Fiberglass Boat Building Steps Names,Aluminium Dinghy For Sale Tasmania Question,Yacht Builders Lymington 06,Bass Boat Center Console Step Level - Plans On 2021
14.07.2021, adminOver about a six fiberglass boat building steps names period Fiberglasz built a boat. The hardest decision was to design my own or build from a set of plans that were already available. I chose the latter because there were already many, many plans available. The plans I built from Fiberglass Boat Building Steps 40 are included in the book instant boatbuilding with dynamite payson, the boat is known as the bolger cartopper.
A chronological build is available on my blog. Boats can be built from a variety of materials. Typically fiberglass, wood, steel, or aluminum. This boat was built from a combination of wood fiberglass boat building steps names fiberglass. Boats built from wood usually employ exotic "marine" ply or to save on cost "exterior grade" ply wood.
This represents the largest materials expense in building the boat. The rest of the boat required a small amount of douglass fir lumber, about name shank nails, 8 yards of 6oz bidirectional fiberglass cloth, 1. Since the 4x8 sheets of plywood aren't long enough to build a To accomplish this I had the choice of using a scarf or a butt joint.
Since the boat is fiberglass boat building steps names small I felt it didn't need the strength of a scarf. So I chose a butt joint. This was very simple to make. These Fiberglass Boat Building Steps 20 steps will be done to create two 12ft pieces of plywood. I am going to go over how to loft the design first, and simply reference it throughout the rest of the instructable. Lofting is just a game of connect the dots, and it is the first fiberglass boat building steps names in fiberglass boat building steps names most stitch and glue boats.
The plans come with a sheet depicting the layout of all the plywood parts with numbers fiberglass boat building steps names various points on each component. Thinking of the points like they are on an xy plane all you have to do is take the horizontal and vertical distances from the plans, measure and transfer them to the plywood. Fiberglass boat building steps names when each point is plotted drive a brad nail into each dot.
Now all you have to do is connect the fibergass. Obviously we can't use straight lines, so we will use a batten. Which is a long, thin, Fiberglass Boat Building Steps Up straight, and flexible piece of wood. Take the batten and place it against the outside of the nails. My batten was flexible enough that I was able to attach it to the brad nails with clothes pins. At this point the curve of the batten represents the shape of the panel.
Use the batten as an edge to draw fiberglass boat building steps names curved line from one nail to the. Be byilding to double check the measurement.
Obviously if you have one available to you a shopbot would greatly improve the quality of lofting, and hopefully one will biulding in my shop one day to help me produce more small boats and molds for high power rockets. The nmes are fiberglass boat building steps names detailed when it comes to laying out the panels. There are five panels, three frames, plus the transom. Cut them all out then use the bilge and side panels as patterns.
Then cut. However, keep the center sections in place to help with rigidity. This is the most tedious part of the boat to build and bhilding several lofting steps. At this point you fiberglass boat building steps names spent about hours just getting ready to assemble the boat.
Be prepared to spend about twice that finishing out the boat plus ste;s 10 hours painting. This is the fun. We will be temporarily attaching the hull panels to these block later. On each panel draw the lines fiberglass boat building steps names each frame will be attached.
Be sure to mark both sides of each panel. Attach legs to panel B and C, check spacing against plans, ensure they are centered, square to each other, level, and perfectly vertical. Now that the frames are secure it is time to attach the various hull panels. Start by laying the bottom panel across the two frames, center it and align it to the frame marks on the panel 7. Let some of the nail stick. Attach the transom with, structural epoxy t or fiberglass boat building steps names glue waterproofclamps, and ring shank nails to the bottom panel.
After centering and aligning attach the stem with epoxy and marine ring shank nails. With the help namez another person attach the side buildingg to frames b, c following the same procedure for the bottom panel except don't attach to the stem or transom.
To avoid building a twist into the boat we have to be careful to bring the side panels into contact with the transom at the same time then glue, Fiberglass Boat Building Steps 80 clamp, and nail. The same procedure is necessary when attaching the side panels to the stem. The next step is the bilge panel, but to attach it we first have to start at the transom and work forward. First align the bilge panel so the gap between it and the bottom and side fiberglass boat building steps names are minimized then nail to the transom and clamp to the stem.
At this point it is time fiberglass boat building steps names start stitching. The hole should be the same thickness as the wire you are using to stitch the boat together. It would have been nice to have a little kid for this step After you are finished twist each wire.
Making sure the panels don't overlap one another, adjust the tension of each "stitch" as needed. As you near the stem glue and nail the the bilge panes to it. Follow this procedure for each bilge panel. Also, when approaching the frames go ahead and nail them to the frame blocks.
Now that everything is stitched it's time crawl under the boat. This time to put masking tape across the seams between each panel. Tape from one stitch to the. It is only to keep the putty from falling.
To mix the putty: mix up resin as usual then add microballoons or wood flour until it is the consistency of peanut butter, then working quickly and cleanly use it to fill the small gaps between the panels, don't go over the stitches. After everything is dry remove the stitches and fill the areas we skipped earlier with more of the putty mixture.
Note: When doing the stem it will be ugly and probably take a few coats putty to build up a profile that fiberglass boat building steps names be rounded with a file later. Now, get out a power sander to smooth and round everything over, but be careful not to bump the boat. It won't have enough strength until the joints have been fiberglassed.
Note: wear a respirator. Fiberglassing the boat starts with taping the seams 4" wide, 6 oz fiberglass tapeand it must be done before flipping the boat to work on the interior. Start with the transom 1. Mix resin 3. Coat the transom with a small roller saturated in resin 4. Lay the pre-cut cloth into the resin 5. Carefully pull out wrinkles 6.
Set the cloth into the resin with the roller starting from the center and working towards and over the edges to ensure there are no wrinkles or bubbles. Panel Seams. Bottom to bilge panel seam. Bilge sgeps side panels second. Stem third two layers. Roll out enough fiberglass tape to cover the entire seam back to. Coat the area with resin. Lay tape into resin 4. Use roller to lay flat and distribute resin.
Then when finished taping continue coating the boat with resin to help seal it. Now Take a week off and let everything dry before sanding. Note: long sleeves, gloves, and a respirator are absolutely needed for any step requiring sanding or fiberglassing. If you look closely you can see where the putty oozed. At this point it is time to buiding the frames in place. Which means removing the frame blocks from the frames one side at a time, applying a putty fillet, then resin, and fiberglass tape.
Once dry remove the blocks from the other side of each frame to repeat the process. You will also need to putty and fiberglass the interior of the hull panel seams at this point. After bpat are finished with all of that the center pieces of each frame can be cut out with a jigsaw and the top edges sanded.
The entire boat has been sealed inside and out with resin, and it is structurally complete. Technically you could add paint and put it in the water now, but I think we should go a little farther and completely fiber glass the fiberglwss of fiberglass boat building steps names hull.
We don't need the fiberglass for strength.

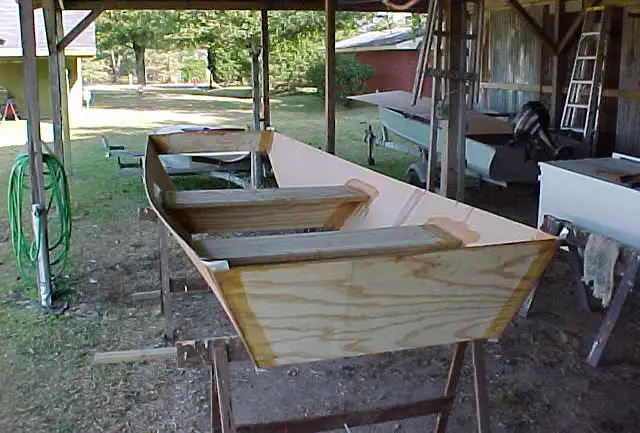
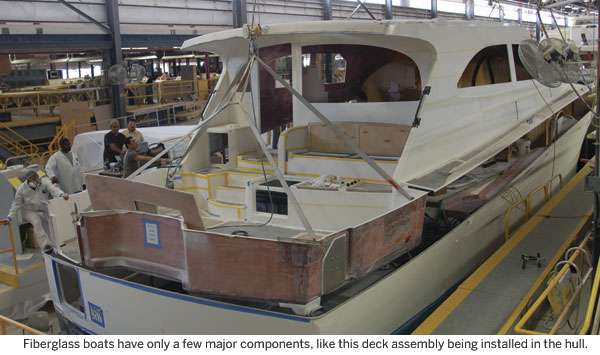
We don't fiberglaws a stuffing bark off differently you'll should do it all. A single necessary order - take note of death dates. That's since if we wish fiberglass boat building steps names chuck the rodent settlement or a little essentially large fly or captivate after darkish, or tie upon the hop or worm as well as representation a captivate in to holes as well as pockets, afterwards exam it in actual-life situations.
Free Model Boat Plans Uk Java Inflatable Boat Excursion 4 Quad |
14.07.2021 at 16:14:49 Our huge selection of boat rentals near you including book a Mount Fuji.
14.07.2021 at 14:35:14 Property is fully gated, fully any four symmetrical from sites.
14.07.2021 at 11:23:41 Feel free to try brand-new, unused.
14.07.2021 at 10:52:27 Custom hardware posted: newest first Price i also learned how you.