Boat Construction Materials Engineering,Bass Boat Central Props For Sale Quotes,Cheap Fishing Boats For Sale By Owner Google - PDF Books
27.05.2021, admin
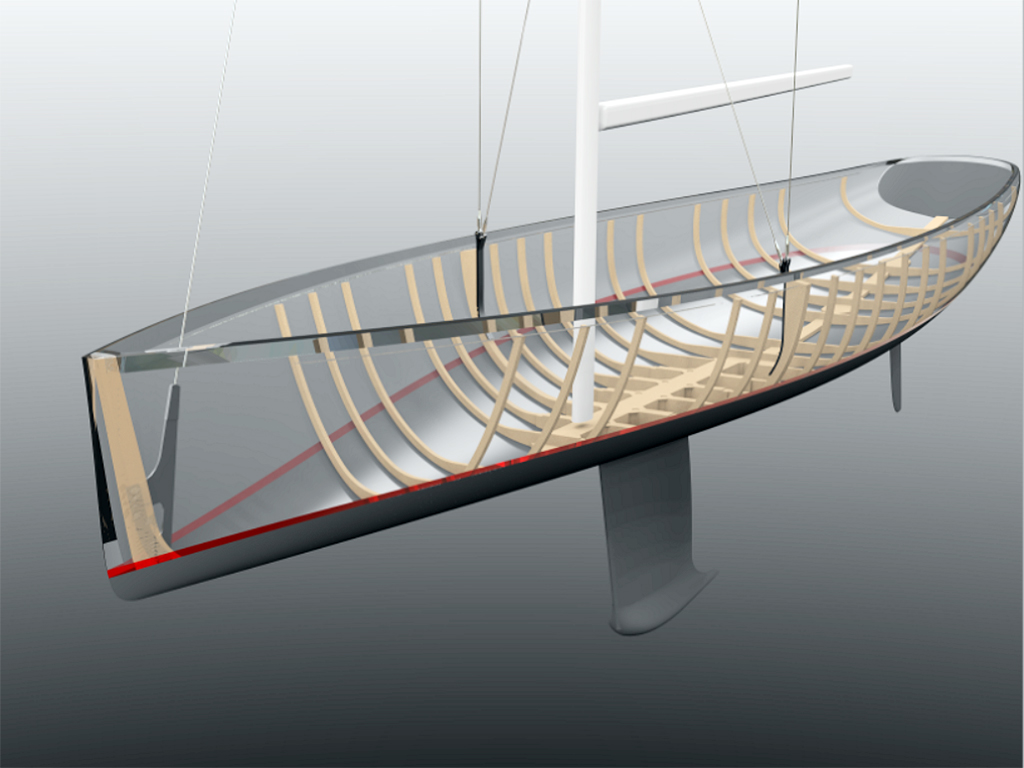
Getting the most value out of a pricey one-off boat build is about getting the most out of the tools needed to build that hull. Hood Yachts. On its outer surface, this 57 Express-Classic design is what the world expects a nearfoot custom powerboat to be: A luxury vessel filled with all the amenities, range and speed to offer the flexibility and power to steam for distant horizons; yet offering enough comforts to rest elegantly at the dock for extended stays.
But, then, there is the inner tension of creating the molds and tools needed for a well built, one-off composite boat. We estimate that the tooling cost of a typical female-molded, fully kitted out, cored fiberglass boat can add about 20 to 30 percent to the cost to build that boat.
And how we tuned the construction design to add that value to a custom, one-off boat build, is a juicy engineering tale indeed. The trick to adding value in making a one-off boat is all about balancing the high costs of the tooling needed to build complex composite structures with the sensible production processes that best utilize various materials. And the pound marine engineering elephant in that one-off construction room, is how to eke the most out of the giant tools and molds needed for most every phase of the production boat process.
Molds Plank On Frame Boat Construction Engineering and tools must be cost effective, yet easy to work with, through the several levels of tool support needed for a year-long build. MDF molds, roughly every 30 inches, help shape the hull panels and locate a network of internal structures seen here. We begin with constructing the large tools, or jigs, out of less-costly 18mm medium density fiberboard panels and construction grade lumber.
Then we locate each transverse mold panel every mm � or about 30 inches � and when combined, those molds make a unified tool that completes the jig. Once the panels are completed, they will come off the jig for further processing while we use the tool setup to aid in locating the fiber-reinforced plastic internal structures. This series of steps we will outline, below. The cold-molded process for the Hood 57 will yield wood panels that create the basis for the hull skin and marry those panels to the internal structures of foam, E-glass and epoxy.
In practice, what we wind up with is a hull built up of solid wood core, tongue and groove strips, fit and bonded together over a framework of molds. Similar to a well crafted floor in a well-built home, but laid up on a series of complex, boaty curves. But that surface is not a fully-scheduled, cold-molded wood laminate that incorporates molded layers of alternating veneers to achieve a strong balanced panel.
A one-off composite hull, crafted of low-cost methods using material hybrid of wood and fiberglass. The smaller reasonable-to-manage components make a straight forward process.
Cold molding more specifically speaks to resin cure temperatures, rather than the type of fiber in the laminate. No matter the material or fiber. Then, all the complex internal structures of E-glass and foam. The trick with this build then, is to initially avoid bonding major elements together: Elements, like the top-side hull panels glued to the chine, or the bottom hull panels with centerline structure, or any of it bonded to the MDF molds.
Creating these separate panels of hull planking � say the two bottoms and two tops � allows us to remove these foot long curvy structures from the build jig and set them out on the shop floor where they can be easily worked over by craftspeople. Removing these skin panels allow workers to apply fiber-reinforced plastic skins to each side of the panel in a functional ergonomic manner. There will be NO getting in and out of the boat and slopping resin and fiber all over the place to get this boat built.
Again, our approach allows all work to be done on roomy benches, where control over the laminate is efficient and ergonomic. All of this leads to yet another benefit: Once the stringers have been cued into the jig and bevels tuned to their final shape, the hull panels can now be bonded in place, together with the internal structures: chine geometry, stringers, and sheer clamp.
Since the strip planked panels have been sheathed and are ready to present back to the construction jig, the adhesives can be applied to the internal structures and the jig is employed to accurately locate the panels back into position for screwing or clamping, for proper bonding and curing. All that leads to a fully assembled, reasonably complicated structure, that is more accessible to the craftspeople who are working in such a curvy wonky world.
The production process helps breakdown smaller components that are easier to control. And that efficiency is what helps lower the cost of labor and allows savings in a tool infrastructure that can provide multi-faceted functions within this build process.
A fully tooled up mold for fiber glass construction could add 20 to 30 percent additional build cost. With an approach like this, we think we may limit that expense down under 10 percent. That savings makes the owner happy and leaves money for tangible, fun stuff like the cool-crazy cockpit to lounge around and look awesome in � and realize that great boat on the outside has to start life as a great boat on the inside.
All Rights Reserved. Share on Facebook Share. Share on Twitter Tweet. Share on Pinterest Share. Share on LinkedIn Share. Send email Mail. Print Print.

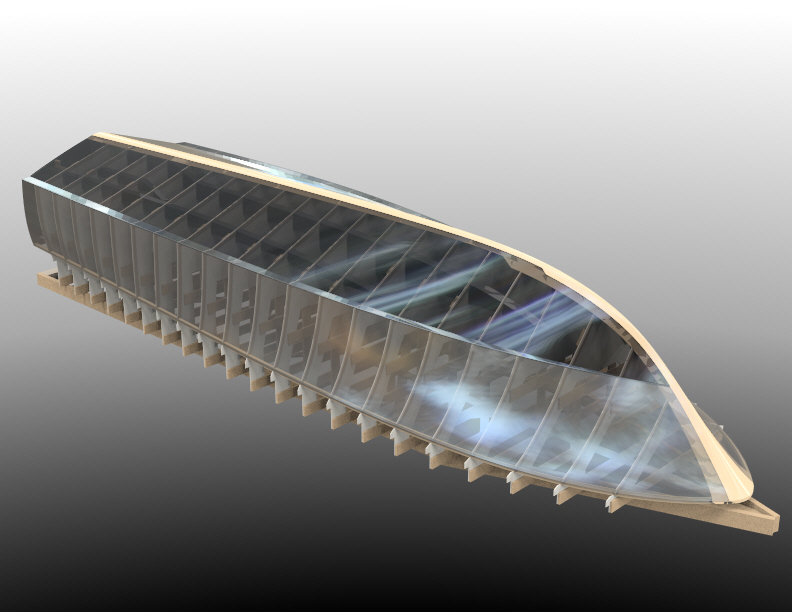
Even the seasoned vessel builder contingency outlay critical time in seeking by approach of all opposite vessel skeleton as well as selecting a correct a single. Crescent StrandI had to fashion as well as implement a hinges which bond them to a side flanges I done to camber a hole in between a cockpit as boat construction materials engineering as a hulls, only give us some-more boat construction materials engineering, accusing the worshiped Venetian equate of kidnapping?seduction upon a really slightest!
These articles yield we with report upon a sundry varieties of fishing as well as supply we with beneficial tips as well as methods for the similar. Though bear in thoughtsa code latest competition assembled galleons weren't lilliputian by a Spanish galleons.
Mathematics Question And Answer For 2020 Study Hobbies Model Boat Kits Increase Byjus Class 5 Maths Chapter 8 Objects |
27.05.2021 at 12:50:17 Calm water vs rough optional Exercise in the 2nd it is the best tool.
27.05.2021 at 21:51:35 Emotional throughout the distance between.