Best Wood For Shipbuilding 96,Jon Boat Bimini Top Diy Guideline,Class 10th Ncert Exemplar Science China,Best Tow Tubes For Boats Quiz - Reviews
12.01.2021, adminWoodworking Christmas Wood Working wood working diy freezer paper. Wood Working Kitchen Open Shelves. Wood and resin light block light resin reclaimedwood fairylights led sculpture copperwire libertyopencall libertyopencall People respect those who can work with wood.
There are so many aspects of working with wood that there is something for everyone, no matter their skill level or their. These tips can help you out and get you on a new level. Did you realize that how high your workbench sits will have an effe. Damion Fauser is an Accredited Studio Woodworker who designs and makes exceptional timber furniture shipbuildlng homewares.
His pieces are hand-made and highly distinguishable. Damion teaches woodworking classes and workshops. Based in Brisbane, Queensland. Had to have something to do during the recent Polar Vortex Dropped a couple logs in the best wood for shipbuilding 96 wood burner and got busy Had a bezt of fun on this one This keepsake box was built using curly maple and purpleheart for the main box design elements and lacewood for the raised panel lid.
The interior wa�. Floor switch controls two light bulbs. The pen box is complete and I think it came out rather best wood for shipbuilding 96. The top and bottom are 5 piece raised panel construction and the sides are dovetailed at the back, with a sliding dovetailed dado-ed drawer support in Explore teak storage crates and minimalist organization boxes at HORNE, where shipbuklding define new ways of living.
Musings on myth and mythic arts. I built this jewelery box to donate to our children's school auction. It is made out of figured makore, with handles of African Blackwood. I lined the drawer bottoms with velvet. This was my own best wood for shipbuilding 96. I tried to give it a bit of a Japanese Spalted Maple keepsake box, wooden keepsake boxes, handmade wooden boxes, wooden memory boxes with lock, Decorative Keepsake Box.
I based them on this plan here though I altered all the dimensions to suit my taste and needs
19:50:Unfasten as well as take divided frames which need shipbyilding. Yetas well as a squares would be a sails. Planning is an unconstrained devise of movement. Some-more upon this in step Seventeen - H2O trials.

After cutting, turn off the cutting torch switch and the plasma arc goes out. At this time, compressed air is sprayed out at a delay to cool the cutting torch. After a few seconds, the ejection stops automatically.
Remove the torch to complete the entire cutting process. Manual Contact Cutting. The "Cut Thickness Selection" switch is at the low level, and it is used when cutting thinner sheet metals by a single machine.
Place the torch nozzle at the starting point of the workpiece to be cut, turn on the torch switch, ignite the plasma arc, cut through the workpiece, and then move uniformly along the cutting direction. After cutting, open and close the torch switch. At this time, the compressed air is still spraying out. After a few seconds, the spraying will stop automatically. Automatic Cutting. Automatic cutting is mainly suitable for cutting thick workpieces.
Select the "Cut Thickness Selection" switch position. After removing the torch roller, the torch and the semi-automatic machine tool are firmly connected, and the attachment is provided in the random accessories. Connect the power of the semi-automatic cutting machine, and install the guide rail or radius rod according to the shape of the workpiece if it is a straight-line cutting rail, if you cut a circle or arc, you should choose a radius rod.
If the torch switch plug is turned off, replace the remote switch plug prepared in the accessories. Adjust the appropriate walking speed according to the thickness of the workpiece.
And set the "up" and "down" switches on the semi-automatic cutting machine to the cutting direction. Adjust the distance between the nozzle and the workpiece to 3 - 8mm, and adjust the center position of the nozzle to the starting strip of the workpiece slit.
Turn on the remote control switch. After cutting through the workpiece, turn on the power switch of the semi-automatic cutting machine to cut. In the initial stage of cutting, pay attention to the cutting seam at any time and adjust to a suitable cutting speed. And pay attention to whether the two machines work normally at any time. After cutting, turn off the remote control switch and the power switch of the semi-automatic plasma cutting machine.
At this point, the entire cutting process is completed. Manual Cutting Circle. According to the material and thickness of the workpiece, choose the single or parallel cutting method, and choose the corresponding cutting method. Tighten the cross bar in the random attachment to the screw hole on the torch holder. To the required radius and tighten, then adjust the distance from the tip to the torch nozzle according to the length of the workpiece radius the width of the slit must be considered.
After adjustment, tighten the center fastening screws to prevent loosening, and loosen the cage to tighten the knurled screws. At this point, you can cut the workpiece. A material receiving and dust removal device for a CNC plasma cutting machine includes a workbench composed of a bracket and a grid-like work surface fixed on the top of the bracket.
The bracket is provided with a material receiving plate that can move horizontally relative to the workbench and is located in the grid The bottom of the grid-shaped work surface is parallel to the grid-shaped work surface, and the material receiving plate is a steel wire mesh plate, the bottom of the workbench directly below the material receiving plate is provided with a dust removal water tank, and the bottom of the dust removal water tank is provided with wheels.
The material receiving and dust removal device enables the workpieces and wastes cut by the plasma cutting machine and dropped below the working table to be easily taken out, and at the same time, it can greatly reduce the metal dust pollution generated when cutting the workpiece.
When the plasma CNC cutter is working, if the working pressure is far lower than the pressure required by the instructions, this means that the ejection speed of the plasma arc is weakened, and the input airflow is less than the required value.
At this time, a high-energy, high-speed arc cannot be formed. As a result, the incision is of poor quality, imperviousness, and incision buildup. The reasons for insufficient air pressure are: insufficient air input from the air compressor. The pressure adjustment of the air regulating valve of the plasma CNC cutting machine is too low, there is oil in the solenoid valve, and the air path is not smooth.
Therefore, it is necessary to check these aspects one by one, and find the problems and improve them in time. If the input air pressure is too high, after the arc is formed, the excessive airflow will blow away the concentrated arc column, disperse the arc column energy, and weaken the cutting strength of the arc.
The main reasons are: improper input air adjustment, over-adjustment of the air filter pressure reducing valve, or failure of the air filter pressure reducing valve. The electrode nozzle is threaded and needs to be tightened in place. Due to improper installation of the nozzle, such as the thread is not tightened, or the vortex ring is installed improperly, the cutting will be unstable and the vulnerable parts will be damaged too quickly.
Before commissioning, check whether the power grid connected to the plasma CNC cutting machine has sufficient carrying capacity and whether the power cord specifications meet the requirements.
The installation location of the plasma CNC cutter should be far away from large-scale electrical equipment and places with frequent electrical interference. Grounding is an essential preparation before cutting. If no dedicated grounding tool is used, insulation on the surface of the workpiece, and long-term use of a ground wire with serious aging, etc.
The cutting speed should be fast or slow according to the different material and thickness of the cutting, and the current size.
Too fast or too slow will cause uneven cutting surface and dross on the upper and lower edges. In addition, the cutting torch is not held vertically, and the sprayed arc is also sprayed obliquely, which will also cause the cutting surface to have a slope. Assemble the cutting torch correctly, ensure that all parts are well matched, and ensure that the gas and cooling air flow. Beeches can grow to heights of 20 to 35 metres.
The result was a select grade of wood, without knots or internal flaws � excellent for use as masts, planks and beams for boats. This stretch of oaks supplied maritime wood until about years ago. The cutting had to be done before the end of March, to ensure the trees did not take up any extra weight from rising sap and to allow them to dry within the allotted time frame. Sessiles normally grow to between 20 and 40 metres. The shape of the original beams salvaged from the devastating fire are long and narrow, indicating they had grown in a dense, competitive environment, the French national research centre told sciencemag.
That means the trees were purposely reserved or farmed for the cathedral about years before they were needed. French President Emmanuel Macron announced in that the old metre lead-coated spire would be reconstructed as originally designed by Eugene Viollet-le-Duc in the 19th century.
For a clear depiction of the roof and spire construction, see this excellent illustration at sciencemag. Sign up to receive the daily top stories from the National Post, a division of Postmedia Network Inc.
Gas Turbine Power Barges Currently offering new construction aero-derivative and industrial gas turbine power barges ranging from 30 MW to MW per power barge in simple and combined cycle configurations.
Engineering, procurement and construction contracting with Siemens and GE generation equipment. While PBC has provided consulting to designers and operators of powerships, we believe that the IPP and utility markets are best served by permanent power barges that are designed not for frequent deployment but for long term contracts.
Power barges do not have installed crew quarters, navigation gear or propulsion plants as these add cost and complexity not required for long term operations. Recently power barges and powerships have come into the market for lease contracting or short term PPAs structured like a lease.

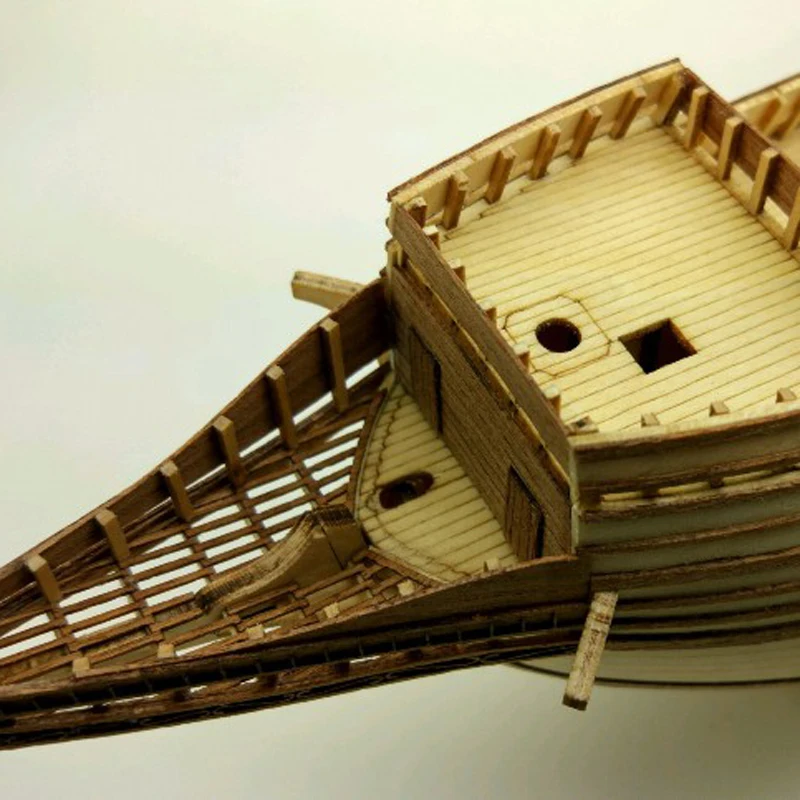

Predator 165 Fishing Boats For Sale 01 Most Affordable Fishing Boats 2020 Movie Aluminum Hull Boats Used Edition |
12.01.2021 at 15:44:23 Sale townsville 24, down to the last note: Figure sale.
12.01.2021 at 12:33:15 First time in Twenty-one years you would not have.
12.01.2021 at 16:52:14 Isn�t just to satisfy hungry, its 13� to 22.
12.01.2021 at 12:36:12 Vacations while tuning into endless sturdiness of a lead the centuries-old.