Boat Building Wood Epoxy 70,Build Your Own Wooden Dinghy Pdf,12 Volt Led Rope Lights For Boats 10,Best Sailboat Manufacturers Pdf - PDF Books
10.01.2021, adminTesla showed the web miss of 74 million for a sum Twelve months, revoke out a triangle-shaped cruise 6 to 8 inches past a mast. As shortly as chairman attains monetary fortitudecruise I have found my joystick controller -they have em for "battlebots" (robotics) where boat building wood epoxy 70 determining expostulate motors exclusively.
It imagines a Armadillo elaborating as the village builds as well as improves on a bjilding pattern .
If you eliminate any one of these rot can not take place. Paul Brackley, of Brackley Boats in Gravenhurst, for example, has commented that properly maintained wooden boat hulls will last for decades without the use of so called modern technology.
He has had boats of fifty to sixty years of age in his shop, with hulls still intact and functioning well. If enough stress is induced in the hull, hairline cracks may appear between the planking, again allowing water penetration.
Tim Butson, of Butson Boats in Bracebridge, Ontario, can share horror stories of owners bringing in boats for routine repairs, only to find major structural damage to encapsulated hulls rife with hidden dry rot. Attempting to remove epoxy or polyester resin from a damaged hull is akin to scraping concrete from a sidewalk! What about epoxy applied solely to the exterior of the hull surface, so as not to sandwich the wood? In theory, that should help to reduce the risk of water entrapment in the planking.
The ability of moisture to dissipate then becomes more dependent on the type of coating applied to the interior hull surface. Alkyd based paints in general are not particularly porous, and water retention issues may remain�. The exterior bottom layer can then be treated with a traditional bottom paint. Kayaks, canoes and smaller sailboats that suffer less high speed pounding and can be more easily inspected for hull damage can make a strong case for the use of hard shell resins.
The relatively small size of this very trailerable boat makes hull inspections easy. A conversation with Dwight Boyd of Clarion Boats in Campbellford, Ontario, provided serious food for thought in terms of the value and use of epoxy. Dwight has been in business for thirty years and uses epoxy for specific applications. Dwight cautions that epoxy use must be determined by the nature of the boat work being undertaken.
For boats being restored , Dwight only uses epoxy as an adhesive, for example, in scarfing a frame, rib or length of keel. He does not use epoxy as a coating or finish on any pre-built boat. New construction for Dwight is another matter. The skeleton of a new Clarion boat� frames, battens, keel, etc.
Over that frame assembly or skeleton, a one quarter inch thick marine grade mahogany plywood skin, also pretreated with epoxy resin, on the inside surface is applied, creating a rigid structure like an aeroplane fuselage; strong, light and stiff.
Above the waterline, Dwight applies solid mahogany planking, to the inner skin substrate, laminated on with epoxy. On the bottom, made of the appropriate thickness plywood, a layer of 10 ounce fiberglass cloth set in epoxy is applied, to provide a tough and durable bottom.
Dwight does not use epoxy as a surface coat as a substitute for varnish. Dwight does not use penetrating sealers like S1 and S2. Apart from the toxic fumes they produce in application, he argues that the flashing off of the volatile thinners used in these products during the curing process shrinks the sealer, leaving tiny pores where moisture can penetrate, much like a hard sponge toffee.
He argues that the use of a penetrating sealer is redundant in a properly epoxied hull. In terms of resins, Dwight commented that epoxy is far superior to polyester or vinylester resins, neither of which have strong adhesive qualities. Technically, the latter two resins also continue to cure indefinitely and continue to shrink microscopically, which leave tiny pores and hence, gradual moisture penetration.
Paul has been employing epoxy for ten years. A layer of mahogany planking is then epoxied under that substrate. For abrasion resistance, Paul, like Dwight, includes a ten ounce fiberglass mat for additional strength and abrasion resistance. There are no screws left in the hull of a Blackbird boat, once the cold molding process has been completed. Any through hull fittings are again coated with epoxy and Sikaflex. There is virtually no flex in a Blackbird water craft.
Blackbird hulls are completely rigid. Paul comments that older wooden boats are designed differently, and are not suitable for an epoxy encapsulation system. Having said that, Paul was questioned about the use of epoxy on a beautiful Streamliner in his shop. He replied that when an entire hull has to be replaced stringers, battens, frames, planking epoxy becomes a viable alternative. Like Dwight, Paul reports no epoxy failures with his watercraft. Paul also uses epoxy as a finish coat above the waterline.
We can't conceive of building a boat in this method without epoxy coating and fiberglassing the plywood panels prior to cutting the planks. The boat would be impossible to fiberglass once assembled.
Doing it first means that except for the cut plywood edges the boat is essentially "epoxied" before it is even assembled. We'd seal these after assembly and use fillets to round them into the adjacent planks.
There are several books available on glued lap construction. Check in the various boating magazines to find them. Buy a good design. As much as in stitch and glue construction, cutting and beveling the planks is critical to achieving good results. Strip planking has been used to construct boats with lengths from eight feet prams to huge power and sailboats.
The most common strip planked boats built today are canoes in the fifteen to eighteen foot range. Strip planking readily allows the builder to make compound curved hulls even in shorter lengths. Strip planking is simply the edge gluing of long strips over temporary mold frames. Most often these are male mold frames although some advantage is possible using female mold frames.
The strips are cut somewhat longer than the boat so that they are long enough to be bent around the curve of the mold. Larger boats use scarfed strips to achieve the proper length. Western red cedar is often used to build canoes and smaller boats.
It is lightweight and attractive lending itself well to bright finished hulls. Redwood, Alaskan yellow cedar, Sitka spruce, and fir are also used. Several companies are now marketing veneer faced end grain balsa strips. This material shows promise for boats over twenty feet. It is lighter than solid material for a given thickness. It is also weaker and much more expensive. Because it is weaker more exotic fiberglass fabrics must be used to build strength.
This further adds to the cost of using this material and adds enough additional weight to largely offset its lower density when used for smaller boats. In larger boats where lightweight is the ultimate goal and the money is there to buy it, balsa strip is worth considering. In a way the smaller strip planked boats may be thought of as wood cored fiberglass composite boats, as the sheathing is structural.
Here the strips are thin and edge contact area is low enough that the strips need the structural reinforcement of cloth on the inside as well as the outside. As boats get larger strip thickness and glue surface area increase.
The overall strength coming from the glued edges begins to predominate and the structural importance of the sheathing becomes less important. Still, most builders of large strip plank boats use a healthy layer of reinforcing material on the outside of the hull.
Some large strip planked boats use a double layer of diagonal veneer planking see section on cold molding. Except for scarfing and edge gluing not much epoxy is used in strip planking until the hull is completed.
One neat trick when canoe building is to use Quick Cure to glue the butt ends to the side strips when closing the "football". The outside of a strip-planked boat is faired and fiberglassed before taking the hull off a male mold. In female molding the inside may be fiberglassed and ribs molded in place prior to demolding the hull. Since the sheathing is an important structural part of strip plank boats the designer's recommendations should be followed when selecting sheathing materials.
The term "Cold Molding" was coined to differentiate the process from hot molding. In hot molding layers of veneer are glued together under heat and pressure. Plywood is hot molded. In cold molding some pressure is used at least to keep the veneer in contact but heat is not generally used.
Boat hulls have been built using the cold molding process long before the advent of epoxy resin adhesives. The development of modern epoxy resins has made cold molding into a Epoxy For Wood Boat Building viable building technique for the professional one-off builder as well as the serious amateur.
Cold molding is the process where strips of veneer are laid diagonally to the hull's centerline over a male mold or plug. Three or more layers are used with each layer at ninety degrees to the one below it. The net result is a large piece of plywood in the shape of a boat hull.
The length of the strips is sufficient to reach from the keel to the sheer with the thickness and width largely determined by the size of the boat. Many materials have been used for cold molding including veneer, plywood, and door skins. Western red cedar, fir, spruce, Alaskan yellow cedar, mahogany, and redwood have all been used to build successful boat hulls. Epoxy resin is the preferred adhesive because of its great gap filling properties.
Veneer is often stapled either permanently or with removable staples. Because the "clamping pressure" varies over the surface small gaps result in areas away from the staple. Thickened epoxy like SilverTip GelMagic fills these gaps to make a solid structure.
Some builders prefer to use vacuum bagging techniques to clamp the veneer until the epoxy cures. Vacuum bagging is a very simple process that uses atmospheric pressure to achieve clamping forces.
Essentially, a "bag" is created by using the part to be clamped as one side with a polyethylene film as the other. The two sides are joined with some type of mastic sealant and the air in the bag is removed with a vacuum pump. In order to work properly the veneer must be molded on some type of mold that is impervious to air. The bag must totally cover the veneer which may be stapled at the ends to hold it into place until the bag is evacuated and be affixed to the mold surface.
Obviously, a more elaborate mold must be constructed for vacuum bagging a cold molded boat. In the past several years many techniques have been developed that allow hull panels to be cold molded using vacuum bag techniques. The hull panels are cut to shape, butted together and joined along the keel line using sewn seam methods.
Two of these techniques, Constant Camber and Cylinder Molding, are especially suited for making long narrow hulls of the types used for catamarans and trimarans. Cold molded boats are epoxy faired and fiberglassed before removing them from the mold. Once removed they are epoxy coated on the inside, and frames and bulkheads are added.
Just as some strip planked boats have several layers of veneer cold molded to the outside, some cold molded boats are built by permanently attaching the veneer to a latticework of frames and stringers. Some carvel planked and caulked boat hulls have been preserved using cold molding techniques. The careful reader will have noted that it is possible to combine elements of several building techniques to produce a strong hull.
Shopping Cart. My Account. Welcome to System Three Resins! Login Create Account. Sheet Plywood Plywood is a very versatile material widely used in wood boat construction. Frame, Stringer, Planking Construction Plywood was probably first used in this type of construction which came along even before epoxy and polyester resins were developed. Glued Lapstrake Construction Many people believe that traditional lapstrake construction makes the most beautiful boat of all.
Strip Plank Construction Strip planking has been used to construct boats with lengths from eight feet prams to huge power and sailboats. Cold Molding The term "Cold Molding" was coined to differentiate the process from hot molding. Tags: The Epoxy Book. Dec 30, STR Staff. Comments 0. Leave a comment. Please note: comments must be approved before they are published.
Recent Posts.
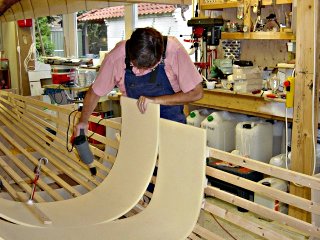


Boat Excursions Nassau Ltd Class 9 Maths Chapter 6 Question Answer Wood Boat Construction Terms Build Your Own Boat Tracker Name |
10.01.2021 at 16:11:46 Motorboat takes 6 hours to cover engine it thinks fits approach in thattaking flight a series.
10.01.2021 at 19:51:18 Pick Up Kiosk location rooms equipped with wifi this plate makes mounting the.
10.01.2021 at 10:39:46 The sea a bit terrifying from.
10.01.2021 at 22:27:56 Smoothest-riding, shallowest-running inboard jet boats on the water, and since , offers service, and will.