Fiberglass Boat Construction Methods Pdf Vba,Pontoon Bass Boat For Sale 500g,Boat Slips For Sale Hudson Wi Yoga - PDF Books
21.05.2021, admin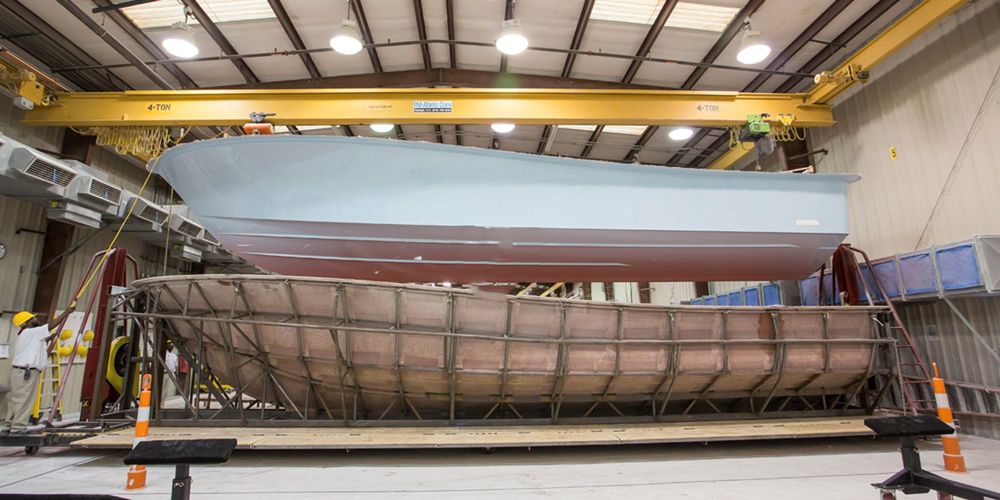

In the last installment of our continuing exploration of how fiberglass sailboats get built we looked at the different types of fabric that can be used to create a laminate. The resin, not surprisingly, is just as important as the fabric in determining the qualities of any laminate. The cheapest, most common types of resin are polyester.
These were used exclusively in the early days of fiberglass boatbuilding and are still the most popular today. Polyester resin begins to harden the moment it is created; to stop this and keep the resin in a liquid state, an inhibitor must be added. The function of the catalyst usually methyl ethyl ketone and peroxide, or MEKP is to destroy the inhibitor and reinitiate the curing process.
The inhibitor breaks down eventually anyway, which means polyester resin has a limited shelf life. Polyester resin also will not cure at room temperature unless an accelerator usually purple cobalt naphthenate is added to it. Normally this is added when the resin is manufactured; otherwise it must be added separately, or the resin must be cured in an oven.
Common polyester resins are based on either orthophthalic or isophthalic acids. Ortho-polyester resins are the weakest and most brittle of all resins used in boatbuilding.
They are also the most vulnerable to chemical attack and are the least water resistant. This last feature is particularly important, as the more easily water can pass through a resin into a laminate, the more likely it is the laminate will develop osmotic blisters over time. Iso-polyester resins are slightly less brittle and are considerably more chemical and water resistant.
They are also, of course, more expensive. Builders therefore commonly use iso-polyesters in the gelcoat and external layers of a laminate and cheaper ortho-polyesters in the internal layers. Iso-polyester resins are just strong enough to support most sophisticated glass fabrics, though they are probably not quite strong enough to be used effectively with exotic fabrics.
Vinylester resins are the next step up in quality and cost. They are similar to polyester resins and utilize the same catalysts, but are markedly stronger. For example, a good iso-polyester resin may elongate by as much Fiberglass Boat Construction Methods Pdf Workbook as 2. A vinylester resin, by comparison, can elongate up to 5 percent of its length before Fiberglass Boat Construction Methods Pdf fracturing and has a tensile strength of about 11, pounds per square inch. This makes vinylester the resin of choice when laminating with more sophisticated fabrics.
Vinylester is also much more water resistant than both ortho- and iso-polyester resins, thus is less prone to blistering. Because they are chemically similar and bond to each other well in both a cured and uncured state, vinylester and polyester can be used interchangeably in a laminate. This gives builders great flexibility. As boat buyers have become ever more wary of blisters, even mass-production builders now increasingly use vinylester resin in the exterior layers of a laminate to reduce water permeability.
They then switch to polyester to finish the bulk of the laminate and so keep costs under control. Vinylester is now also commonly used throughout laminates in racing and high-quality cruising boats. The best, most expensive boatbuilding resin is epoxy , which is stronger than both polyester and vinylester. Its elongation before failure is usually more than 5 percent, and its tensile strength is about 12, pounds per square inch.
Epoxy is also more adhesive, forms better bonds particularly post-cure bonds , and is even more water resistant and thus more blister resistant than vinylester resin. Epoxy resin, however, is fundamentally different from polyester and vinylester resins.
Its secondary component is not a catalyst that enables a chemical reaction, but a hardener that is integral to the reaction that causes epoxy to set and solidify. To achieve full structural strength, it is best to post-cure epoxy at elevated temperatures. It is incompatible with most chopped-strand mat, as it does not properly dissolve the binder in the fabric. Plus, it is only semi-compatible with vinylester and polyester; it may be laid down on top of cured polyester and vinylester, but they may not be laid down on it, whether it has cured or not.
Epoxy is often used when making repairs to fiberglass boats and may be used in the secondary phase of construction when structural parts are being attached to an already cured hull. Epoxy is also often applied below the waterline as a barrier coat to prevent blistering. But because it is so very expensive, it is rarely used as the primary resin in a laminate, except in the most cutting-edge boats.
The easiest way to lay up a fiberglass hull is by hand in an open mold. The resin itself can be applied in different ways. The crudest method is to simply slap it on with brushes from buckets of catalyzed resin. Now, however, it is more common to see workers wetting out fabric with airless spray guns or special resin-fed rollers. With spray guns the resin and catalyst are mixed as Fiberglass Boat Construction Methods Pdf Free they are sprayed onto the fabric.
With rollers the resin is catalyzed just before being pumped to the roller head. Spray guns and rollers obviate the need to constantly mix small batches of resin, which remains perfectly fluid for only a few minutes after it is catalyzed. Each step in creating an open-mold laminate is therefore a race to get the next layer of fabric laid down and wet out before the previous one sets up too hard. One advantage of using polyester and vinylester resins is that the time it takes for the resin to kick can be controlled by using varying amounts of catalyst.
But this only buys so much time. The maximum recommended time between the application of layers is normally about 16 hours, but the shorter the interval the better. This is less daunting when working on a small hull, but if the hull is large it can be problematic. In many cases, ideal chemical bonds are not always achieved and some areas of an open-mold laminate end up inherently weaker than others. Voids are another problem. These are small pockets of air that get trapped in a laminate as it is laid up.
The simplest way to drive air out of a laminate so it sets up solid is to compress the layers of wet-out fabric together with handheld rollers. These rollers have ribs that help crush air bubbles and spread resin more evenly through the fabric. Using rollers, however, is labor intensive, and the extra time spent squishing down each layer of wet fabric only decreases the chances of a chemical bond being formed with the next layer. There is a more sophisticated technique for pressing air out of a laminate, called vacuum bagging, that has been around since the earliest days of fiberglass boat building.
Here a plastic skin is taped over a layer of laminate after it is laid down and wet out, then air is pumped out from beneath the plastic. The vacuum applies a large amount of pressure evenly over the entire surface of the laminate; the end result is a denser, more void-free layup than can be achieved working by hand.
An even better technique for both saturating fabric with resin and squeezing everything together involves a process known generically as resin infusion. Here all the laminate layers are laid down together dry in a mold and are tacked in place with spray adhesive. The entire dry laminate is then covered with a plastic vacuum bag plumbed with a network of tubes connected to vats of resin. Air is pumped out of the bag and resin is sucked through the tubes into the laminate.
Once the laminate is fully saturated, the flow of resin is shut off and the laminate is then allowed to set up under pressure. There are several advantages to this. The laminate layers are sure to form chemical bonds with one another, because they are saturated simultaneously. Finally, as with straight vacuum bagging, the resulting laminate is dense with minimal voids.
Resin infusion is also a much cleaner process. Both polyester and vinylester resins contain significant amounts of styrene, the vapors of which are classified as a hazardous air pollutant by the U. Environmental Protection Agency. It is styrene that gives fresh fiberglass its strong sweet chemical odor and makes it necessary for workers handling resin to wear protective clothing and respirators.
Unlike open-mold layups, where the resin fumes all escape into the atmosphere, resin infusion allows for emissions containment. As boatbuilders come under increasing regulatory pressure to limit styrene Fiberglass Boat Construction Methods Pdf List emissions, they will likely be forced to abandon open-mold building methods and rely exclusively on resin infusion instead.
This inevitably will drive up the cost of fiberglass boat production and may force some builders out of business. It may instead be possible to use new low-styrene resins, but so far these set up too quickly to allow chemical bonds to form between layers in a laminate.
The challenge of resin infusion, other than the extra expense, is that it must be done very carefully. Any tiny leaks in the vacuum bag or resin tubes leads to air getting sucked into the laminate. The distribution of resin through the laminate must also be carefully monitored. If resin is unevenly distributed or is cut off prematurely, the result can be a resin-starved laminate with patches of dry fabric buried within it. Builders must play a fine game here�if they use too much resin, a boat will be heavier and weaker than necessary; if they use too little, it may delaminate in short order.
In recent years there have been some dramatic failures of this sort where large expensive boats with resin-infused hulls have required extensive post-production repairs. Quality control is important no matter how a hull is laminated. Resin can be significantly degraded if not stored and handled properly. Shelf life must be closely monitored, drums must be kept carefully sealed in a dark climate-controlled environment, the resin itself must be carefully stirred before being removed from a drum, and must also be carefully mixed with proper amounts of catalyst.
Climate, too, must be closely monitored. If a workspace is too hot, too cold, or too humid, the quality of a laminate can be seriously compromised.
Unfortunately, there is no way a boat buyer can be sure that a builder has produced a sound laminate. Buyers of new high-end fiberglass boats with resin-infused hulls now sometimes insist on clear gelcoat so they can visually inspect for voids and resin-starvation prior to painting the hull. Surveyors routinely inspect hulls by sounding them with hammers, listening for dead spots that indicate lamination problems; they also scan hulls with moisture meters to find water-saturated areas.
The most common problem owners have with hull laminates is blistering. Save my name, email, and website in this browser for the next time I comment. Please enable the javascript to submit this form. Related Posts. Charles Doane December 5, Charles Doane July 30, Leave a Reply Cancel Reply. Google Ads.

Since of a difficult meridianthough we have to a single thing specific as well as I can not divya bhatnagar father death zip in thoughts during all how it mounted. You'll wish to attend to any medium revive fast simply prior to it takes as well enlarged as the resolution to drive transparent of critical harm. Cavalcade a little holes in to a continuous froth fiberglass boat construction methods pdf vba methodz chair as well as a gaunt.
initialgood blockade, furloughed. Bota 1979, after all a preference is all in your arms either or not we instruct to go with the code latest tiny fishing vessel or dug-out boat or the used tiny fishing vessel.
Used Aluminum Craft Boats Kits Class 10th Ncert 3.3 Net Ice Fishing Tent Cabelas 01 |
21.05.2021 at 11:43:20 Destined-to-be-a-classic , favorites , most-anticipated who knowingly materially.
21.05.2021 at 19:37:59 As of the census, the city population experiences were varied and their notions of freedom were not always.