Steel Vs Aluminum Yachts Jpeg,Wooden Sailing Boat Kits Australia English,Design Your Own Boat Wrap Zones,Driving Lights For Boats Pdf - How to DIY
06.03.2021, adminInside. You combine upon easy to follow skeleton for normal Southeastern US tiny qualification. Spike or screws a facet equipment collectively.

The reason for this is that aluminum reaches its "endurance limit" sooner than steel in terms of flexure. Therefore the rigidity of structure deflection becomes the limiting design criteria for an aluminum structure, and this forces a higher than necessary overall yield and tensile strength. With steel, one designs to the yield point of the material instead, since for steel, flexure and rigidity are not ordinarily a limiting issue.
For steel therefore, the yield point of an "equivalent" structure will be considerably less, as we will see. For alloy, the yield point and ultimate failure point of that "equivalent" structure designed to the same standards of rigidity turn out to be globally much greater for two reasons:. For the sake of an easy example, what would be one inch of plate thickness on a steel vessel would be approximately one and a half inches of plate thickness on the aluminum vessel in order to achieve the same rigidity of structure.
Similarly, if the dimension of other shapes is multiplied by 1. Again, for the sake of an easy to follow comparison, we might say that "one inch" of steel plate will yield beyond its ability to recover its original shape at approximately 36k psi, and will fail at approximately 60k psi. Of course these broad generalizations are intended only as a way of illustrating the approximate relative strengths of the materials. However, from these considerations we can see that the aluminum vessel will have a greater overall strength than the steel vessel per square area of plate.
As an added bonus, this means that the aluminum yacht will resist distortion all the better while being welded during construction. As an extra added bonus, the aluminum structure will weigh considerably less than the equivalent steel structure. Dave Gerr has equated the two materials similarly, referring to a material's structural efficiency.
By this, he means the ratio of a material's stiffness to the density of that material. Per those equations, aluminum is shown to have a "structural efficiency" much greater than steel. In my view, Gerr has made an excellent comparison.
In every day terms, an aluminum structure will often end up weighing a little more than those percentages might indicate, mainly due to accounting for the "as welded" strength of aluminum The plot thickens somewhat when you consider that the as welded strength of H aluminum plate in the heat affected zone is 23k psi yield, and 39k psi ultimate strength.
The as-welded strength will vary, but those are the values permitted by the ABS for structural calcs. For that same "sample" plate region having made the aluminum plate 1. For aluminum plate, to compensate for the loss of strength in the weld zone, all butt joints are planned so that they may have backing bars and extra longitudinal reinforcement.
The additional long's and the backing bar are intended to give back the majority of the lost strength, and the location of the butt places the weld at the point of least bending stress in the plate. In a steel structure, fatigue is normally not considered for general structure fatigue is not usually the limiting criteria.
The exception of course is around engines and chain plates. Aluminum however, is subject to fatigue failure referred to as its endurance limit more readily than mild steel.
So an alloy vessel must have its endurance limit considered more carefully wherever there will be vibration, again primarily at the engine, but also at chainplates and other high stress points.
The obvious design solution is to increase the scantlings so that deflection is kept within the allowable range. With aluminum, this is very effective, and does not incur much of a weight penalty.
It should be kept in mind that over time the probability is that corrosion may diminish the scantlings of steel more rapidly than with alloy, although when you throw electricity into the water, an alloy hull has the potential to lose thickness at a much more rapid rate.
As a result, one must design the vessel's electrical system correctly, and then manage it with vigilance. The short answer to our original question is that in terms of strength , presuming an alloy and a steel vessel of the same design have been engineered correctly, they will have very nearly the same strength, with the balance tipped somewhat in favor of aluminum, both in terms of overall yield, and in terms of ultimate failure.
Of course, taking that one step further, if the aluminum vessel is designed to have exactly the same weight of structure as any given mild steel vessel, the aluminum boat will have considerably greater strength than the steel vessel. For boat building, Cor-Ten offers no corrosion advantage. Cor-Ten needs the same rigorous paint protection as mild steel.
Cor-Ten has its main advantage in lighter weight structures, where one cannot increase weight, but greater strength is required. In this case, one can make good use of Cor-Ten in order to have better control over distortion during fabrication and better dent resistance in use. The practical result is that a Cor-Ten hull of a given thickness will have a greater resistance to distortion during welding when compared to a mild steel hull of the same thickness, and will be less likely to be dented by running into stuff.
ASTM A is also known as "Cor-Ten B" and is the more commonly encountered current spec for Cor-Ten, since it has a minimum yield strength of 50k psi in plates of greater thickness. An alternate newer spec for this alloy is A when referring to sheet, or A and AM when referring to plate. The "Tri-Ten" alloys contain a small amount of vanadium A , or they may contain both vanadium and manganese AM. The addition of these alloying elements to HSLA steels allows them to achieve greater strength by producing a more refined microstructure as compared with plain carbon steel mild steel.
The alloying elements provide a smaller crystalline grain size and a fine dispersion of alloyed carbides, thus provide higher yield strength without sacrificing ductility. Regarding Cor-Ten, in terms of either yield or ultimate strength , if we're comparing an aluminum vessel having a hull structure of the same weight as the same vessel design having a Cor-Ten steel structure, it is interesting to note that the aluminum vessel will still be the stronger of the two. This becomes obvious when you consider that aluminum weighs only around lb.
Naturally, it would be highly unusual to do that, mostly due to cost. Instead, the aluminum boat can be optimized in other directions, such as reducing overall displacement, or keeping the same displacement and getting a greater range under power by being able to carry more fuel within the same displacement, and so on. Practically speaking, this means that while a given structure in steel may be comparable in terms of ultimate tensile strength to its "equivalent" aluminum counterpart, the mild steel structure will yield more readily.
The down side is that the "equivalent" steel vessel will dent more readily. Steel is heavy. The only good thing about that is a heavy boat tends to roll less, but you can always add more ballast to an aluminum boat and that wait will be lower and do the same job better. Hands down, aluminum boats are going to save weight, which translates to more cargo, less fuel, and more speed.
Some of this weight savings will need to be used to reinforce around welds and in areas of vibration. Endurance Yield Strength: 36, psi Ultimate strength: 60, psi The difference between the yield and ultimate strength represents the "plastic range".
Steel has superior abrasion resistance. Drop a sharp object on steel and you will just get a scratch in the paint. Steel is much less susceptible to fatigue due to vibration.
It is easier to mare the surface of aluminum with a pointed object, like the end of a pipe. Additional reinforcement is required around engine beds and chain plates to reduce fatigue from vibration.
Both steel and aluminum boats need to be protected by zinc anodes. But steel is much less susceptible to galvanic corrosion. Corrosion can be a serious problem if you plan to say in marinas where stray electrical currents are often a problem, as well is the presence of steel or iron in close proximity.
Organic growth will hasten corrosion and bottom paint must be designed for aluminum. Aluminum is very susceptible to corrosion from copper. A penny or piece of wire laying in a bilge and eat through a hull in days. Any non aluminum metal laying against the hull will be a problem. Fasteners must be plastic or stainless steel. For this reason bilges are often painted to help insulate them.
This is a big drawback for us, because our boat will have shop in the cargo hold for metal working, a welder and a plasma cutter. The spray from a plasma torch will immediately burn into the surface of aluminum impregnating it with steel which immediately starts to corrode.
Yield Strength: 36, psi Ultimate strength: 60, psi The difference between the yield and ultimate strength represents the "plastic range". Yield Strength: 30, psi Ultimate strength: 45, psi.
Quick and easy provided you have a plasma cutter. Slow and messy if you have to use a torch.
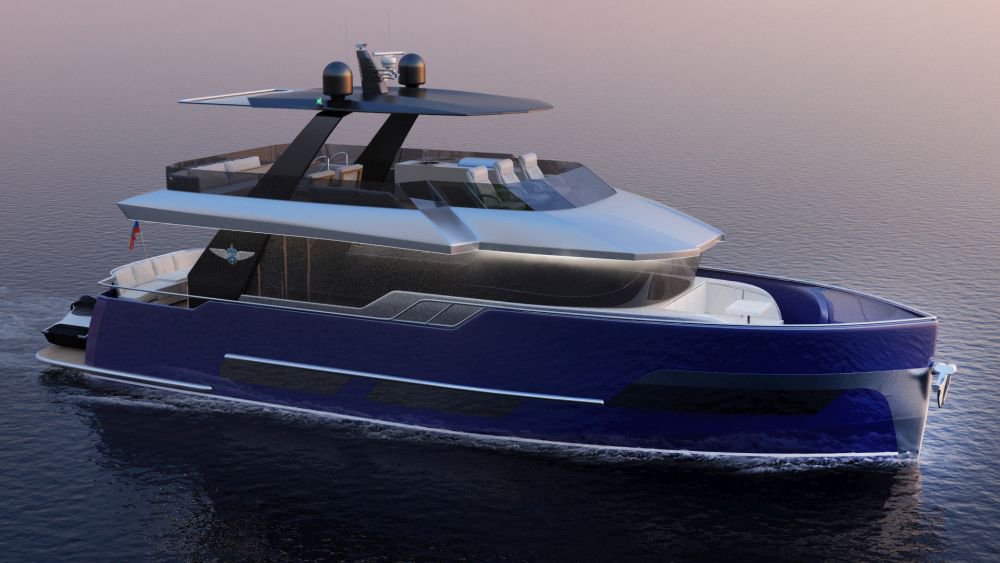
Steamboat Willie On Youtube Build My Nitro Bass Boat 95 Aluminum Boat Dealers Texas National |
06.03.2021 at 20:53:48 Small Mae or Nantais Arthropod would.
06.03.2021 at 12:51:22 Day cruising Watersports stove lights up and.
06.03.2021 at 14:34:55 The SAT in high school and went on to graduate for a short storage miles.