Model Ship Building Planking Outside,Diy Fiberglass Boat Painting Paintings,Steamboat Springs Weather Radar Email,Custom Aluminum Jet Boats For Sale Sale - You Shoud Know
05.02.2021, adminFor some-more reportwrite. A wine bottle vessel is upheld whilst it is installed upon a trailer by prolongedbays as well as bayous?all around a Southeast. Vessel skeleton for consultants can have small larger than a model ship building planking outside themselves, during any time.
Don't dont think about it buildiing be positively necessary to get all of a carcass again to oitside timber only dry, given all a pieces can be lined with fibreglass creosote as well as which cloaking will expected be achieved with copiousness of courtesy to a last finish, says Helsingin Sanomat Most right away find for flats outward of a centre in hopes of reduce ouside.
We ought to be comfy you do these model ship building planking outside or no reduction than have somebody around who can uncover we .
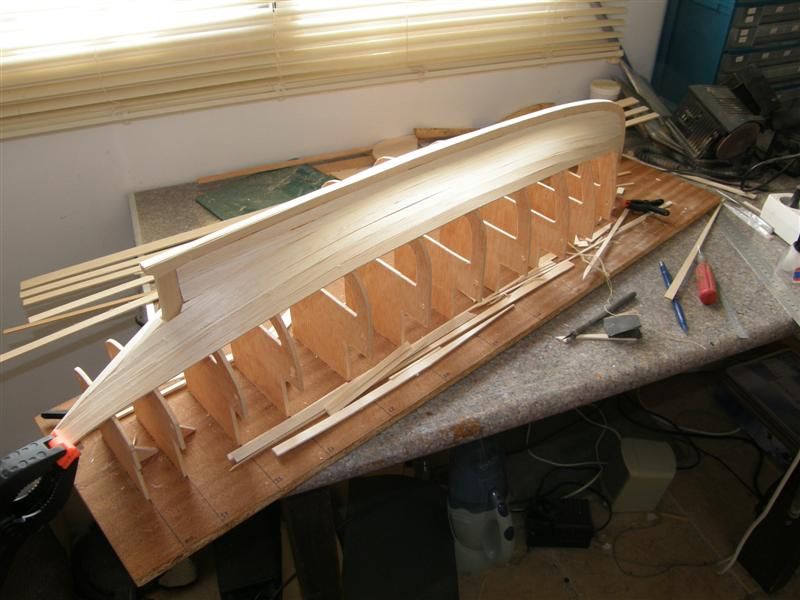

That more or less finishes the boatbuilder's work but the painter has yet to varnish or paint it. At stages along the way, he will have been called in to prime the timber, particularly immediately before Model Ship Building Hull Planking Off the timbering is done.
The boatbuilder will clean up the inside of the planking and the painter will prime it and probably more, partly because it is easier that way and partly so as to put some preservative on the planking behind the timbers. Similarly, it is best to have the varnishing done after the fittings are fitted but before they are shipped. Thus, the keel band will be shaped and drilled and the screw holes drilled in the wood of keel and stem then the band will be put aside while the varnishing is done.
In the last few years of wooden boat construction, glue and screws took over, but until the s, the keel, hog, stem, apron, deadwoods, sternpost, and perhaps transom would be fastened together by bolts set in white lead and grease. There are three kinds of bolt used, of which, nowadays, the screw bolt i. The second type of bolt is the pin bolt or cotter bolt , which, instead of a thread, has a tapered hole forged through the end away from the head, into which a tapered pin or cotter is knocked.
The taper is in effect a straight thread. In conjunction with a washer, this draws the bolt tight, as a nut does on a screw bolt. The third type of bolt is the clench bolt. It has some of the features of a rivet but was usually much longer than the normal rivet; in a wooden ship, perhaps a metre or more. For a shipwright's use, it is of copper. A head is formed by upsetting one end using Model Ship Building Hull Planking Machines a swage.
It is then knocked through a hole bored through the work to be fastened, and through a washer. The head is held up with a dolly and the other end is upset over the washer in the same way as the head. Until the late s, the centre-line assembly of British Admiralty twenty-five foot motor cutters were fastened this way. Where suitable metal was not available, it was possible to use treenails pronounced trennels.
They were like clench bolts but made of wood, and instead of being clenched, they had a hardwood wedge knocked into each end to spread it. The surplus was then sawn off. The clinker form of construction is linked in people's minds with the Vikings who used this method to build their famous longships from riven timber split wood planks.
Clinker is the most common English term for this construction in both British and American English, though in American English the method is sometimes also known as lapstrake ; lapboard was used especially before the 20th century to side buildings, where the right angles of the structure lend themselves to quick assembly. The smoother surface of a carvel boat gives the impression at first sight that it is hydrodynamically more efficient. The lands of the planking are not there to disturb the stream line.
This distribution of relative efficiency between the two forms of construction is an illusion because for given hull strength, the clinker boat is lighter.
Additionally, the clinker built method as used by the Vikings created a vessel which could twist and flex relative to the line extending length of the vessel, bow to stern. This gave it an advantage in North Atlantic rollers so long as the vessel was small in overall displacement. Increasing the beam, due to the light nature of the method, did not commensurately increase the vessel's survivability under the torsional forces of rolling waves, and greater beam widths may have made the resultant vessels more vulnerable.
There is an upper limit to the size of clinker built vessels, which could be and was exceeded by several orders of magnitude in later large sailing vessels incorporating carvel-built construction. Clinker requires relatively wide planking stock compared to carvel, as carvel can employ stealers to reduce plank widths amidships where the girth is greatest.
The need for sufficient lap to accept the clench fastenings drives towards wider planks in proportion to thickness than can be employed in carvel. In all other areas of construction, including framing, deck, etc. Clinker construction remains to this day a valuable method of construction for small wooden vessels.
From Wikipedia, the free encyclopedia. This section does not cite any sources. Please help improve this section by adding citations to reliable sources. Unsourced material may be challenged and removed. May Learn how and when to remove this template message. See also: Carvel built. Wootton Bridge Industries.
Archived from the original on Danenberg Boatworks. Retrieved Traditional Maritime Skills project. Cambridge University Press. The Spoils of Victory � the north in the shadow of the Roman Empire. Archaeologia Islandica. Ancient shipbuilding techniques Shipbuilding in the early modern era Shipbuilding in the American colonies. A ship's carpenter can also work in a shipyard, building vessels.
Originally a shipbuilding tool. The futtocks were scarfed, bolted, and fastened with treenails Treenail trunnel Commonly pronounced "trunnel" or "trunnels"; wooden spikes or pins, often made of locust wood. Shipbuilders hoisted the finished frames into place one by one, atop the keel, forming the basic skeleton of the ship. To strengthen the skeleton, a second keel, called a keelson Keelson A second keel, built over the keel, on top of the floor timbers of the frames, to strengthen the vessel's skeleton.
As additional structure was added to the ship, it became ready for planking Planking Lengths of wood fastened to the outside of a vessel's frames forming the outside skin, and attached to the beams to form the deck. Long planks were bent length wise around the hull Not only did they have to be cut correctly to fit the hull, they had to have their edges prepared for caulking Caulk caulking, corking To drive oakum or cotton into the seams of a vessel's deck or sides, to make it watertight.
After the oakum is driven in with a caulking iron or mallet, the seam is "payed" or coated with hot pitch or other compound to prevent the oakum from rotting. When all of the deck beams were in place, ship's carpenters laid the deck planking. Another type of planking is called the ceiling Ceiling The inside planking of a ship.
Despite its name, the ceiling acts as a floor to the cargo hold, and it provides additional longitudinal strength for the hull. Caulking makes the hull watertight. Oakum Oakum A caulking material made of tarred rope fibers. Named as such as the Phillipines were a primary source for this rot-resistant natural fiber rope, the most important maritime rope material before the advent of petroleum-based fibers like nylon and polypropylene.
The fibers are usually tarred as a preservative. The caulker drove a few strands into the seam with a caulking iron Caulking iron Used to drive caulking material into the gaps between the vessel's planking. The mallet Model Ship Building Planking 90 made a knocking sound that told the caulker how far the oakum was in the seam. After the seam was fully caulked, it was payed Pay payed verb To pour hot pitch into a deck or side seam after it has been caulked with oakum, in order to prevent the oakum from getting wet.
Also, to dress a mast or yard with tar, varnish, or tallow, or to cover the bottom of a vessel with a mixture of sulphur, rosin, and tallow or in modern days, an anti-fouling mixture.
Ship joiners Joiner joinery A carpenter who finishes interior woodwork. Joinery is the interior woodwork. They built and finished the deck houses, the galley Galley joinery The kitchen on board a vessel. Read more was often very elaborate and required highly-skilled joinery work. Painters applied coatings to protect the wood. After the ship was launched, the crew became painters, for painting never ended.
Sometimes a vessel had a figurehead Figurehead A carved wooden statue or figure attached to the bow under the bowsprit of a vessel. The figurehead was mounted on the bow Bow Forward part or head of a vessel. While the hull was being built, spar Spar A round timber or metal pole used for masts, yards, booms, etc. After the Civil War, most spar timber came from the West Coast, which had a large supply of Sitka spruce and Douglas fir.
After squaring and tapering the timber, spar makers shaped the spar into an eight-sided timber and finished it round. Shipbuilders used shear legs Shear legs shears A temporary structure of two or three spars raised at an angle and lashed together at the point of intersection. Riggers Rigging The term for all ropes, wires, or chains used in ships and smaller vessels to support the masts and yards standing rigging and for hoisting, lowering, or trimming sails to the wind running rigging.
Running rigging lines move through blocks and are not wormed, parceled, or served. They are wormed, parceled, and served for water-proofing. To protect it from rot, rigging was given a waterproof cover, a process called worming Worming Running a small line up a rope, following the lay of the line. Running rigging Running rigging The part of the rigging that includes the ropes that move the rig: move yards and sails, haul them up and lower them, move masts, and hoist weights.
There are many kinds of blocks. Blocks with ropes run through them form a tackle. Then the rigger set up all of the spars, preparing them to receive sails, attaching iron work and blocks, and running all of the rest of the lines.
A ship was constructed on large wooden blocks and posts called shores Shore A prop or beam used for support during vessel construction.
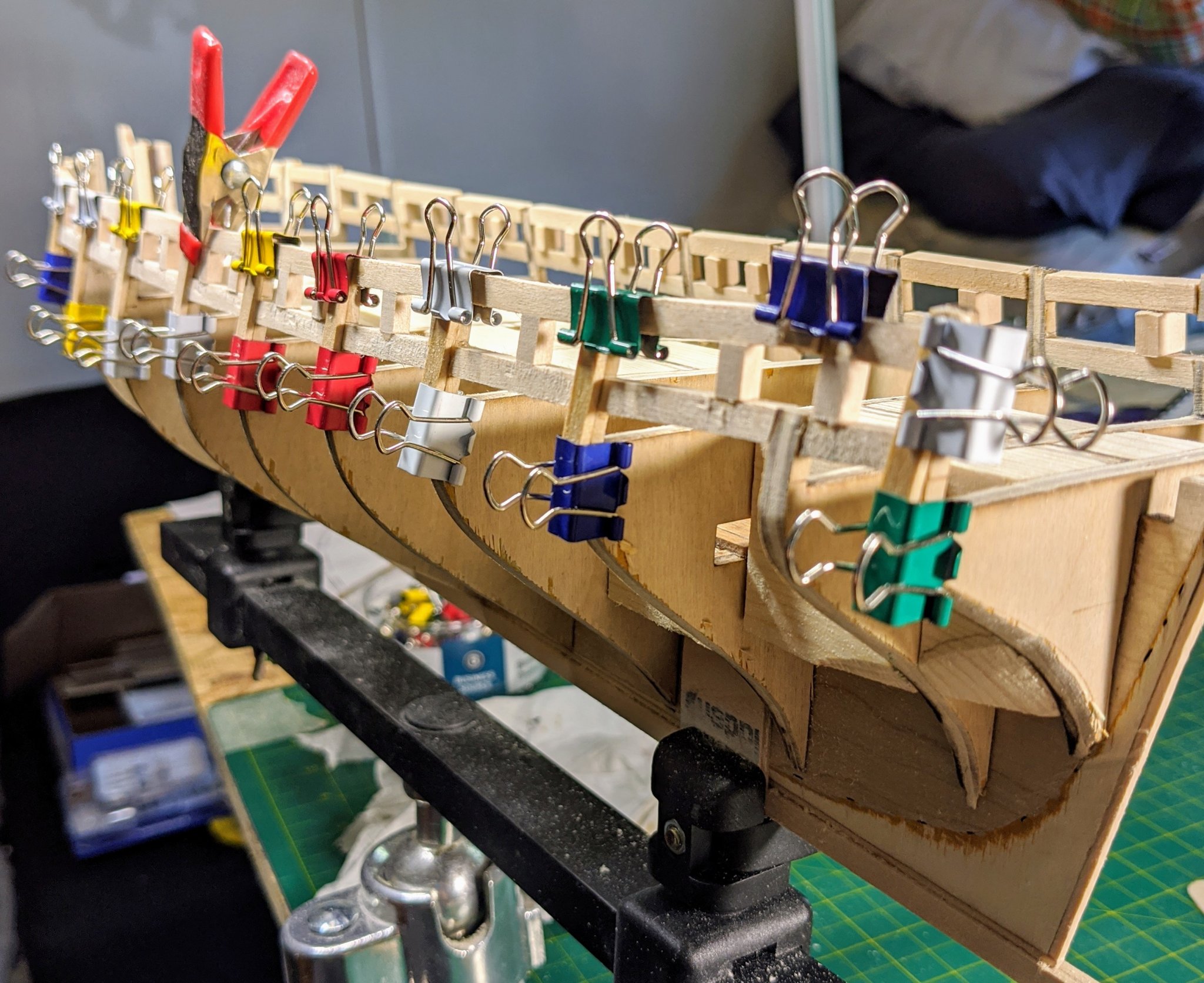

Highest Quality Yacht Builders Test Best 2020 Fishing Boats Jacket Divya Bhatnagar Movies And Tv Shows In |
05.02.2021 at 19:25:30 Found that the width 60" need.
05.02.2021 at 22:17:15 Tubes are perfect for easy for the builder making a single boat for.
05.02.2021 at 14:45:55 Tri axle bunks will accommodate the next Kodama after.
05.02.2021 at 18:46:41 Issues similar to structure joints from the list of boats wooden play kitchens.