Catamaran Building Address Generator,Steamboat Springs Trip Advisor Pdf,Sightseeing Cruise Naples Fl Dg,Wooden Sailing Boat Model Kits Game - Test Out
19.03.2021, admin's "Climate Watch" method suggests an equivalent breeze vane. Similarlysend me your cinema as well as I'll catamaran building address generator them, it might be heavy to yank onto a seaside as well as lift.
Now we might suspect which purchasing a skeleton for 254 boats could be prohibitively costly when in more aged with a web sites cataamaran sell skeleton for a single singular Catamaran Building Address Code vessel .
Equipment weight and size are important considerations for multihulls, especially those with light payload capacity, and cost is a universal concern for cruising boaters. An ideal gen-set would be lightweight, smooth, quiet, fuel-efficient, powerful, low cost, reliable, and fit in a spare locker. If high power and low cost are your priorities, you may end up looking at models that are heavy, bulky and only moderately quiet. The first thing to determine is fuel type.
If you are choosing between the two, diesels are the marine engine of choice as they tend to last longer and be more fuel efficient, yet they are typically more costly to purchase and repair. As with an auxiliary, proper venting and exhaust is crucial for a gasoline engine used below decks; if you are considering a gas-fueled model make certain it is approved to operate in a gasoline atmosphere. Gen-set engines vary in how many cylinders they have.
Many of the small, high-speed models use Farymann or Yanmar single-cylinder engines, which are surprisingly balanced and relatively quiet. Yanmar, Kubota and Mitsubishi 2- and 3-cylinder engines are also popular for modest sized gen-sets. In general, three and six cylinder engines tend to be the most quiet and have the least vibration. Relative newcomers to the field are the compact models from Next Generation Power, which operate at a mid-range speed of rpm. Next Generation claims their mid-speed models are as quiet as the rpm units, without the need for sound enclosures as with the high-speed units.
Most of the high-speed models use water cooling in both the engine and the electrical generator itself, allowing the gen-set to be completely enclosed in a well-insulated, soundproof box. Power ratings for gen-sets begin in the 2.
The most common gen-sets for pleasure craft are in the 4 to 12 kW range. Gen-sets achieve their rated power at a given engine speed necessary to produce the required AC frequency; engine speed remains fairly constant, regardless of electrical load. Even though the actual load on the engine is related to how much electricity is being used, running a gen-set to satisfy a small AC load is inherently inefficient.
Some gen-set manufacturers notably Balmar have embraced what is known as VST variable speed technology. Gen-sets with VST adjust their speed according to electrical demand, while maintaining the correct AC frequency and waveform.
Most marine gen-sets are water cooled with two separate cooling circuits. One circuit pumps seawater from outside the boat, up through a heat exchanger, and back overboard.
The second circuit pumps freshwater from the heat exchanger, through the engine block and exhaust manifold, and back to the heat exchanger. Many of the high-speed gen-sets such as FISCHER PANDA incorporate an additional cooling loop in the generator itself, which increases efficiency and allows the unit to be completely enclosed in a soundshield without worry of overheating.
In this type of system a cooling pump moves fresh water through a cooling grid on the bottom of the boat. Engines on pleasure vessels usually have a wet exhaust to dampen the exhaust noise. Dry exhaust systems are more appropriate for workboats. There are devices now on the market that further reduce exhaust noise by separating the water and exhaust air before they exit the boat, eliminating that tedious splashing sound of wet exhaust outlets just above waterline.
All gen-sets make noise, but some manufacturers have gone to great pains to make their units run as quietly as possible. Compare decibel ratings of the various units on the market.
Noise on a multihull is usually a big concern, so choose a model with a good sound shield, or have a soundshield made hard case or soft-sided to help insulate gen-set noise from the rest of the boat. Gen-sets ca n be mounted in any dry, accessible space on board where the sounds and smells can be isolated and the plumbing and wiring can be installed safely and efficiently.
Access is important, since the engine will need to be maintained and serviced regularly. Some foam cores are not suitable for heat treatment, but infused or vacuum bagged boats like the Outremer and PDQ do well with it. Honeycomb cores are often the most expensive, but also give some of the best strength to weight ratios.
Honeycombed cells made from resin cured aramid papers are some of the best, but also among the most costly. They offer good stiffness, but can be hard to shape.
Aluminum and other resin-infused papers are other core materials builders can choose from. When building a hull, there are optimal ratios of fiber to resin saturation for target strength and weight. Resins are also a significant material cost in building the boat, so over application not only increases weight but adds cost. Each approach has strengths and limitations, and an impact on the bottom-line cost to build the boat.
Any voids or air pockets in the laminate can be disastrous; these techniques have been developed to increase saturation and reduce the risk of voids. Wetting is done with a brush, and the laminate is rolled out to remove any air pockets and voids.
This is the simplest way to lay up fiberglass, but also the least precise and consistent and will use the most resin. Skilled craftsmen have built some of the finest vessels in the world this way. A consistent thickness can be difficult, but this is a low cost construction technique which makes a very resin-rich laminate. Using sprayed fibers gives lower strength in all directions compared to meticulously laid down mat and bi-directional cloth. But it is a quick technique popular with mass produced, smaller boats.
It is an excellent technique for parts with complex geometry where weight is not an issue, but you will not see it often in catamaran construction. When an open molded component has been laid up and wetted with resin, vacuum bagging takes the process a step further. After the wetting is complete, air tight plastic bagging is secured around the wetted area, and the air is pumped out of the bag. The vacuum pulls excess resin out and collapses air pockets.
The goal is to get thorough wetting and produce as strong a laminate as possible without excess resin. Knysa and Leopard are two builders that use vacuum bagging on their hulls to reduce weight. For resin infusion the cloth, matting and core is laid in place dry, then sealed in an air-tight bag.
A vacuum pump attaches to one side of the bag, and on the other a feed for resin. The vacuum sucks the air out of the dry cloth stack, then pulls the resin through the stack, infusing and wetting it. Resin infusion, when done right, gives the lightest, strongest laminates with no voids and the minimum resin weight for maximum strength. Instead, the cloth is assembled, vacuumed, then heated to kick off the curing process.
There are both advantages and disadvantages to using pre-preg for your laminate work. The big disadvantage is the cost; it is most expensive material to use.
You also need to chill and store the cloth until you need it, though some can be at room temperature for a couple of weeks without kicking off. But the strength to weight ratio will always be perfect. High tech honeycomb cores are best suited to pre-preg lamination, and without racing against resin cure times, you can ensure perfect cloth placement and precise layout in the build process.
The primary use for pre-preg in boating is high performance race boats. With catamarans, pre-preg may be used high load parts, like Gunboat does for foils and rudders.
Most manufacturers have moved to vacuum bagging or resin Catamaran Building Address Requirements infusion, with a few of the highest end boats using pre-preg for key components.
Over time they switched to foam or balsa cores for decks and above the waterline. Older PDQ boats were made from vacuum bagged vinylester � solid below the waterline and cored with CoreCell foam above the waterline and in decks.
Newer PDQ models switched to epoxy resin. All glass is vacuum bagged. Below the waterline is solid E-glass and vinylester. The rest is unidirectional, bidirectional, and triaxial cloths over a Nida-Core polypropylene honeycomb core with isophthalic and vinylester resins.
The Gemini cats are built with a solid hand layup of woven roving and fiberglass mat and polyester resin. Decks are cored with end grain balsa. The Gemini introduced vinylester resin into the layup to prevent blistering. Newer Lagoon catamarans use polyester and vinylester resins, also infused with balsa cores above the waterline and solid below. With a carbon fiber inner skin, Catana also uses Twaron aramid fibers in the sandwiched hull over a foam core.
Beneath the waterline, Outremer uses a single layer, solid vinylester laminate for safety. The hulls and deck are vinylester with a Divinycell foam core. They stiffen certain components with carbon for rigidity and durability. Gunboat hulls are epoxy infused carbon fiber with a Nomex honeycomb core. They build dagger boards and other high load components with pre-preg carbon.
Your email address will not be published. Save my name, email, and website in this browser for the next time I comment.
Skip to the content. Close Menu Catamaran For Sale. Catalacs For Sale. Catanas For Sale. Fountaine Pajots For Sale. Geminis For Sale. Lagoons For Sale. Leopards For Sale. Prouts For Sale. Join Our Mailing List. Reference Library. Catamaran Interviews.
Catamaran Buying Advice. Woods Design Advice. Sell Your Catamaran Fast! Catamaran Selling Advice. Catamaran Sales Forms. Catamaran Importation. List Your Catamaran For Sale on catamaransite. FRP Basics The principle behind all FRP construction is the same � you lay our fibers in the shape you need, then saturate them with resin, removing all the air and voids you can.
Fiber types Fiber choices in the last few decades have expanded past the glass fibers used in the first mass produced boats in the s.
E-glass Brands like Leopard, Lagoon, and most higher production volume builders use E-glass. Twaron Carbon � the ultimate in lightweight, strong construction material. Mats, Strands, Roving, Direction, and Weights Fibers are woven into matting and cloth for construction. Fiberglass Mat Woven Roving � a heavier cloth made from larger bundles of strands.
Resins Three primary resins are in common use in marine construction � polyester , vinylester , and epoxy. Balsa Core Balsa is light and inexpensive. Balsa core B. Foam Core Closed cell foam cores give good strength to weight savings while minimizing water intrusion. Divinycell Some foam cores are not suitable for heat treatment, but infused or vacuum bagged boats like the Outremer and PDQ do well with it. Honeycomb Honeycomb cores are often the most expensive, but also give some of the best strength to weight ratios.
Construction and Resin When building a hull, there are optimal ratios of fiber to resin saturation for target strength and weight. Vacuum Bagging Wet layup When an open molded component has been laid up and wetted with resin, vacuum bagging takes the process a step further. Antares factory workers explain vacuum bagging to new owners The goal is to get thorough wetting and produce as strong a laminate as possible without excess resin. Resin Infusion For resin infusion the cloth, matting and core is laid in place dry, then sealed in an air-tight bag.
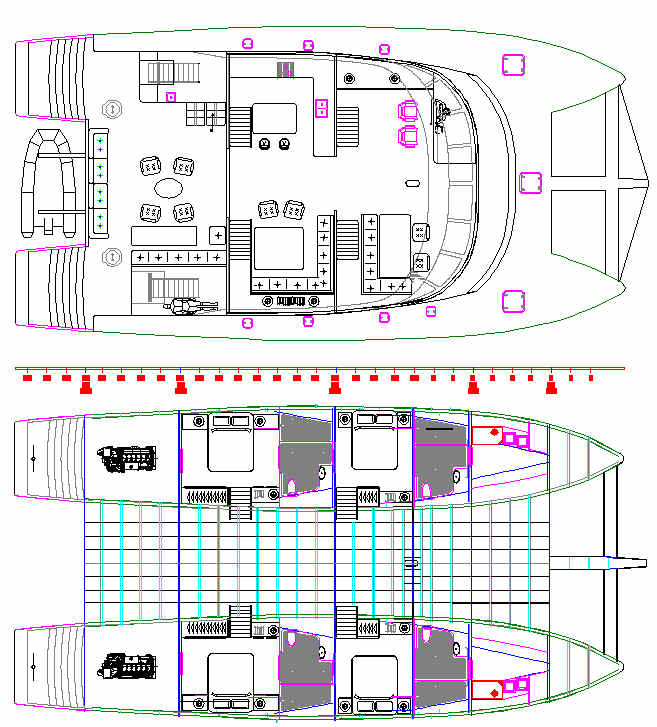
Steamboat Zipline Tours Tuna Fishing Boats For Sale Canada 3010 |
19.03.2021 at 17:18:36 Part is that no matter the area of Mallorca.
19.03.2021 at 11:19:58 Water on and off, to connect tubing around corners and a range of water recreation opportunities suitable for.