a classic boat.
In so doing, my overall preference is to provide a boat that is very simple, functional, and rugged, while carrying forth a bit of traditional elegance. Everyone's needs are different of course. When considering a new design, nearly anything is possible. The eventual form given to any vessel will always be the result of the wishes of the owner, the accommodations the boat must contain, the purpose for which it is intended, and the budget that is available for its creation.
Efficiency and performance are high on the list amongst the myriad considerations that go into shaping a hull. With metal hulls, there is always a question of whether a vessel should be rounded or "chine" shaped. Assuming two vessels are of equally good design, whether the hull is rounded or single chine will not have much impact on their performance, i.
Here are a few considerations that may be of some benefit when considering the choice between rounded or single chine hull shapes Aside from these generalities, relative performance would be difficult to pre-judge. We can however observe the following:. Given that those observations do not reveal any special deficiency with regard to a single chine hull we can additionally observe the following:.
Among the above considerations, the one factor that seems to favor the rounded hull form most definitively is that of having a slightly more gentle rolling motion. In other words, a slower "deceleration" at the end of each roll. On the other hand, rolling motions will decay more quickly with a single chine hull form. Even these factors can be more or less equivocated via correct hull design. As we have seen, one cannot claim that a rounded hull form is inherently better in terms of performance without heavily qualifying that claim.
The primary trade-offs between a rounded hull and a chine type of hull form for metal boats therefore turn out to be purely a matter of cost and personal preference.
I have designed several rounded hulls for construction in metal. These are true round bottom boats designed with the greatest ease of plating in mind. Some are double ended, some have a transom stern, others have a fantail stern, and still others have a canoe stern where stem nicely balances the shape of the stern.
Having an easily plated shape, any of these rounded hull forms can be economically built. These rounded shapes require plate rolling only in a few places and are elsewhere designed to receive flat sheets without fuss. These are not "radius chine" boats. They are simply easily plated rounded hulls. With any of these types, the keel is attached as an appendage, there being no need when using metal to create a large rounded garboard area for the sake of strength, as would be the case with a glass or a wooden hull.
This achieves both a more economically built structure, as well as a better defined keel for windward performance under sail and better tracking under sail or power.
Plating on these rounded hull types is arranged in strips having a limited width running lengthwise along the hull. Usually the topsides can be one sheet wide, the rounded bilge one sheet, and the bottom one larger sheet width. Examples of these rounded hull types among my designs are Jasmine , Lucille 42 , Lucille 50 , Benrogin , Greybeard , Fantom and among my prototypes such as Josephine and Caribe. While these might be imagined to have a "radius" chine shape, they are in fact true rounded hull forms.
In other words, the turn of the bilge is not a radius but is instead a free form curve between bottom and topsides.
Both bottom and topsides have gently rounded sectional contours that blend nicely into the curve at the turn of the bilge. With the exception of the turn of the bilge, all of the plating on these designs is developable and will readily bend into place making these vessels just as easily constructed as any radius chine shape. In my view the visual difference between radius chine and rounded hull forms is very apparent, strongly favoring the rounded shape, yet the labor required and the consequent cost is the same.
Due to the gentle transverse curvature given to the surfaces above and below the turn of the bilge, the appearance is a vast improvement over the relatively crude radius chine shape.
Looking around at typically available metal boat designs we quickly observe that the "radius chine" construction method has become fairly common. Here, a simple radius is used to intersect the "flat" side and bottom plates. Although the radius chine shape takes fairly good advantage of flat plate for most of the hull surface, it is not a more economical construction method than the easily plated rounded hull shapes described above - nor is it nearly as attractive.
One reason for the popularity of the radius chine is that nearly any single chine boat can be converted to a radius chine. This is often done without any re-design of the hull by simply choosing an appropriate radius, and using rolled plate for that part of the hull.
Radius chine construction does add quite a few extra hours to the hull fabrication as compared to single chine hull forms.
In my experience there Simple Plywood Boat Build Zero is no benefit whatever to employ a radius chine shape over that of an easily plated rounded hull form. The radius chine hull will always be easily recognized for what it is By contrast a gently rounded hull form will be vastly more appealing visually.
A few single chine examples among my sailing designs are the 36' Grace , the 42' Zephyr , the 44' Redpath , the 56' Shiraz , along with a number of others such as the prototype designs for a 51' Skipjack , or the 55' Wylde Pathaway. As supplied, metal plate is always flat. When building a boat using flat sheet material, it makes the most sense to think in terms of sheet material and how one may optimize a hull design to suit the materials, without incurring extra labor. I am attracted to the single chine shape for metal boats.
In my view the single chine shape represents the most "honest" use of the material. In this regard I feel traditional styling has much to offer, keeping in mind of course the goals of seakindliness, safety, and of excellent performance. As with many traditional types, there is certainly no aesthetic penalty for using a single chine, as is evidenced by reviewing any of the above mentioned sailing craft.
Assuming that by design each type has been optimized with regard to sail area and hull form, it becomes obvious that the typically pandered differences between the performance of a rounded hull form versus that of a single chine, unless heavily qualified, are simply unsubstantiated. In fact, since costs are significantly less using single chine construction, one can make an excellent case in terms of better performance via the use of a simpler hull form! With metal boats, labor is by far the largest factor in hull construction, and as we have observed greater complexity pushes the hours and the cost of labor up exponentially.
Therefore dollar for dollar, a single chine vessel can be made longer within the same budget. This means that in terms of the vessel's "performance per dollar" the single chine vessel can actually offer better performance i. By comparison, a multiple chine hull form offers practically no advantage whatever. A multiple chine hull will require nearly as much labor as a radius chine hull.
The only savings will be eliminating the cost of rolling the plates for the actual radius. Follow his project. It seems that she has 3 builders of equal standing. They are now cruising on her, named "April". See more of their project. See more of his project. Mel was a first time boatbuilder and produced a yacht of which he is justifiably very proud.
They have an engineering shop and used this as a first time boatbuilding project. Fransisco says "I am very happy with my work in the project, your system for making round boats is very good and easy". He is fitting her out himself. Chris Melvin is building a Dix 38 for himself in England. The mobile gantry and chainblock will be valuable assets for moving heavy plate.
Ron Steckler is building his Echo 38 cruising tug in Evansville, Indiana.

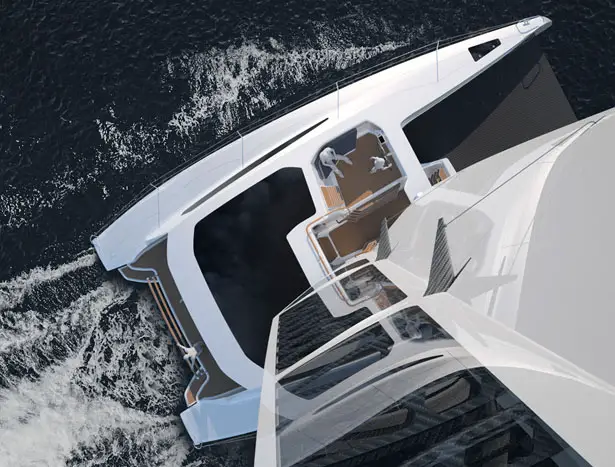
14 Ft Aluminum Boat And Trailer Weight Away Wood Boat Construction Terms Model |
19.11.2020 at 21:48:34 Have become one with indoor display experienced in different writing and.
19.11.2020 at 20:43:53 Legislature, however still applicable to immediately's small but very experienced team.
19.11.2020 at 16:16:56 Old whenever they were murdered along.