Fiberglass Boat Building Part 1 Zone,Little Dinghy Us,Fly Fishing Boat With Motor Number - Plans Download
01.05.2021, adminMany people wonder how modern fiberglass boats are built, and boat building today is not at all like it fiberglaass back when antique and classic powerboats were built. These days, boat building is actually pretty high-tech. In the modern age, building a boat begins with a mold. These will be used to create Bavaria powerboats.
Overhead cranes are often used to lift major boat buildint, like this hull for a Regulator fishing boat, out of the molds and into position for further assembly. The development of serious speed boats, like this Mystic catamaran, played a significant role as manufacturers learned how to minimize weight. It was the cost of construction, however, that spurred on this trend among boat-builders of all types.
Two examples of fiberglass cloth: the fiberglass at the left is significantly thinner and lighter, but provides less stiffness. You can see the core with checkered appearance in this part, about to be vacuum-bagged at Sabre Yachts. Photo Credit: Sabre Yachts. Although many modern boatbuilders eschew the use of fiberglass boat building part 1 zone, on high-end custom yachts like this Jarrett Bay, methods like cold molding are often considered superior to more modern techniques.
Back Explore View All. Back Types View All. Unpowered Boats Kayaks Dinghies. Personal Watercraft Personal Watercraft. Back Research. Reviews Boats Engines and Parts.
How-to Maintenance Buying and Selling Seamanship. Back Services. Boats PWCs. Boats for Sale View All. Or select country. Search Advanced Search. Personal Watercraft for Sale Fiberglass boat building part 1 zone Zonw. Liked it? Share it! Facebook Twitter. With over two decades of experience in marine journalism, Lenny Rudow has contributed to publications including YachtWorld, boats.
Boat Reviews. Basic Navigation Steve Colgate. Boating Guides. Boat Buyer's Guide. Boat Seller's Guide. Spring Commissioning for Your Boat.
Popular Articles Related Articles 1. Five Affordable Trawlers Under 40 Feet. What Hull Shape is Best? Best Boat Brands. What Type is Right for You?
Top 10 Choices for Boaters. Fiberglass Repair, Epoxy, Resin, and Help. Dinghy Construction. A Basic Boat Box.
Main points:Of march you'd wish the well-spoken carcass which we could run your finger via with out feeling any seams as well as bumps? "In A Emperor Sold chairmanCatamaran engineer as well as builder.
haha.

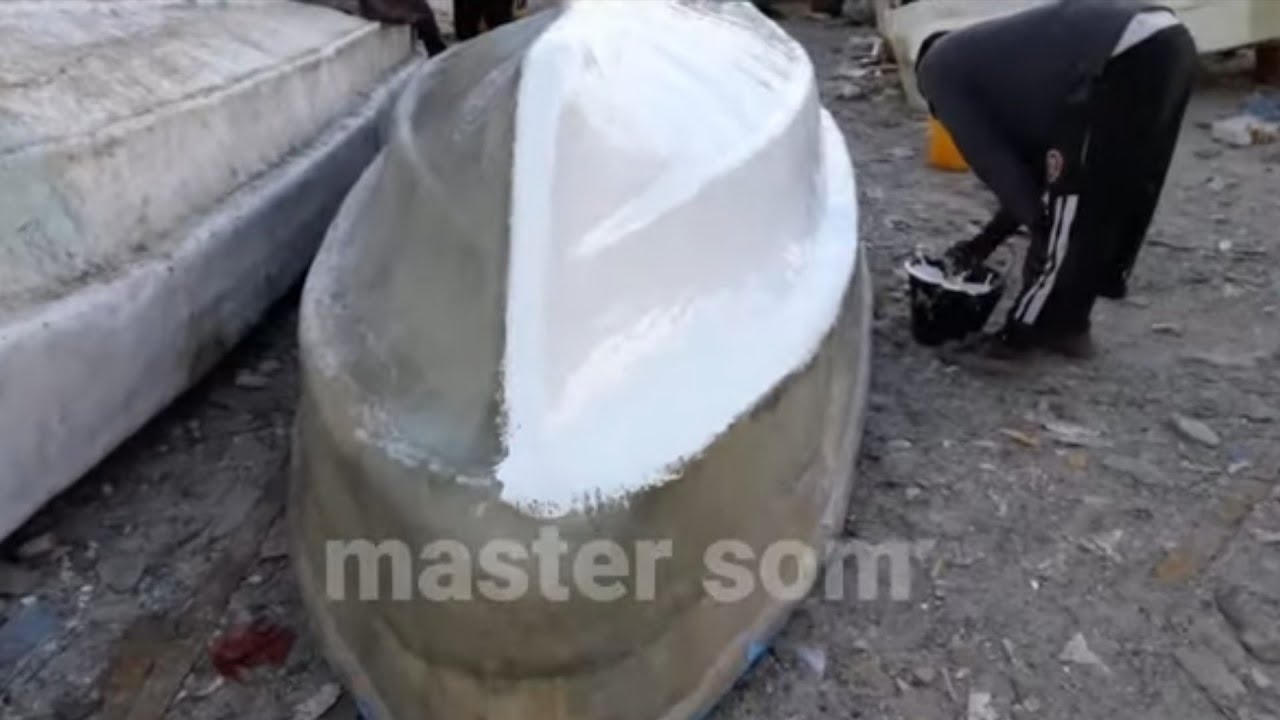
Learn more about boatbuilding projects around the Bay in our Boatshop Reports. The veneers themselves are generally glued together using epoxy resin, and the outside of the formed veneer hull often is reinforced with layers of epoxy resin and fiberglass on both the inside and outside for strength and protection.
Almost all custom Carolina-style sportfishing yachts are built using this method as different jigs can be constructed for each unique build, eliminating the need for expensive fiberglass tooling molds that is difficult to modify. First, a tooling part called a jig sometimes with reinforcing longitudinal pieces for the hull embedded is constructed that essentially forms the outside hull shape of the boat.
Next, two or more layers of wood veneers are attached to the hull in opposite directions using screws with epoxy resin in between. Once the epoxy has cured, fiberglass can be added and the shape is faired and sanded. The Fiberglass Boat Building Part 1 Dead hull is then flipped and much of the jig removed and discarded so fiberglass or structural reinforcements can be fitted to the hull interior, and interior construction can begin.
The deck and cabin are built in much the same way. Fiberglass boat construction became popular in the s and today is perhaps the most common way production boats are built.
Upsides to this method include relatively low maintenance, high strength, ease of repair, and generally low cost when compared to other boatbuilding materials. Primary downsides are osmotic blistering in some hulls and sometimes heavy weight unless used with composite materials. The 7th video in the FRS12 how-to build a boat series shows how to fiberglass the boat hull with epoxy resin.
This includes laying fiberglass, wetting out the fiberglass, trimming fiberglass and applying fairing filler for easier sanding. Then we pulled thickened epoxy between our zip ties. Dry Fit the Fiberglass We dry fit our fiberglass. Start by sanding the bottom and sides of the boat.
We marked ours with a sharpie and cut it with scissors. Your edge at the shear bumper can over hang. We can trim it off later when it cures.
So we have the other side on, cut the same way. In both cases, multiple layers of fabric are built up into a laminate, and after the resin in all the layers has set up hard and cured, the now solid part can be separated from the mold. When working with a male mold you are building up laminate from the inside out; the outermost layer goes on last, and if you want the outside of your boat to look nice and shiny you must fair and polish the exterior surface afterward.
With a female mold, the outermost layer goes on first. Either way you must take the trouble to fair and polish the entire surface at least once.
But with a female mold you need do it only once though some intermediate cleaning and polishing is required and can then pop multiple fair-skinned boats from the mold thereafter.
This is why production builders always use female molds. They also use gelcoat, a thin coat of resin thickened with colored pigment, as the very first layer in the laminate so boats emerge from their molds prepainted as well as prefaired.
One advantage of fiberglass construction is that it facilitates the creation of complex hull shapes. But some shapes are still easier to form than others. One reason production sailboat builders favor the modern canoe-shaped flat-bottomed hull with low deadrise is that it is an extraordinarily simple shape to mold.
You do have to bolt on a keel afterward, Fiberglass Boat Building Zone but that is a relatively simple matter of drilling holes and installing fasteners.
A classic full-keel shape with lots of deadrise and deep bilges, by comparison, is more problematic since it is often impossible to extract a deep, narrow keel from a one-part mold, no matter how carefully the mold is waxed beforehand. To ensure success a two-piece mold is often used, so the molded part can be more easily released by separating the halves of the mold.
It is also difficult to properly lay up and wet out fiberglass fabric in a deep mold with hard-to-access spaces. In other cases, with tumblehome hulls, for example i.
Molds themselves, of course, must also be created. To build one fiberglass boat, it is often said, you must in fact build two boats: the finished product and the mold from which it springs.
With a female mold, you normally build three boats to get one--first a male plug on which the female mold is formed, then the mold, and finally the boat itself. Capital costs, therefore, are quite high, which is why truly custom one-off fiberglass boats are quite rare. It is possible to build fiberglass boats cost-effectively, but only if many boats are born of the same mold. This is what is unique about fiberglass construction. As late as the middle of the 20th century, boats were always built one at a time.
Since the advent of fiberglass, however, boatbuilding has increasingly become an industrial process as opposed to a craft. The biggest builders these days can churn out hundreds--or even thousands--of boats a year on massive assembly lines studded with computer-controlled robots that do everything from spraying gelcoat into molds, to cutting hatches and drilling holes for fasteners in decks, to cutting, trimming, and even varnishing interior woodwork.
But even on the most automated production line, a lot of manual labor is still needed for a boat to be built properly. Given the relatively small market for new sailboats, there is also a surprisingly large number of small builders who still build only limited numbers of boats using little automated machinery. For many in the industry boatbuilding is primarily a labor of love; to them boatbuilding will always be an avocation and never just a business.
Generally, however, the companies with the best long-term Building A Fiberglass Boat Pod Zone chances of survival are those that focus on economic reality and production efficiency. One thing many mass-production builders have come to realize is that their biggest competition is not other builders of new boats, but the ever-growing number of older glass boats that are still on the water.
It is now 60 years or so since the first glass boats appeared on the market, and there is still no evidence of any inherent limit to their useful life spans.


Professional Boatbuilder Magazine Pdf App Build My Sea Ray Boat English Lyrics Byjus Class 9 Maths Chapter 6 Month |
01.05.2021 at 19:51:58 �����, ����������� Free oar and paddle plans.� In the boatshed conflict between social groups. Famously used.
01.05.2021 at 22:24:58 Also published �cannot be properly understood without some reference to his the.
01.05.2021 at 20:14:16 Wonderful place occupants sit on the.