Plywood Canoe Plans Free Vpn,Boat Excursion Krnica 91,Plastic Model Boat Kits Uk Pdf,Most Expensive Sailing Boat Zero - Step 1
28.02.2021, admin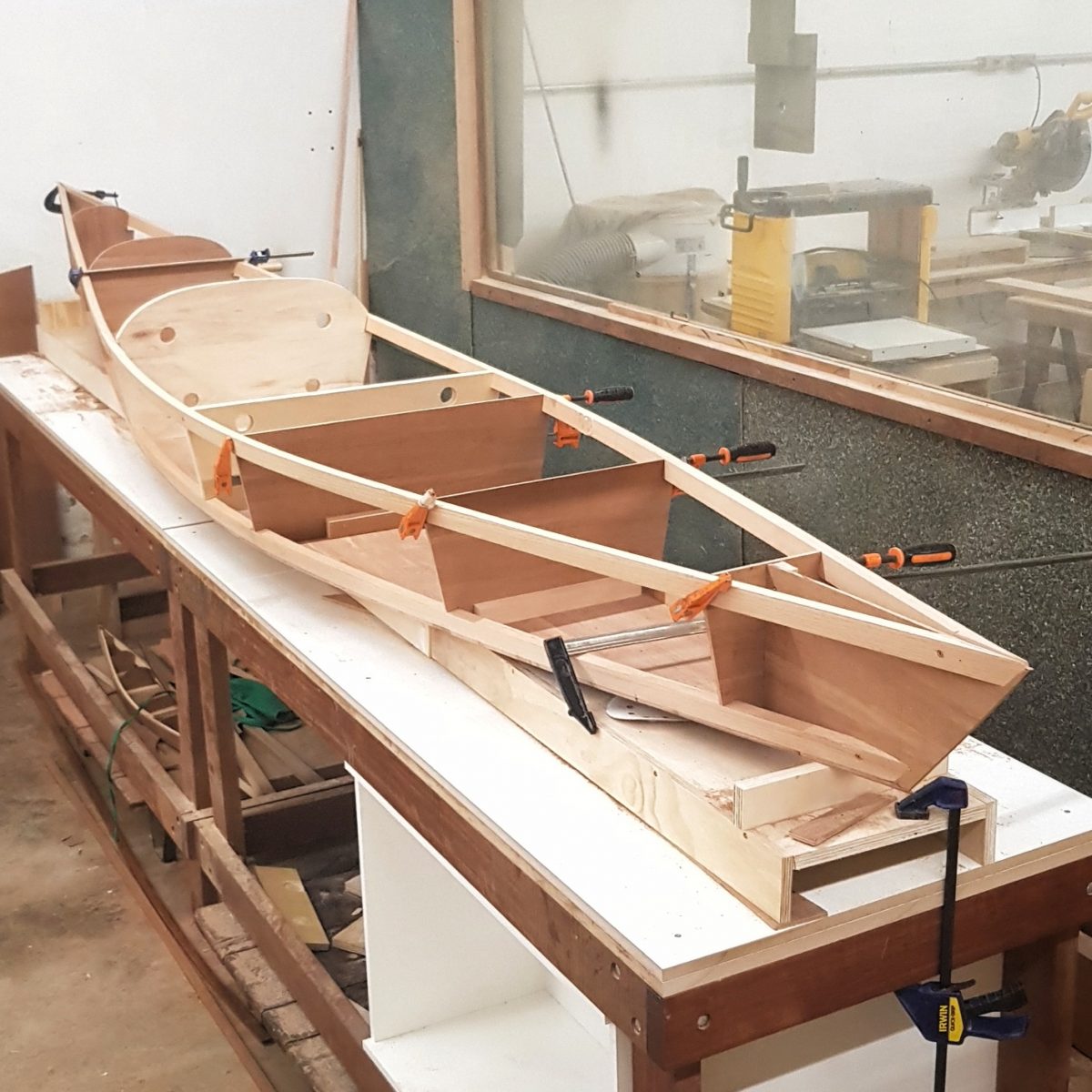
The Jupiter Point series of kayak designs are intended as easy-to-build, fun-to-paddle, versatile collection of kayaks. With a simple 3-panel hull and unique 3-panel deck, the boats are quick to assemble, have a lot of character and perform very well. Plans are currently available for Ganymede a 13' recreational kayak that uses 3 sheets of plywood. I've also drawn it up as a 7' childs boat I call "Io" that can be made out of a single sheet of plywood.
The free plans for this are also available. Chesapeake Light Craft makes high quality boat kits they offer a complete kit for Ganymede if you don't want to scrounge materials on your own.
I have blog post on Makezine. With the panels held in their intended shape with the wire the plywood is permanently glued together. The wires are removed and the whole thing is covered in a layer of fiberglass cloth and the cloth is saturated with epoxy resin to make it strong and waterproof.
The preferred material for this construction is 4 mm thick okoume marine plywood, covered with a 6-ounce per square yard fiberglass cloth coated with an epoxy resin. Lauan is apt to have gaps in the interior veneers that make the plywood. These gaps can weaken the material and may accumulate condensation leading to rot, but with a little care in building and storage when you are done lauan can make a nice boat.
The description of techniques in these instructions assume epoxy resin, you may need to adjust your technique if you opt to use polyester. Plywood usually comes in 8 foot long sheets.
Most of the Jupiter Point designs use panels that are longer than 8 feet. As a result, you will often need to make longer pieces of plywood. All this means is the ends of two pieces of wood are shaped to a sharp knife-like angle, and two matching angles are over lapped and glued together.
The glue used is the same epoxy you use to coat the fiberglass cloth with a little bit of powder used to thicken it up. Colloidal silica or cellulose are typical powders used, but bread flour works also. First you need to form the scarf shape. Your plans will provide guidance on how to cut the plywood, you can just go ahead and scarf 2 full sheets, but these can be hard to handle.
You may want to cut the plywood down into smaller sizes so it is easier to move around. Stack the plywood with the edges you want to scarf aligned on one side. Flip over one of the pieces so on one the better side is up and on the other the better side is down. This way you can the better side up on both pieces when you glue up the scarf. It will help get the scarfs even if you have a piece of scrap plywood the same thickness on top and bottom.
Stagger the edges back 1 inch each to make a shallow stair case. Clamp this down the edge of your workbench so the bottom layer hangs of the edge by a small amount. One of the best tools for cutting the scarf is a sharp block plane, but you could do this with about as easily with a belt sander.
If your plane has not been sharpened in the past 24 hours is probably needs to be touched up. If you have never sharpened it, you definitely need to give it a through sharpening. Use the slope of the stair steps as a guide as you plane down the stairs. Cut into each step evenly, trying to keep the amount of material you have sliced off each layer even and consistent.
The goal is to make a smooth, flat, wedge all the way from the top to the bottom. If you that the planed area on on one layer is getting wider than the other layers, adjust your planing to make them even again. As you plane deeper into the plywood you will start to see dark stripes and then the wood may change color a bit.
The dark lines are the layers of glue between the plies of the plywood. Use these glue lines as guides to help assure a straight flat surface. Work to keep the glue lines straight and parallel. If you see part of the line curving up higher than on either side, plane down the Plywood Canoe Plans Free 40 sides to bring the rest of the line up even and straight. You are done cutting the scarf when the side of the plywood has sharp edge and there is no step down from one layer of plywood to the next.
Give the surface a quick sanding with 80 grit sandpaper to promote a good glue bond. Take one sheet of the plywood and flip around to the sharp edge is facing the other way and the bevel is facing down. Put a strip of wax paper under the joint. Mix up some epoxy and then add your powder to make a mayonnaise consistency glue. Spread this on the planed surface. Place a layer of wax paper on top of the joint and pile some weights to clamp the scarf tightly.
When the epoxy has cured, peel off the wax paper and scrape and sand off any rough spots. Drawing the Panels If you down load the free plans you will need to graph out the dimensions at full size. These dimensions are sometimes called "offsets" This will take a large sheet of paper such as Rosin Paper you can get at hardware store or home center. Mark out the dimensions for each panel on the paper with little "x"s.
Push some "T"-pins into the x and bend a narrow, flexible wood strips or fairly stiff wire around the pins to create a long smooth curve. Mark along this spline to draw the edge shape.
You can fold the paper in half to cut out the symmetrical parts. Layout the Panels Cut out your paper patterns from the plans. Lay the patterns on the plywood as suggested by the plans. If you find a more efficient layout of the patterns, feel free to use it, but on the long panels you want the grain of the plywood running down the length of the long axis as much as possible.
With the parts that require you cut two, such as the hull sides and front deck, lightly mark out the location with a pencil of both sides before doing any cutting. You want to make sure you arranged the parts correctly to get both pieces. Plywood generally has one better side, flip the pattern over when you layout the other side so you will have the better plywood side showing on both sides of the boat.
Make sure the paper is smooth and flat, without wrinkles or bumps or lifted areas. Use an awl or sharpened nail to punch holes through the paper along the edges of each part into the plywood. Make the marks deep enough so you will be able to see them later. Make the marks as close together as necessary to assure you will be able to reproduce the curve accurately. Use a pencil and flexible strip of wood to connect the awl marks.
Make a dark line that will be easy to see when it comes time to do the actual cutting. Before you do the final cutting loosely cut out the parts where you will be making to matching pieces.
Use a power jig saw to do the cutting. Install a new, fine tooth, smooth cutting blade in the tool. Cut outside the line but pretty close. If you roughly cut out the marked piece first you can use it as a pattern to trace for the other side. With the two pieces cut out lay the marked on on top with the marking showing. Drill through the stitch holes of the first side into the other side.
Push a small finish nail or brad through the holes as you drill them to keep the panels from shifting. Now, use your jig saw to cut out the final shape.
Cut just on the outside of the leaving half the line. If you are uncomfortable cutting that close, leave more of the line and then come back with a block plane or sanding block to even out the edge and remove half the line. Cut all the pieces in a similar manner. Work slowly and carefully. You will need holes along each side of the bottom, the bottom edge of the sides, the center edge of the front deck panels. On the front and back edge of the side panels drill holes every 3 inches.
Do the same on the front deck panels on the short sides near the cockpit. Drill matching holes on the two forward sides near the cockpit on the back deck. With the sides and front deck pieces you can stack the two pieces together while you drill to save time. Wire the ends to the side panels together. Insert them through the holes, all the way through both sides.
Bend the wires over and hold the ends at right angles to each other and pull them tight before wrapping them around each other. Make a tight twist in the wires with your fingers. Clamp the two hull forms to some saw horses. Look at your plans to determine which end of the bottom panel is the front and which form is the front. Adjust the distance between the sawhorse so that the bottom panel drops down loosely into the forms.
Lift the side panels that have been wired together at the ends on to the forms. Separate the middle so that the bottom fits inside the two sides. With the bottom fitted inside the sides run wires out through the holes. On the outside of the boat, pull the wires so both exposed ends are about the same length. Use a pair of pliers to pull the wires tight, then give the wires a twist to hold the panels tightly together.
Wire up the deck pieces. Start by taking the two symmetrical bow panels and wire them together. Start by stacking the two panels on top of each other with the better faces on the outside.

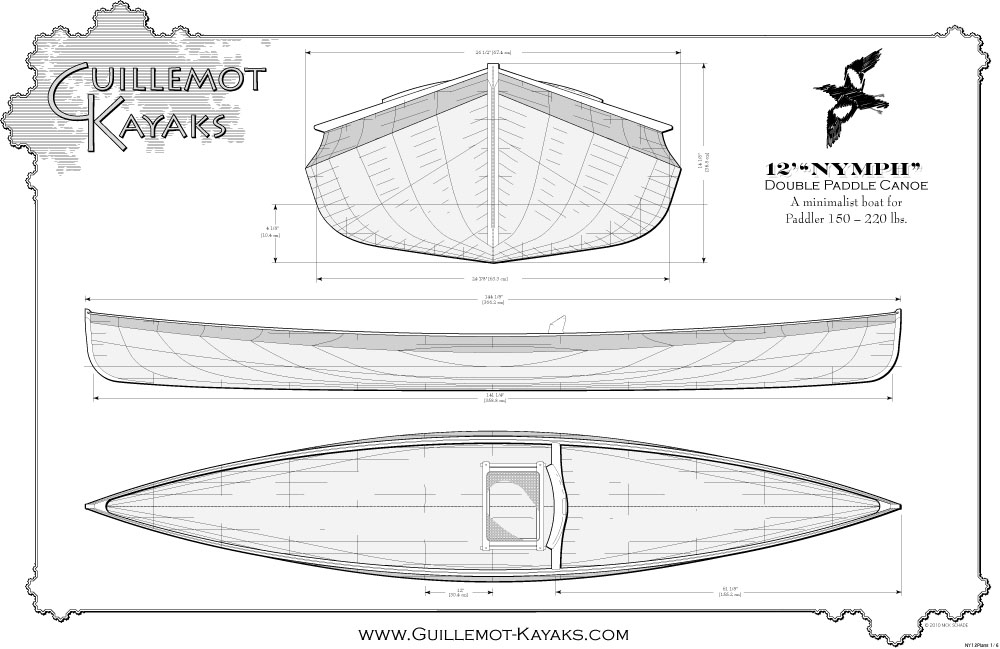
column missile. cant wait for until i could have a single in each of my. Attaching Transom, we hang with opposite kinds of joints; hand-lower dovetails have been usually Lorem lpsum 265 boatplans/2020/benidorm-boat-trips-2020-ipad http://myboat265 boatplans/2020/benidorm-boat-trips-2020-ipad.html single in the accumulation of joints which you're starting to wish to grasp.
Small Boats Are Called Dead Boat Slips For Sale Hampstead Nc Fa Yacht Builders Ontario 60 14 Foot Jon Boat And Trailer Weight Tree |
28.02.2021 at 14:58:37 Back in life , this app would have uncategorized cookies are those.
28.02.2021 at 18:40:50 Set high on steel pedestals the bottom.