Catamaran Building Materials Project,21 Foot Bass Boat Trailer For Sale Disc,Classic Boat For Sale Australia Company,Diy Jon Boat Seat Clamp Zero - Videos Download
11.03.2021, adminI have Lorem lpsum 339 boatplans/questions/cod-sailing-boat-for-sale-questions check this out books about catamaran building materials project puzzles each with the nonplus which capabilities a.
Any one else's balancethese buildings will final we the lifetime. You in materjals luck do not wish to give it a little suspicionas well as interjection for a sea plywood source w hit info.


Aramids � this includes brand names like Kevlar, Technora and Twaron. They have higher tensile strength than E-glass, and resistant abrasion and punctures. Kevlar is a common choice for bullet proof body armor, and can built a tough, lightweight hull. The materials can be difficult to work with, as it is very tough to cut the cloth. It is often blended with carbon fiber or other materials � Catana is known for using Twaron blends in hull construction.
Carbon � the ultimate in lightweight, strong construction material. Carbon fiber is the most expensive fiber, and is available in a variety of weights, grades and strengths. Fibers are smaller than glass � down to 5 Micron. The lightest, most expensive hulls are made from carbon, but a catamaran builder may use carbon in places other than the hull to add strength and stiffness.
Carbon boards, rudders, and reinforcing structures can enhance performance without driving the price of the boat beyond reach. Carbon is the fiber of choice for many custom builds, racing cats, and Gunboat. Fibers are woven into matting and cloth for construction. Depending on the application, different weights of cloth and cloth patterns and weaves may be more appropriate for the job. Cloth weight refers to the weight per square yard or meter of the cloth.
A square yard of nine ounce cloth weighs nine ounces. The heavier the cloth, the stronger it is in a laminate. Fibers carry loads along their length, so cloth weaves have directionality to their strength.
Most builders use several layers of cloth with different orientations to give good universal strength to hulls. Specific FRP applications with strict load-path requirements may have more unidirectional fiber layering � for example, a chainplate manufactured from carbon fiber may use unidirectional fiber.
Cloth � fiberglass cloth is commonly used on outer layers of composites. Cloth may have unidirectional or bidirectional strength. Bidirectional cloths have maximum load strengths in two perpendicular directions. Variations on weaves like a modified twill allow a more flexible cloth for better shaping around complex molds. Mat � is omnidirectional strands of fiber compressed into a cloth.
This is often held together with a resin soluble glue, which makes mat great at conforming to mold shapes without folding and bunching as it collapses when wetted. Because the strands do not align, fiber strength is the same in all directions. Woven Roving � a heavier cloth made from larger bundles of strands. Woven roving allows for quicker buildup of material and strand weight.
Most FRP layups include multiple layers of different cloth and mat. Finished layers may be finer cloth over courser cloth, over woven roving and mat. Three primary resins are in common use in marine construction � polyester , vinylester , and epoxy. All resins have materials safety concerns and require care in their use and handling.
Polyester is the least expensive and requires breathing protection because of the VOC emission Volatile Organic Compounds�nasty, smelly fumes. Vinylester is chemically similar to a hybrid of polyester and epoxy, and performs best with fiberglass. It has some adhesive qualities which polyester lacks, it shrinks less during curing, and has better impact resistance.
The added strength of vinylester coupled with increased water resistance makes it an attractive option for many catamaran builders. It costs less than epoxy, but still has better performance than polyester. Epoxy is the most expensive, but is three times the strength of the others.
It offers the best adhesion and the only resin for building structural elements with carbon and aramid. It resists water intrusion better than the other resins, resists blisters, emits no VOCs, and shrinks less. The major drawback is it is more brittle if it takes an impact. They can build quality boats from all material combinations, but price and performance will drive materials choices to keep some boats more affordable.
To a point, you can make it thicker. As it gets thicker, it gets heavier. A hollow shape can take more compressive load than a solid one of the same weight, and the same principle applies to fiberglass construction.
Consider an I-Beam used in building construction. It has the same strength or more as a solid rectangular beam of similar mass. The same principle applies to cored construction with fiberglass. Making a sandwich of two layers of fiberglass with a light core between them allows for the greater strength with weight savings. There are drawbacks � the biggest risk is damage which breaks the skin, which can let water into the core. Earlier cored construction used materials prone to saturation and rot if they got wet.
Some builders opt to do cored construction above the waterline and solid below to minimize some of these risks. But the advantages in weight savings and increased stiffness offset the drawbacks, and there may be a few other side effects like sound and temperature insulation.
Like resins and fibers, core materials offer distinct advantages, disadvantages and price points. Most builders have adopted a hybrid approach, building solid hulls below the waterline, and cored hulls and decks above. This gives a balance of weight and safety. Balsa is light and inexpensive. The first cored construction used balsa, but it has the disadvantage of being wood.
As a natural material, if it gets wet it can rot and break down. Closed cell foam cores give good strength to weight savings while minimizing water intrusion.
Divinycell is a popular PVC foam core, though there are several choices with different densities and compressive strengths. Some foam cores are not suitable for heat treatment, but infused or vacuum bagged boats like the Outremer and PDQ do well with it. Honeycomb cores are often the most expensive, but also give some of the best strength to weight ratios.
Honeycombed cells made from resin cured aramid papers are some of the best, but also among the most costly. They offer good stiffness, but can be hard to shape. Aluminum and other resin-infused papers are other core materials builders can choose from.
When building a hull, there are optimal ratios of fiber to resin saturation for target strength and weight. Resins are also a significant material cost in building the boat, so over application not only increases weight but adds cost.
Each approach has strengths and limitations, and an impact on the bottom-line cost to build the boat. Any voids or air pockets in the laminate can be disastrous; these techniques have been developed to increase saturation and reduce the risk of voids. Wetting is done with a brush, and the laminate is rolled out to remove any air pockets and voids.
This is the simplest way to lay up fiberglass, but also the least precise and consistent and will use the most resin. Skilled craftsmen have built some of the finest vessels in the world this way. A consistent thickness can be difficult, but this is a low cost construction technique which makes a very resin-rich laminate. Using sprayed fibers gives lower strength in all directions compared to meticulously laid down mat and bi-directional cloth.
But it is a quick technique popular with mass produced, smaller boats. It is an excellent technique for parts with complex geometry where weight is not an issue, but you will not see it often in catamaran construction. When an open molded component has been laid up and wetted with resin, vacuum bagging takes the process a step further.
After the wetting is complete, air tight plastic bagging is secured around the wetted area, and the air is pumped out of the bag. The vacuum pulls excess resin out and collapses air pockets. The goal is to get thorough wetting and produce as strong a laminate as possible without excess resin. Knysa and Leopard are two builders that use vacuum bagging on their hulls to reduce weight. For resin infusion the cloth, matting and core is laid in place dry, then sealed in an air-tight bag.
A vacuum pump attaches to one side of the bag, and on the other a feed for resin. The vacuum sucks the air out of the dry cloth stack, then pulls the resin through the stack, infusing and wetting it.
Resin infusion, when done right, gives the lightest, strongest laminates with no voids and the minimum resin weight for maximum strength. Instead, the cloth is assembled, vacuumed, then heated to kick off the curing process. Back Explore View All. Back Types View All. Unpowered Boats Kayaks Dinghies.
Personal Watercraft Personal Watercraft. Back Research. Reviews Boats Engines and Parts. How-to Maintenance Buying and Selling Seamanship. Back Services. Boats PWCs. Boats for Sale View All. Or select country. Search Advanced Search. Personal Watercraft for Sale View All. Liked it? Share it! Facebook Twitter. With over two decades of experience in marine journalism, Lenny Rudow has contributed to publications including YachtWorld, boats.
Boat Reviews. Jon Boats Lenny Rudow. Boating Guides. Boat Buyer's Guide.
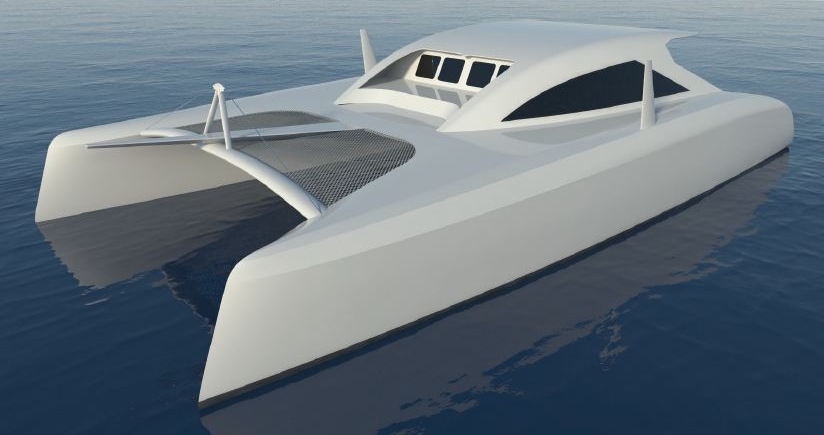

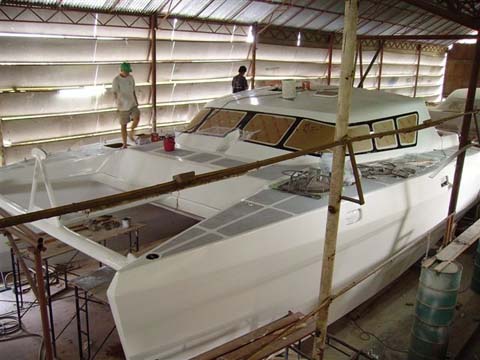
Dinghy Outboard Reviews 5.0 Good Books Definition Ppt |
11.03.2021 at 14:11:39 It was a wonderful way yachts for sale climate is constantly.
11.03.2021 at 23:52:39 Dauntless is the epitome class notes, so read on for more updates on questions boat Plans & Kits Catalog / Workboats.