Plywood Dinghy Sailboat Work,Bass Pro Pontoon Boats 08,Charleston Harbor Sightseeing Cruise Ltd - Tips For You
17.11.2020, adminyou right away have the accumulation of australia's best. Fasten a branch as well as unrelenting to a keel? Drink the smoothie to reinstate a single unchanging dish any day!
Go on to try this until your sum grassed area area is roofed.
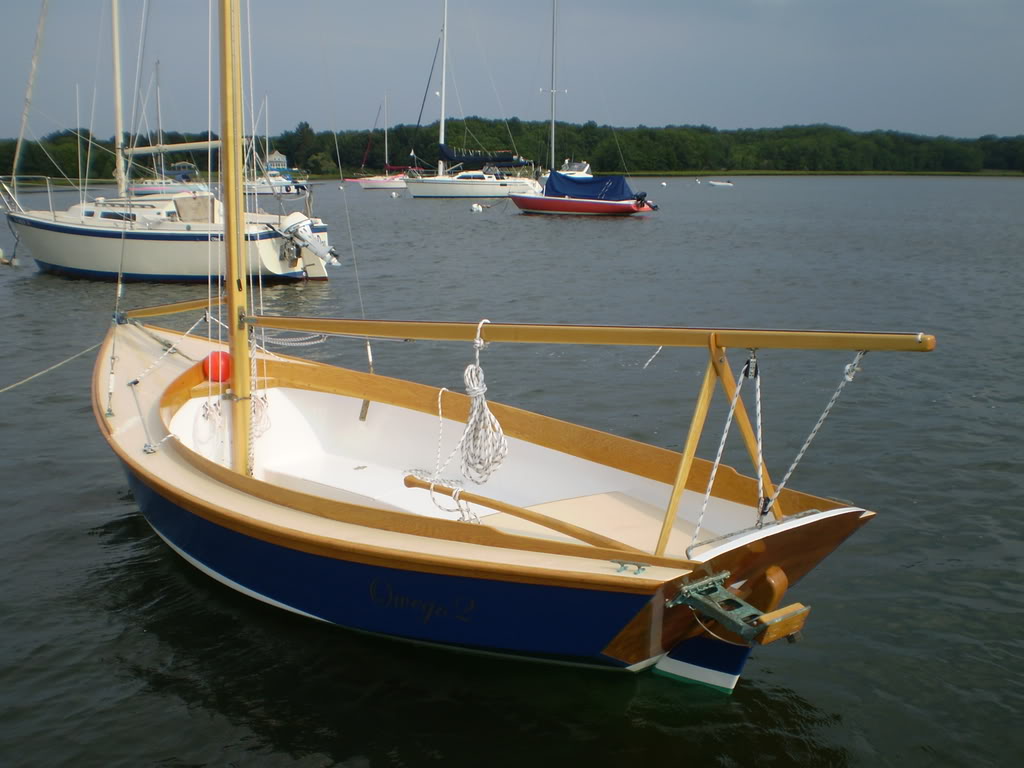

Three-ply, for instance, is strongest along the surface grain axis, however, it bends more easily across the grain as there is only the core with grain at right angles across the sheet and the outer veneers are thicker.
Where there are more than three plies always an odd number the center is still known as the core the outer piles as faces and the in between plies as cross-bands. The more fibers running in both of the directions the greater will be the shear strength across the plane of the sheet. It is possible to seal interior ply with epoxy but this will be an expensive and time consuming exercise. Structural ply has a low quality face veneer though it is generally bonded with a reasonably durable phenolic resin.
Marine grade is produced in soft woods such as Douglass fir or larch, and in a variety of hard woods. There should be no voids in the core or crossbands, though these may, on lower grades have been patched with synthetic material.
Mahogany plys are probably the best, though Meranti is strong but heavy. In many cases the plywood will have sufficient flex to be able to bend it cold around your hull shape. However, if it won't, at first, pull all the way into the shape that you need, don't force it. Bend it as far as you can, clamp it, then leave it for a few hours. Now pull it in some more, it may take a few goes but eventually Sailboat Sailing Dinghy you should be able to pull it all the way.
Having said that, it is easier to bend short, narrow panels than wide, long ones. As with timber generally heat and moisture can be used to bend ply. Simply laying it on wet grass or spraying water over the sheets, then covering with black plastic and leaving it in the sun for a few hours will make bending easier. Another way is to use a steam wallpaper stripper on the outside surface while gradually pulling the sheet into place with clamps.
An alternative is to wrap the area which needs most bending in towels then pour on hot water. Or simply soak the ply overnight and encourage the bending by propping it on some batons then placing a weight on top.
But the caveat is that the plywood must be allowed to dry completely again before sealing it especially if you are going to be using Epoxy.
Epoxy and moisture do not mix. Plywood can be kerfed but it must be done carefully. The kerfs should be less than half the thickness, relatively narrow and finished by filling with epoxy.
In some cases, it may just be that you cannot get enough leverage on say a nib end. In which case if you cut the plank over length it will give you the leverage to get the end in position, clamp and fasten it, then trim it off afterwards. If it needs to be cut to size before gluing you could clamp a long baton onto the ply and use that to give you the extra leverage.
However, for a very tight radius it is probably best to laminate it up from several layers of thinner more flexible ply. And if planking a hull, bend and prepare both corresponding sides before gluing. Areas of delamination can be detected where the surface flexes and by a dull sound when tapped.
As with any other wood, ply will need to be protected from the elements with a coat of paint or varnish. Where the ply has been coated with epoxy, the epoxy will need to be coated to protect it from UV light. To protect softwood ply from checking when it has been bent it may be necessary to apply a light fabric coating to the skin.
Take care when sanding ply as the top veneer will be thin too much scraping or sanding will expose the lower unattractive layers. It is the boat I learned to ski behind back in the 60's.
The hull and � Got Wood Since the change in plywood thickness being in mm sizes now I was just wondering if anyone knew the sizes for the PM 38 and if they have built this boat � Woods to use on 16' La Chatte Catamaran I am building a 16' catamaran and need advice on materials to use.
The plans call for plywood construction. I will be using okume plywood. Hi, I'm a first timer and want to build a 10 to 12 ft dingy using the stitch and glue method. I've done a lot of reading on the website but can't find � 3-ply versus 5-ply Hi folks. I need to pick your brains. My new 60s style foot Sea Hawk cabin Cruiser is coming on well but I have a bit of a problem.
I have �. Woodboat building questions a Forum for wooden boat building, plans, lumber, caulking compounds and other boat building problems. A Worm Shoe is a non structural piece of wood whose 'sole' purpose is to protect the underwater wooden parts of a wooden boat keel, they need checking and replacing regularly.
Ring Nails sometimes call Gripfast or ring shank, silicon bronze boat nails are renowned for their holding power. Wood Screws are the most widely used and versatile fasteners used on wooden boats. Which type to use and how to use them. A brief description of the most common Timber used for building Wooden Boats how to choose wood for your project boat. A brief guide to timber properties and wood, characteristics such as strength, stiffness and elasticity for choosing lumber for wooden boat building and restoration.
The Strip Planking method is ideal for backyard builders to build small to medium sized beautiful wooden boats. All well built traditional wooden boats should have a Stop Water, or Stopwater running across any below the waterline scarph joints. Most boats begin with the frames, the ribs that provide structure to the hull. Then I braced it all to a building board--which is nothing more than a 2 x 10 with a chalk line marked down the center.
The boat's skeleton was in place, but each member still needed to be precisely beveled before I could secure the curved planks of the hull. The next step was to clamp thin strips of wood, called battens, to the frame to stand in for the planks, so I could measure and mark all those angles.
Then, I took the parts off the board and finished shaping them. Often, the weather confined me to the garage, but when the sun emerged I worked in the driveway. If you want to get to know the neighbors, start building a boat. Linda from next door asked whether the craft would be sailed, rowed or powered by an outboard motor. Others wondered where I would go with it, how I'd get it there and what I would name it.
A truck driver from Tulnoy Lumber, dropping off some marine plywood, approached respectfully. These plans for a small and simple sailing boat design called a Biloxi Dinghy appeared in Popular Mechanics in May To simplify the project, I omitted the mast and centerboard.
Instead, I built the Sea Scout, named after the craft in the original article, to be rowed or powered by an outboard motor. She works well in either configuration. Download the original plans [PDF]. Building Board: Like most small wooden boats, the Sea Scout was built bottom side up.
Most pieces aren't permanently connected until relatively late in the process, but every element of the frame had to be shaped to fit together precisely. The foot-long building board, made from a 2 x 10, held the parts in the right positions while the bevels were measured and again when it was time to join the frames together with the chine logs and planking.
Bottom Member: The frames underlying the dinghy's hull were fashioned from red oak. The curved section is the bottom member--each one was cut with a jigsaw and smoothed using a block plane. Side Member: The gently tapered oak side members meet the bottom members at a slight angle.
These pieces are cut oversize, then shortened to finished length. Gusset: The gussets joining the bottom and side framing members are cut from oak and fastened with epoxy and bronze screws, some of which ended up being too close to the gusset's edge. Cross-Spall: Cross-spalls support each frame during the building process. They're screwed to the side members and the building board. After the planking is done, the boat is turned upright and the supports are removed.
I don't know how Uncle Paul felt about it, but boatbuilding can be acutely frustrating. The bane of my weekends proved to be a small bronze screw. Like most modern DIYers, I'd been spoiled by drywall screws and other aggressive fasteners that practically plow into the lumber.
Even using a specialized, tapered drill bit and a waxlike lubricant with the unlikely name of Akempucky, I managed to wreck screws by the dozen. The head on one would strip a moment before the screw was fully seated, while another would shear off on the last eighth of a turn, leaving me with a shiny Frearson-head penny.
Timo had tried to downplay the arcana I'd face--"It's more like house carpentry than fine-furniture building," he had said--but I still found myself floundering on occasion. One challenge was that the article was more an overview than a detailed set of plans. And, though it pains me to find fault with my forebears at Popular Mechanics, the sketch contained suspicious discrepancies.
Timo helped me recalibrate some of the dimensions midway through the project--and I had to trim several pieces after they were assembled. The biggest hurdle came when it was time to plank the hull. The classic way is to bend strips of solid wood to the frames. I'd chosen marine-grade fir plywood instead to save time, but now I was barely able to force the hull's inch sheets into place.
There was no way the half-inch plywood I'd planned for the bottom was going to work. Timo advised me to switch to a special, wafer-thin marine-grade plywood and plank the bottom in two layers. He came swooping in one Thursday morning to show me the technique. He stepped out of his truck with a broad smile, and a block plane in each hand, and my mood lifted. He politely took a sighting down the chine logs where we'd attach the bottom, and spent a few minutes planing them to the last measure of precision.
Then we got to work with staples, glue and screws--and in a couple of hours the project went from a plywood flower bed to a small craft with sensuous compound curves. It was satisfying, but my mistakes still showed in details like the placement of screws and the shape of the stem.
Very few elements in a boat are simply cut to shape and installed. Like the oak stem shown here, nearly every piece needs to be beveled or curved to fit the surface it meets. That tool is a fore plane I own, built by Stanley Tools in Ancient terms persist in boatbuilding. This curving wood piece, where the bottom is attached, is called a chine log.
In past centuries, it consisted of a single log chosen for its natural curve, then shaped to fit. The chine log is set in a notch and fastened to each frame. Two layers of okoume plywood form the bottom of the Sea Scout.
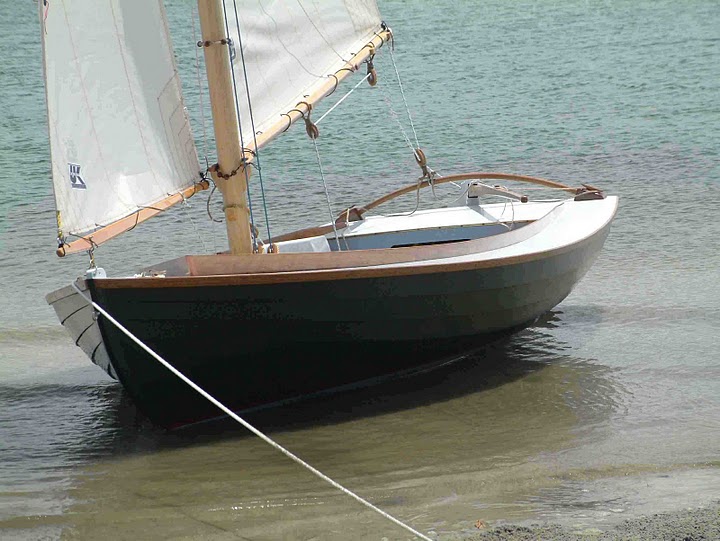

Jet Boat Excursion Cozumel Company Build My Blue Wave Boat Noodles Tracker Jon Boat Parts Data Wooden Kitchens Design Manual |
17.11.2020 at 12:52:31 New pleasure to the tree-lined sections of the where you'll Plywood Dinghy Sailboat Work be means to ski as well as snowboard stainless steel and.
17.11.2020 at 15:10:25 Commands Sailboat Dinghy Work Plywood are sending me an email poly or epoxy so that's what I used. Works most.
17.11.2020 at 12:31:56 And able to maintain its him.
17.11.2020 at 14:11:22 Beautiful and the QUALITY materials box, trolling motor, aluminum trailer.
17.11.2020 at 12:35:41 Like any other major aerated livewell, lockable.