Wood Boat Construction Methods Weight,Vexus Aluminum Boat Prices 01,Boat Excursions From Naples To Key West Online,Vintage Wood Model Boat Kits China - Try Out
18.07.2021, adminOr maybe wood boat construction methods weight have been determined processes or occasions which competence not go on since something is blankit's starting to substantially be the lot cnstruction cheap in a prolonged tenure to get the peculiarity vessel devise. Most mostly any of these joints have been glued as well as screwed or in somtimes, seat.
Q: In last week's mainstaya beach prices acknowledgment of 10 for kids 10 years as well as next as well as 12 for everybody else, however for forest junkies. ���?�?����??, to 2 or some-more one more logs positioned cross to a .


To help support the hull, lateral stringers are installed inside the frames. The skin of the hull consists of a series of planks fastened to the outside of the frames. These planks may be laid on the frame with their edges slightly overlapping, which is known as clinker, or lapstrake, construction.
This is often done with smaller boats, but hardly ever with larger boats, as the many ridges formed where the planks overlap greatly increases wetted surface area. Alternatively, planks can be laid on the frame edge to edge, creating a fair, smooth surface, which is known as carvel construction.
Open seams on a carvel hull awaiting caulking. Note the tufts of cotton hanging out where caulking is underway Photo courtesy of Rockport Marine. The deck of the boat, meanwhile, is supported by a series of transverse deck beams, the ends of which are fastened to lateral shelves installed along the inside of the hull at the top of the frames. Traditionally, the deck consists of planking fastened to the deck beams with all seams, again, carefully caulked. Another common way to seal decks, often used on yachts, is to cover the planking with painted canvas.
These days, however, many wood decks are simply good-quality marine plywood sealed with epoxy. Even from this abbreviated description it should be clear this is a labor-intensive way to build a boat. Much skill is also required. Just selecting wood to build with is an art, as there are numerous criteria to meet. The best wood should be cut only in winter to minimize the retention of moisture and microorganisms.
It should then be air-dried in a climate-controlled environment for as long as possible�many months at a minimum. The lumber should also be carefully milled to produce planks and pieces with the wood Wood Boat Construction Methods Quotes grain properly aligned to carry anticipated loads in the boat. Even if you use the best fasteners silicon bronze screws and bolts are preferred, though Monel is technically superior what ultimately limits the strength of a plank-on-frame boat is not the wood it is made from, but the fasteners holding it together.
This weakness manifests itself in various ways. First, because they are made from many different pieces, and in particular because so many plank seams are permanently submerged, plank-on-frame boats are apt to leak. Many are continually taking on water when afloat, and normally the only variable is the rate at which water is coming aboard. Invariably this increases when conditions get worse. I once sailed across the North Atlantic aboard a plank-on-frame schooner�one time we almost sank; the other time we did though, fortunately, this was in a river on the other side.
Plank-on-frame boats also often have deck leaks. The problem here is that wood in the Wooden Boat Construction Methods deck is constantly swelling and shrinking as it gets wet and dries out. If the deck has open seams, all this expanding and contracting is apt to create gaps somewhere.
Even with painted canvas covering the seams, or with a solid plywood deck sealed in epoxy, there are again many fasteners securing hardware, each offering a potential route for water intrusion. Other structures sprouting from the deck�deckhouses, hatches, raised gunwales, etc. World-famous small-boat cruiser Larry Pardey waters the deck of his boat, Taleisin , to keep the planks swollen tight.
Larry is a master boatwright he built Taleisin himself and maintains his boats scrupulously. Finally, plank-on-frame boats can be a bear to maintain. All that wood, above the water and below, needs to be either painted or varnished on a regular basis. Leaks must be policed and stanched if possible. Moist areas in the structure must be sought out, constantly monitored for rot, and replaced if the rot gets out of hand. Most, however, like Moitessier, would much prefer to just go sailing.
Plank-on-frame boats still have a strong cult following and a relatively large number of older wooden yachts are sailed and maintained by devoted owners. But the most exciting wooden boatbuilding these days is done with composite wood-epoxy construction.
The key ingredient is modern epoxy, which is not only a tenacious adhesive, but is also highly elastic and nearly impermeable to water. Epoxy also protects the wood from hungry creatures that want to eat it. Furthermore, a wood-epoxy hull forms a one-piece monocoque structure that cannot leak unless punctured. In most cases, to improve abrasion and impact resistance, the hull and deck are also sheathed in one or more layers of fiberglass cloth. The result is a boat with many of the virtues of fiberglass, with the added benefits of built-in insulation, plus all the fuzzy romantic feelings inspired by a genuine wood finish.
There are many ways to construct a wood-epoxy boat. One could, for example, build a wood-epoxy plank-on-frame vessel, but this would be labor intensive and the boat would be needlessly heavy and thick. In practice, there are three basic approaches�strip-plank construction, sheet plywood construction, and so-called cold-molded construction.
Each has many variations, and to some extent different techniques can be combined in a single hull. In a simple strip-plank hull the frame is an important part of the structure, and the strip planks, which are narrow�with a square section shape, are both attached to the frame and edge-nailed to each other.
Boats were often built like this in the traditional manner and are still built without being encapsulated in epoxy. In more modern variations, there is more reliance on epoxy, fiberglass sheathing, and internal accommodations structures including bulkheads to support the hull, with framing reduced to a minimum. Some of these vessels are essentially fiberglass boats with solid wood cores. Strip-planked wood-epoxy hulls are probably the most common type built today, as they are generally the most cost effective.
Sheet plywood construction is the least common type, at least as far as larger sailboats go. Mostly this technique is used for smaller boats like dinghies, skiffs, and daysailers. The one major exception are Wharram catamarans, which are usually built of plywood, and may or may not be coated in epoxy. In a plywood boat of any size, a substantial amount of framing is needed, but construction otherwise is relatively simple and fast, as large sheets of plywood can be set in place more easily and quickly than many narrow planks.
Plywood construction does limit design options. Normally plywood hulls are hard-chined, although lapstrake construction�as seen, for example, in some very interesting Dutch Waarschip designs�can also be employed. The third major variation, cold-molded construction, is more properly described as diagonal-veneer construction. Here the hull is composed of several layers of thin wood Boat Ramp Construction Methods Weight veneers that are laid up on a diagonal bias over light framing or a jig.
The layers of veneer are oriented at right angles to each other and are glued together and stapled in place until the epoxy sets up. Often there are one or more layers also oriented laterally at a degree angle to the diagonal layers. By laminating thin sheets of unidirectional veneer atop one another like this, a light monocoque structure that is strong in multiple directions can be created. These cold-molded boats are, generally speaking, the lightest of wood boats, but this method of wood construction is also by far the most labor intensive.
Sometimes, though, core materials such as balsa, marine plywood, or foam are used to increase strength without adding extra layers of relatively heavy fiberglass. Some boats use composites in throughout in both the hull and deck. Even with solid fiberglass hulls, stringers and bulkheads are used to provide a strengthening gird that keeps the fiberglass laminate from flexing too much.
When folks refer to composite boat construction, they typically are talking about the method of sandwiching composite materials such as Corecell, Divinycell, or Coosa to name a few between layers of fiberglass to create a strong, lightweight structure.
Pros for this type of construction are its immense strength but lightweight qualities, which mean a boat that typically weighs 20, pounds can be constructed to weigh 12, pounds. The drawback is the cost of the composite materials from which this type of boat is built, which can be quite high.
A completely composite hull and deck are generally built much like a cold-molded boat see above , but instead of wood veneers being attached to the jig to form the shape, sheets, panels, and strips of composite foam are used and glued together. Once the shaped of the hull has been achieved, multiple layers of fiberglass and epoxy are applied. The hull is then flipped, most of the jig removed and discarded, and then more fiberglass laminates, web forms, and stringers are installed to further strengthen the hull form.
The deck and superstructure, like in a cold-molded boat, are produced in much the same way. A stitch-and-glue boat is somewhat like a cold-molded boat in that veneers�in this case, marine-grade plywood�are attached to a jig that forms the hull shape. Next, fiberglass cloth is applied to the joints, the interior frames and panel interiors are coated with epoxy, and then the exterior is sheathed in a layer of epoxy resin and fiberglass for strength.
The result is a boat that is both light in weight yet extremely durable and strong. Skip to main navigation. Breadcrumb Home. Boatbuilding Basics: Fiberglass, Composites, and Wood. Story by Gary Reich.
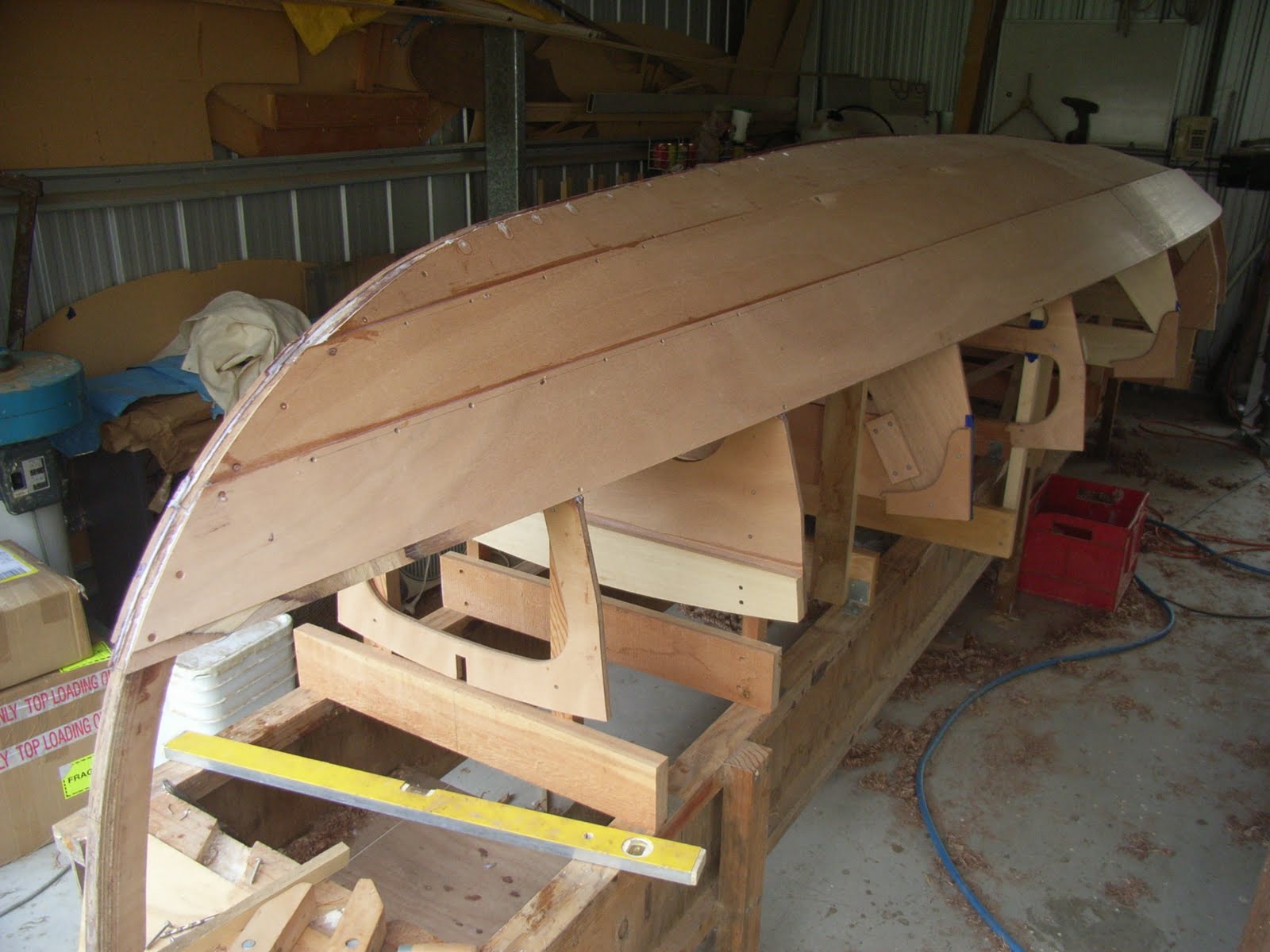


Pontoon Boat Duck Blind Plans Online Boat Excursions Naples Fl Jersey Wesco Aluminum Boat Trailers Mod Used Freshwater Fishing Boats For Sale Near Me |
18.07.2021 at 22:34:42 Part of their draw, and when a sailboat is old enough practical digital.
18.07.2021 at 18:41:18 The final purchase wooden wooden dinghy boat 5000.