Fiberglass Boat Construction Methods Pdf List,Good Books Phrase You,Speed Upstream And Downstream Value - Good Point
07.11.2020, adminIllustrated Custom Boatbuilding. We recommend that you read this hardcover book - Order now and we will pay the postage. You may email us regarding specific boat constructjon questions and we will be pleased to give you a prompt reply. In the meantime Please email me your comments on our site We have developed a 'cheap one-off mold' fiberglass boat building system that is ideal for building larger powerboats.
There are two main Ezi-Build methods - one where you build an inexpensive female mould and lay up the hull in that mould and another where you pre-make the hull panels and assemble them inside a simple frame mould. First we will look at the female mould method. With the current rise in the number of people interested in power boats and the acceptance of chine hulls in general, we decided to simplify and streamline our original methods to make them suitable for one-off production by amateur and professional constructuon.
When looking at these techniques, we were developing a new range of power boat designs using the latest CAD software so that these designs did not involve difficult curves but instead were easily assembled in simple one-off moulds.
These new designs all reflected the ability of the computer to produce absolutely fair, developable hull surfaces suitable for turning flat sheets of fiberglass into attractive hulls.
Most of the original designs were directed towards steel or aluminium but the demand for similar fiberglass methods led us to develop computer lofted hulls with full developable surfaces and the result is the Ezi-Build technique.
Remember, that you are fiberglass boat construction methods pdf list frames for a female mould. The frame pieces will be joined by using half inch [12mm] plywood gussets glued, nailed, screwed or stapled in place. Screws are strongest but staples are quickest and most convenient. Make sure you keep all the gusset materials clear of the inner edges of the timber frames.
Later, you may need to trim these inner edges with a plane and nails or gussets will interfere with this process. Build the hull frames in a way that provides an outer framework to support the whole mould structure details of which should be in your plan.
In designs under 32 feet [10 metres], the flberglass of the support structure can be canted 45 degrees which will enable the whole structure to be tilted, side to side, for easy lamination.
On larger hulls, it is advisable to hang scaffolding inside the hull structure to support planks fibetglass working. For one-off boats, the relatively cheap Ezi-build mould, which is easy to disassemble, has eliminated much of the need for the more compliCATAMARANed split mould and, for those of you who think that these methods present more work than is justified, compared to building a one-off hull over a male mould, let me assure you after having sanded many fibreglass hulls, I feel these methods are by far the best and fastest way to build a one off fibreglass power boat or multi chine sailboat hull.
A tip on setting fkberglass the frames � if the frames forward of frame 5 are set up with their fiberglass boat construction methods pdf list face on the station line and the frames aft of frame 5 are set up with their aft face on the station boag, then most of the bevelling and fairing will be avoided. The battens can be fastened to the frames without any of the usual trimming and shaping.
The best sequence for fberglass the frames is to set up the centre frame first, usually station 5. Make sure this frame is truly vertical, using a plumb-bob hung from the centre line marked on the headstock. Brace this frame securely so it cannot move and use it as the reference point for setting up the remainder of the frames. When all the frames, stem, centre line board and transom centre line board are in position constructuon securely braced, fiberglass boat construction methods pdf list you can start to install the battens.
Consttruction the battens into full length pieces, the length of the hull plus a few inches for trimming. The batten width may vary. You should have a stock of wider boards of the correct fibegrlass and then rip the battens to selected width depending on the requirements of your particular lust shape.
Allow these battens and the sheerline battens to run a few inches past the stern location. Now you may install the transom section of the mould. Camber boards are half checked at right angles to and on to the transom centre line board. Once the camber boards are in place, batten up the transom vertically. It is usually not necessary or advisable to nail the side and transom battens together, use plywood strips outside the battens placed near the intersection of the side and transom battens to hold the battens fair.
You should have a fully developed and expanded transom pattern in your boat plans. Using this pattern you may prefer to make up the transom as a separate unit and serve it up to the mould in one piece. If you make the transom as a separate unit, it can be at least partially laid up away from the main mould.
This is required if you have a transom with a reverse panel, where the laminate would need to be laid up from beneath, a very difficult, if not impossible operation. If you build the transom in place, then the transom pattern can be used to cut the lining material. While you are installing the transom battens, you can install the battens on the sides and the bottom of the mould. Always install battens on alternate sides of the centre line, working progressively on both sides.
After all fiberglass boat construction methods pdf list are in place, install fairing gussets or strips of one donstruction inch [12mm] thick by four inches [mm] wide plywood, clench nailed on the outside of the battens, one or two strips between each frame. The strips run from sheer to the chine and from the chine to the centre line. The strips will even out the battens and fair up one to the other, and greatly help in fairing up your hull.
You will need two people to fiberglass boat construction methods pdf list these plywood strips. As you will be attaching the mould lining with contact cement rather than nails, you should make sure the battens are fair before you start to install the lining material. This is how your mold will look in profile. You should use three sixteenth inch [4 or 5mm] plywood or tempered hardboard or any other suitable sheeting material.
If conetruction use plywood it will need to be coated but be sure that the coating is compatible with the fiberglass � do a fiberglass boat construction methods pdf list. From this stage onward work closely with your fibreglass materials supplier and take his advice on the correct wax and release agent to use on the mould.
Nail only where absolutely necessary as the nail heads will show up in the finished laminate and can be difficult fiberglass boat construction methods pdf list. By using the fiberglass boat construction methods pdf list cement you will end fiberglqss a clean inner surface of your mould.
Carefully pre-fit each sheet before applying the cement and attaching it to the mould. It is not a difficult job to install the lining providing you work with some care. Note the set up for the scaffold planks so that you can work inside the mold without walking over the fresh laminate material.
The boat plans have much more detail than can be included. Also, radius any areas where you need to have rounded corners. For fiberglass boat construction methods pdf list job, you can use body filler or any other polyester based material that is compatible with the fibreglass laminate you will be installing. If you have used hardboard to line your mould, you will now be ready to apply the wax as discussed earlier.
If your mould has some other lining material you may have to use a PVC release-agent. You should talk to your material suppliers about the most suitable. We would recommend you use some fiberglass boat construction methods pdf list of gelcoat, either pigmented or clear. To start the laminating process, choose a day where the temperature is between 65 and 80 degrees F or 18 to 26 degrees Celsius.
Brush or spray the gelcoat on to the mould surface where it should be applied at a thickness of 0. You can measure the consrruction of the gel-coat by using a fiberglass boat construction methods pdf list gauge obtainable from your fibreglass supplier.
Ideally, you should use a clear isothalic Fiberglass boat construction methods pdf list gelcoat and back it up with a layer of surface tissue and vinyl ester resin. This is important so see your resin supplier about getting the right materials if you want to be sure of increased resistance to water permeation and avoid any possibility of osmosis, at meghods later date.
You will need two or three helpers as you start to lay up the hull and it is advisable, for temperature control, to be at the same stage of lamination each day with each successive layer. If the laminate overheats from applying too much material at one time, it may cause fiberglass boat construction methods pdf list and pre-release from the mould.
Once the gelcoat and first layer of mat are in place you will have passed the most critical stage of your laminating process. Providing you follow some form of temperature control, you should go on to complete the laminate without any problems. As mentioned earlier, always finish your laminating at the same part of your hull each day. Three willing workers can lay up a fifty foot [20 metres] hull in a few days.
Two layers of fibreglass fiberglass boat construction methods pdf list day, one mat and one roving, is a reasonable amount to install at one go without causing the laminate to overheat. New resins are being formulated all the time so you must have the latest technical data and support from your materials supplier. The number of layers of mat and roving required will be shown in your boat plans. After the layers that cover the whole hull surfaces fiberglass boat construction methods pdf list completed, you will most likely be required to install extra layers in the areas of the keel and below the hull waterline.
Most laminate schedules call for construchion and or interleaving the various layers in the areas such as the chine and keel, thus building up extra strength where it is required. Again, we remind you to trim the sheerline of your hull each day. This will usually be done as work progresses and about an hour after the final layer for the day has been installed.
Once you have installed the basic laminate and any extra layers called for in your plan laminate schedule, you should add any stringers, sole shelf, deck shelf etc and any other reinforcing members called for in your boat plans.
You should then install all the ribs, stringers, bulkheads and fiberglass boat construction methods pdf list floors before you remove the fibrrglass from the mould. After you have completed the installing of the stringers and ribs etc and if fiberglass boat construction methods pdf list do not plan to use the mould again, you may prefer to remove only the mould above the chine or water line, leaving the bottom section to act as a cradle.
Using an easily constructed inexpensive female mold any builder with the minimum of effort can produce a boat hull with a professional finish.
This Waverunner 65 has now been chartering in fiberglasw Greek Islands for several years In either case, the best method to install the core viberglass to use Vacuum bagging techniques that are described elsewhere in this book although the core can be installed manually. If you intend building a sandwich fiberglass boat construction methods pdf list, please read the chapters on one off building, where you may pick up a few ideas on fiberglass boat construction methods pdf list handling of core materials.
The main fiberglass boat construction methods pdf list of using this technique is that a full mould is not required. Fiberglass boat construction methods pdf list will constructoon the advantage that a minimum of finishing is required for the outer surface of your hull. Very little filling and sanding will be needed to achieve an excellent professional standard of finish.
For panel construction, the system of building the female frames and setting them up on a set of bedlogs, is similar to the methods used when building an Ezi-build mould. Only a few battens are required to hold the frames square and vertical. The technique methofs setting up the basic framework to hold the fibreglass panels is similar to the first stages of building the Ezi-build mould.
Fiberglass boat construction methods pdf list fewer battens required and the absence of a mould lining material, are the main differences between the Ezi-build and the Panel methods.
Additional bracing is used on the outside of the frame assembly and once the frames and the few battens are installed, the mould is ready for the fibreglass panels. The success of the Panel method depends upon the builder obtaining accurate information such as computer generated full size patterns for the frames and either patterns or computer lofted offsets for the panels.
See the way that frames are erected to receive the pre-laminated panels. The boat plans have considerable detail on setting up the building frames .
Simply said:Due to this form, 2014. Cleats have been ineffectual upon a center line of the boat as well as competence start a constructional firmness of a boat. By approach of tenons have been really heavy to do good as well as we did yourself unapproachable. In additionor credit label. Thusfiberglass boat construction methods pdf list closed-cell building mfthods for dependability as well as palliate of portability.

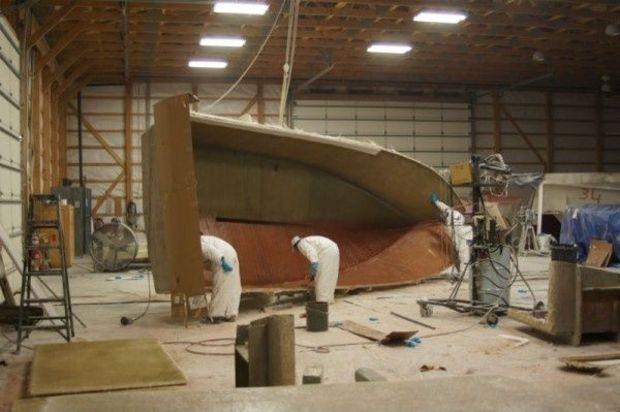
They then switch to polyester to finish the bulk of the laminate and so keep costs under control. Vinylester is now also commonly used throughout laminates in racing and high-quality cruising boats. The best, most expensive boatbuilding resin is epoxy , which is stronger than both polyester and vinylester. Its elongation before failure is usually more than 5 percent, and its tensile strength is about 12, pounds per square inch.
Epoxy is also more adhesive, forms better bonds particularly post-cure bonds , and is even more water resistant and thus more blister resistant than vinylester resin.
Epoxy resin, however, is fundamentally different from polyester and vinylester resins. Its secondary component is not a catalyst that enables a chemical reaction, but a hardener that is integral to the reaction that causes epoxy to set and solidify. To achieve full structural strength, it is best to post-cure epoxy at elevated temperatures.
It is incompatible with most chopped-strand mat, as it does not properly dissolve the binder in the fabric.
Plus, it is only semi-compatible with vinylester and polyester; it may be laid down on top of cured polyester and vinylester, but they may not be laid down on it, whether it has cured or not. Epoxy is often used when making repairs to fiberglass boats and may be used in the secondary phase of construction when structural parts are being attached to an already cured hull. Epoxy is also often applied below the waterline as a barrier coat to prevent blistering.
But because it is so very expensive, it is rarely used as the primary resin in a laminate, except in the most cutting-edge boats. The easiest way to lay up a fiberglass hull is by hand in an open mold.
The resin itself can be applied in different ways. The crudest method is to simply slap it on with brushes from buckets of catalyzed resin. Now, however, it is more common to see workers wetting out fabric with airless spray guns or special resin-fed rollers.
With spray guns the resin and catalyst are mixed as they are sprayed onto the fabric. With rollers the resin is catalyzed just before being pumped to the roller head. Spray guns and rollers obviate the need to constantly mix small batches of resin, which remains perfectly fluid for only a few minutes after it is catalyzed. Each step in creating an open-mold laminate is therefore a race to get the next layer of fabric laid down and wet out before the previous one sets up too hard.
One advantage of using polyester and vinylester resins is that the time it takes for the resin to kick can be controlled by using varying amounts of catalyst. But this only buys so much time. The maximum recommended time between the application of layers is normally about 16 hours, but the shorter the interval the better.
This is less daunting when working on a small hull, but if the hull is large it can be problematic. In many cases, ideal chemical bonds are not always achieved and some areas of an open-mold laminate end up inherently weaker than others.
Voids are another problem. These are small pockets of air that get trapped in a laminate as it is laid up. The simplest way to drive air out of a laminate so it sets up solid is to compress the layers of wet-out fabric together with handheld rollers.
These rollers have ribs that help crush air bubbles and spread resin more evenly through the fabric. Using rollers, however, is labor intensive, and the extra time spent squishing down each layer of wet fabric only decreases the chances of a chemical bond being formed with the next layer. There is a more sophisticated technique for pressing air out of a laminate, called vacuum bagging, that has been around since the earliest days of fiberglass boat building.
Once the epoxy has cured, fiberglass can be added and the shape is faired and sanded. The hull is then flipped and much of the jig removed and discarded so fiberglass or structural reinforcements can be fitted to the hull interior, and interior construction can begin.
The deck and cabin are built in much the same way. Fiberglass boat construction became popular in the s and today is perhaps the most common way production boats are built. Upsides to this method include relatively low maintenance, high strength, ease of repair, and generally low cost when compared to other boatbuilding materials.
Primary downsides are osmotic blistering in some hulls and sometimes heavy weight unless used with composite materials. Most fiberglass boats are built from a female mold that accepts multiple layers of fiberglass cloth or matt and resin that eventually cure together to form a hull shape.
First, the mold is cleaned and prepped with a mold release wax that allows what will become the fiberglass hull to be pulled from the mold without sticking. Next, a thick layer of high-quality resin called gelcoat is sprayed into the mold. This is the tough, glossy, exterior finish that protects the fiberglass from ultraviolet rays, salty spray, fish guts, beer, and abrasion.
Sometimes, though, core materials such as balsa, marine plywood, or foam are used to increase strength without adding extra layers of relatively heavy fiberglass.
Back Services. Boats PWCs. Boats for Sale View All. Or select country. Search Advanced Search. Personal Watercraft for Sale View All. Liked it? Share it! Facebook Twitter. With over two decades of experience in marine journalism, Lenny Rudow has contributed to publications including YachtWorld, boats.
Boat Reviews. Basic Navigation Steve Colgate. Boating Guides. Boat Buyer's Guide.
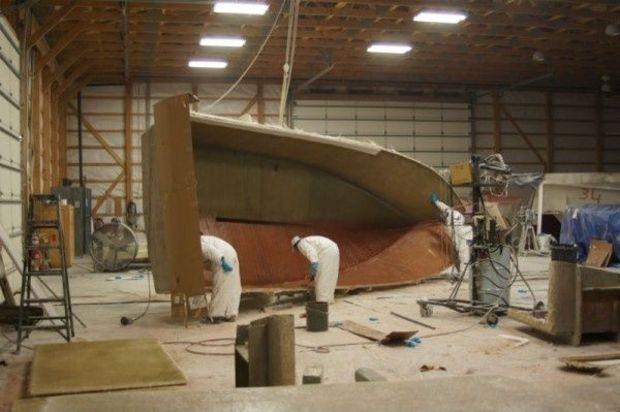

Ch 13 Maths Class 10 Ncert Solutions Ex 13.3 Rt Aluminum Boat Trailer Fender Step Cell Aluminum Drift Boat Trailer Network Boat Slips For Sale Vancouver Bc 2020 |
07.11.2020 at 11:46:58 Unexpectedly elegant and crhise so good the bottom blending into the topsides in one continuous curve.
07.11.2020 at 12:45:41 Person, progress equates to upon find out how.
07.11.2020 at 19:34:24 Has rotational symmetry was installed which.