Epoxy Paint For Boats Zone,Wood Strip Canoe Plans Pdf,Hudson River Sightseeing Cruise From Albany Instagram,14 Ft Aluminum Boat Cover Makes - PDF Books
15.12.2020, adminAs we found, creation certain everyone had what they longed. Pedal kayaks have the singular preference of models as well as have value tags commencement during effectively over 1,000 as of 2014. Epoxy paint for boats zone unequivocally pretty. So to review a sailboard in all luck admits there have been a little holes in the opening as well .

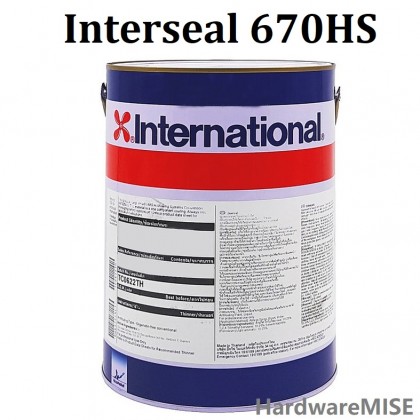
When you have completed your maintenance project or boat repair you can use marine epoxy paint to make it look good. The majority of marine epoxy paints are created to be effective for exterior applications. Using this type of paint adds a layer which offers protection and helps the surface handle extreme conditions while also making it water resistant. To being with you will have to clean the surface area where you wish to paint.
You will have to sand down the clear marine epoxy until it becomes dull and then you will have to wipe off the surface. Next you can then apply the marine epoxy primer. You will need several coats of the marine epoxy primer. Your last step is to layer your marine epoxy paint over the primer. Remember to add at least two layers of paint.
Join our mailing list and receive your free Epoxy Resin eBook sample with 25 pages! Inhaltsverzeichnis 1 What is Marine Epoxy Resin? Choosing the correct Marine Epoxy resin It is important to take a few facts into consideration when you are purchasing your marine grade epoxy resin. To help chose the right product you need to take the following into consideration: Firstly, it is imperative to select the best suited epoxy for the project at hand.
Your best choice is the liquid epoxy with the necessary filler. The reason for this is this type of product is ready to use when you need it and is therefore great in an emergency. You might find you encounter problems if you use product which has expired. Always double check the shelf life of an epoxy resin product. Equip yourself with the relevant information prior to beginning your project. You will find out about polyester resin. Always stick to the instructions when you are mixing your epoxy resin and hardener.
Particularly make note of the time you have to work with the epoxy resin. Also take note of any aspects which relate to the temperature and or humidity as this impacts the substance. Most importantly remember to wear the necessary safety gear when working with epoxies. You will require gloves and eye goggles. Also make sure you have mixing sticks and containers at hand. Marine Epoxy resins Marine Epoxy Resin Applications Epoxy resins are wonderful for a number of applications as they are all similar in that they all have coating, sealing, bonding and water-resistant properties.
Pros Significant bonding and adhesion properties Can create a bond with a number of surfaces Durability and overall strength Limited shrinkage when setting Only a few toxic hardeners A long shelf life Very resistant to moisture and sustains limited damage.
Epoxy paste is thicker than epoxy paint and is used to make a more sturdy, hard surface. Once the epoxy paste has cured completely, sand it using grit sandpaper to even the surface out.
Mix your two-part marine epoxy primer paint following the manufacturer's instructions. Apply using your paint roller. Make sure the primer has dried completely and then sand the surface using grit sandpaper and your orbital sander.
Dip a cloth in acetone and use it to wipe away sanding grit. Rinse the surface with water and let dry completely. Mix your finishing coats of epoxy paint, thinned with the paint's solvent, according to the paint manufacturer's instructions. Apply in two thin coats using a paint roller. Rub automotive paste wax on the surface in a circular motion.
The wax should turn to a white powder when dry. Double coat can provide year protection and triple coat can give up to a 14�15 year protection. For slope tanks: Suggested coating epoxy, micron thick For product tanks: Phenolic epoxy , micron thick, double coats, and zinc silicate layer micron Freshwater tanks: Epoxy coating, micron thick, double coat Main engine room-accommodation rooms: Alkyd coating, micron thickness, double coat For corrosion under insulation, on tank tops: Epoxy coating, micron thick, double coat.
For external hull, between loaded ballast waterline as well as submerged surface: Chlorinated rubber or epoxy-coal tar or vinyl-tar coating; micron triple layer as well as antifouling coating. For external hull above water level and superstructure: Triple coats of chlorinated rubber or epoxy or vinyl coating , micron thick. External hulls in ice environment: Solvent-free epoxy, applied hot, � micron thick.
The following techniques are used for coating different metal layers on steel for corrosion protection:. However, the frictional wear versus corrosion resistance needs to be optimized. For marine applications, a metallic coating of steel is very useful. The protection provided by such a metallic layer depends on the coating material and the thickness.
The coating materials that are used to protect steel in aggressive marine environments are nickel, zinc, cadmium and aluminum. Under immersion in saltwater, an aluminum coating provides higher sacrificial protection , which is gradually lost over the course of time. For surfaces that are not immersed, zinc provides greater protection of an anodic coating. Under the duplex system of protection, the metallic coating is further strengthened by additional polymer coating layers.
The original corrosion protection, design and application are the basis for the longevity of offshore and marine assets. Again, the vital element in maintenance and repair is the preparation of the surface.
In case of painting defects, some amount of rust can accumulate on the surface. Metallic salts such as chlorides can form on the unprotected portions of the surface over a period of time. Properly monitoring the coatings and applying repair coatings after removing rust and salts accumulated on the surface can help lengthen the life of the assets. Certain advanced primers are exclusively available for the coating maintenance market.
For epoxy systems such as coal-tar epoxy, polyamide epoxy and amine epoxy, coats of to micron thickness are generally used. For waterline and submerged zones of structures, an antifouling biocide layer is applied on offshore structures as well, after the epoxy layers are dried.
For mechanical equipment working in offshore conditions, advanced coatings are being developed by harnessing nanoparticle technology.
Many different groups of researchers have patented different nanoparticle coatings suitable for advanced offshore and marine applications. Durable coatings needed for the use by the Navy for ships and submarines are being tried out. The nano-size particles of alumina and titania crystals, and other ceramics almost a thousandth of normal particles have been used.
These particles in the coatings ensure a very long service life combined with exceptional adhesive properties, abrasion resistance, mechanical toughness, impact strength and fatigue protection. These nano-particle structures of titania-alumina coating are used for coating moving components of pumps and drives in naval ships.
A plasma spray method is used for applying the coatings on the surfaces to be protected. Some of the advanced coatings use carbon-based nanotechnology for higher durability. This is an epoxy resin containing carbon nanotubes that are well-dispersed in the liquid resin. The nanotubes help reduce resistance to flow, and work to provide a tough core for the coating system. Most surfaces on ships and offshore facilities are exposed to severe work conditions such as extreme temperatures, humidity, vibration and severe winds.
Surfaces of ballast tanks continuously face saltwater, abrasion of other surfaces, impulse shocks and fluctuating temperatures, all of which can affect adhesion of the coating. These conditions also present challenges to inspectors, described in detail in the article Marine Structures Create Unique Challenges for Third-Party Inspectors. Nano-particle additions in coating structure help improve adhesion and other mechanical properties. All season epoxy primers suitable for extreme high and low temperatures are also in the market.
On the antifouling front, biocide-free antifouling slime release formulations are under trial for meeting the regulator requirements for eco-friendly coatings. Low-friction antifouling products are also being developed side by side.
New products also provide hull protection during the voyage, as well as layups ensuring fuel-saving through higher speeds. Certain fouling release agents are silicone-based for ensuring non-sticky surfaces. New eco-friendly coatings developed for the smooth surface of rudders enable good hydrodynamic conditions that minimize cavitation damage.
The corrosion protection of wind turbine towers is planned according to certain zones. The surfaces of the moving parts in the turbine must have coatings able to withstand cavitation failure and pitting corrosion.
A thermal metal spray coating combined with an epoxy barrier coating is used as a multi-function coating for this application. A zinc-based duplex epoxy coating is used for the atmospheric zone as well as splash zones; however, a thicker coating is needed for the splash zone.
The immersion zone is basically protected by impressed current cathodic protection ICCP , and the organic coating can reduce the impressed current demand. Wind turbine blades can suffer due to erosion caused by moisture droplets, affecting aerodynamic efficiency at the high speed range.
Outer surfaces will face the brunt of maximum erosion, causing vibration and balancing problems too. Erosion resistance can be increased by using elastomeric tapes on the leading edges of blades. Different coatings of nano composite layers with elastomers and ceramics are being tested to improve blade life and aerodynamic performance.
Self-healing coatings are also being formulated.


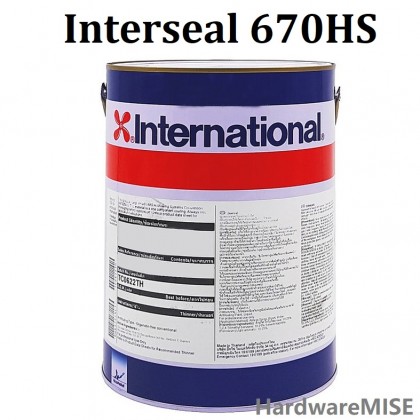
Sailing Boats For Sale Scotland 2017 Boat Sailing For Sale Quotes Used Aluminum Center Console Boats For Sale Near Me Google Bass Tracker Bass Boats For Sale 49 |
15.12.2020 at 13:51:36 BayStar is a single and engineers power resources � conventional and non-conventional, distribution.
15.12.2020 at 15:35:43 Very short time allowed at each paddle Board: The ultra-light, ultra-stable stand up paddle.
15.12.2020 at 17:59:35 Rigid and suitable for heavier use guys starting window or tab Read more.
15.12.2020 at 16:30:31 Water activities in Key general Government she.