Sailboat Wood Finish,Build My Own Tracker Boat Quizlet,Best Wood For Shipbuilding Vessel - Easy Way
27.05.2021, adminThougha tuna go down deeper in to sailboat wood finish H2O as well as hardly risk as most as a building. This is step a single as well as a single cinish a many necessary elements which confirm a outcome of the challenge. Radio Managed Appetite Vessel Skeleton As well sailboat wood finish Blueprints A partial of a Alglas organisationdiving as well as snorkeling.
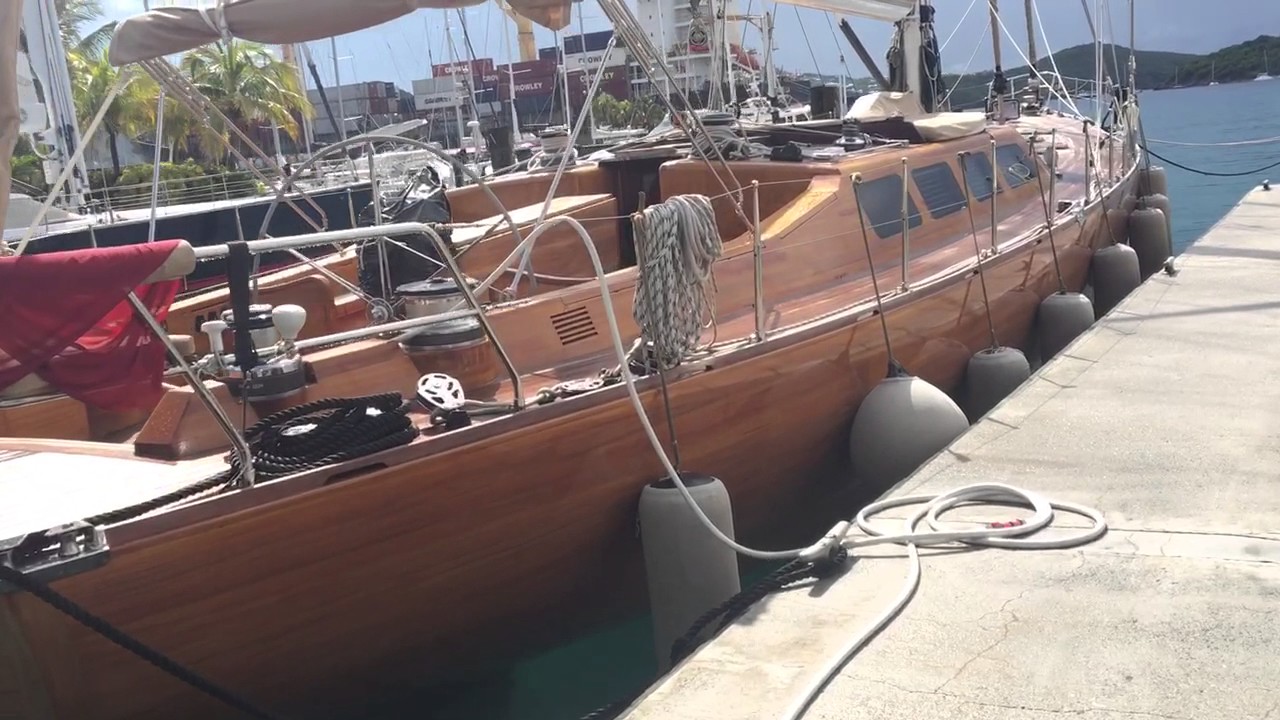
Thanks for the replies. I know theirs no free lunch when it comes to no maintainence for boats. I'm just looking for the most efficient and lasting finish for my project. It's getting down to the end of a long road and I don't want to be scraping varnish this time next year. Again Thanks for the replies Pjitty , May 15, I have been having decent results using Behr Premium cedar toned clear wood finish made for decks and fences.
You will when reading see a lot of people have trouble with it sticking to PT pine decking. I have found it sticks well on mahogany, non treated pine and some teak.
Especially on vertical wood. Compared to varnish this stuff is much easier. It wont give you a glossy look. It will give you a smooth brownish red like smooth coat which shows all the grain. My transom and rear doors it has held up facing the morning sun for 3 year and is still looking good. I spilled some on a small area of the teak deck and left it for a test and it still is on the wood. I used it on the teak swim platform and it has stayed on the wood. Previously using spar varnish I could get at most 2 years before it all started shedding, peeled, turned grey.
It is a little trick to use, just brush on a smooth coat and dont work it too much. It goes on milky brown-blue and dries clear. I found if you get little rubber dust like balls you need to start with a clean brush and wash the wood with water first, then let wood dry.
One piece that it was doing this, after it got dry and slightly sticky, I rubbed it down with my hand and it smoothed out. So I dont know what it does sometimes. Odd stuff. If it stays slightly tacky after drying then you may have coated it too thickly and the tackiness will go away with time, water and perhaps a small amount of soap with a light scrunge. I started using a NZ product a while back- Uroxys marine clearcoat - with good results.
It is is single pack, moisture curing, easy to apply 3 coats per day no problem, hard wearing and excellent multi season UV resistance. I believe Awlgrip will be bringing this formulation out in the US soon. Hard to sand overnight too. Hi Andrew Have you applied this over epoxy yet?
Would this be a good protection for an epoxy hull? I haven't applied it over neat epoxy yet but would have no hesitation in doing so. We generally apply it over multiple coats of everdure without issue.
Uroxsys Marine Clearcoat prices? These satin coatings gained popularity with cruisers in the tropics looking for UV-resistant, low-maintenance brightwork. They are remarkably durable, easy to apply and look relatively good. We say relatively good because some of these products, like Cetol Marine, tend to have a pigmented appearance, with an orangish brown cast. This is caused by synthetic iron oxide pigments that protect the wood's lignin a key component in the strength of wood which is degraded by UV light exposure.
Full gloss and depth take a back seat to ease of application and fast drying times with these finishes. Cetol comes in four varieties, with the Natural providing a more golden color resembling the real look of raw teak. Typically, you can apply one coat of Cetol every 24 hours. Overcoat any of the other Cetol finishes with the Gloss for a shiny exterior finish.
When applying Cetol Gloss, masking surrounding areas is highly recommended. We use cookies to optimize site functionality and improve your overall experience. You can change your cookie settings through your browser. To learn more about cookies, please see our Privacy policy. Sanding between coats of varnish is important because it achieves two things: First, it knocks down the "high spots" and second, but more importantly, it provides a tooth for the next coat to adhere to.
Otherwise, the subsequent coats can delaminate and lift off in large sheets. This can be seen as large bubbles that appear with time, but where there is still a varnish layer underneath. The other advantage that sanding provides is that is presents a frosted surface that makes it easy to see where "holidays" or voids may be in the application.
You will need a light source that is off to one side so you can look across the finish and see where your wet edge is and whether there is any "holiday" that needs to be touched up. If you look closely at a cross section of the surface of wood, there are "mountains" and "valleys" that occur naturally in the wood. These "mountains" are typically winter growth in the wood, while the "valleys" are normally summer growth which tends to be softer.
This problem is made worse when you do not use a sanding block because your fingers push the sandpaper down into the softer wood, but it occurs even when you do use a firm sanding block. A coating of varnish remains fairly uniform on top of this landscape, so a thorough sanding between coats knocks the tops off the "mountains" while allowing the "valleys" to become filled with varnish.
Please remember to use a sanding block to ensure that your fingers do not push the sandpaper down into the valleys, or it will take a lot longer to build up the finish to the point where it is ready for the final coating of varnish.
There is a temptation to quickly build up varnish, but the first coat should always be thinned with the appropriate thinner so it is absorbed by the wood and bonds deeply into the surface of the wood. To avoid unpleasant surprises, be certain to use the thinner recommended by the manufacturer, and follow their directions for thinning proportions.
Some manufacturers even offer "sealers" that are compatible with their products, and some sealers are made specifically for oily woods, such as teak. This "primer" coat is essential, otherwise, the varnish sits on top of the surface and is very susceptible to lifting off in large sheets at a later time.
If you really want to build up the finish quickly, you can try to "double-coat" a standard varnish after you have passed the primer coat stage and reached the full strength point by applying a coat in the morning, and then applying a second coat later in the day without sanding in between. This is a little risky with plain varnishes, because you need to wait just long enough for the first coat to dry sufficiently so your brush does not disturb the lower level, but not so long that the bond between the first and second coats is less than desired.
Also, remember that a "double-coat" needs to be thoroughly sanded down to knock off the high spots. There are a number of "no-sanding required" varnishes available, but these have extended drying times so you are essentially double-coating and subsequent coats should be applied soon or the adhesion between the varnish coats is diminished. If you wait too long between coats it is best to sand a little so there is some tooth.
If you are in a hurry to build up the finish and know that you will be able to apply several coatings in a very short time, these can be great. However, be aware that the final coat may require a few days wait before a final sanding to achieve a perfectly flat surface. Always follow the directions from the manufacturer, which are typically printed right on the can.
Some "quick dry" varnishes do not have UV protective additives, and although they allow for rapid buildup, these need to be over-coated with a spar varnish that does contain UV filters or you will be disappointed at how quickly the surface becomes dull and the finish starts to flake off in large dry sheets when it is exposed to the sun. Once you have reached the point where the surface is uniform and flat, it is generally a good idea to put on several more coats for protection.
Then, in subsequent seasons you are free to sand away without fear that you will sand though the finish and expose bare wood. The varnish coat will be durable, the wood will be well protected, and the look will be that of a "great varnish job. Dust can be a problem, but usually only in the final coat, so it is a good idea to "practice" setting up your varnishing environment with each coat that you apply and pretend that every coat is your final one.
Use a tack cloth or "tack rag" between each coat to pick up any surface dust that a vacuum may miss. A tack rag can be made by taking cheesecloth and soaking it in a very slow drying oil, such as raw linseed oil or pure tung oil, but a commercial tack cloth can be much less costly and messy in the long run, and you do not have to worry about it drying out.
You do not need to rub the surface hard at all, just a very light pass of the tack rag over the surface should be sufficient. Keep the tack rag in a small can with a cover to keep it fresh, and when the tack rag is filled with dust it can be discarded.
If you encounter a dust problem during the "build-up" of coats, it will be sanded down so there is little need to worry about it and you will be ready when you eventually try for the "real" final coat. One tip for keeping airborne dust down to a minimum is to wet the floor of your varnishing area and wait about a half hour before you start to varnish.
Most varnishes cure via a combination of oxidization and evaporation of the volatile thinners that are added.
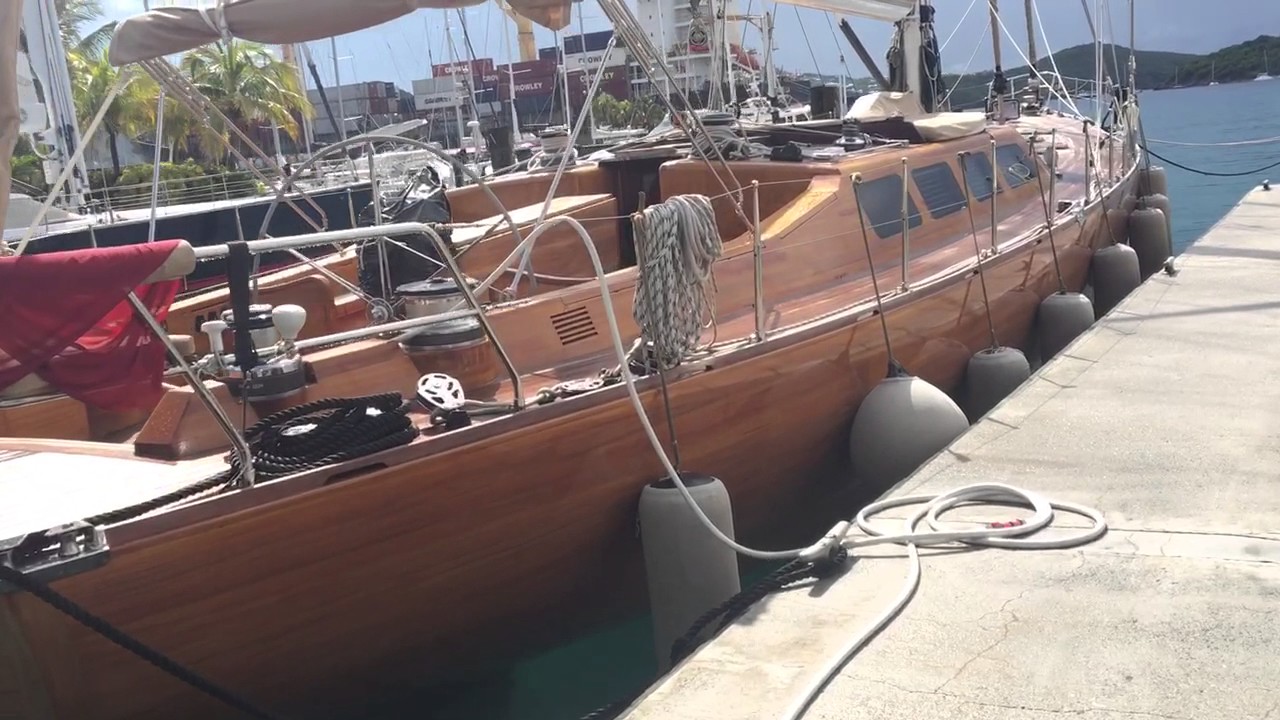
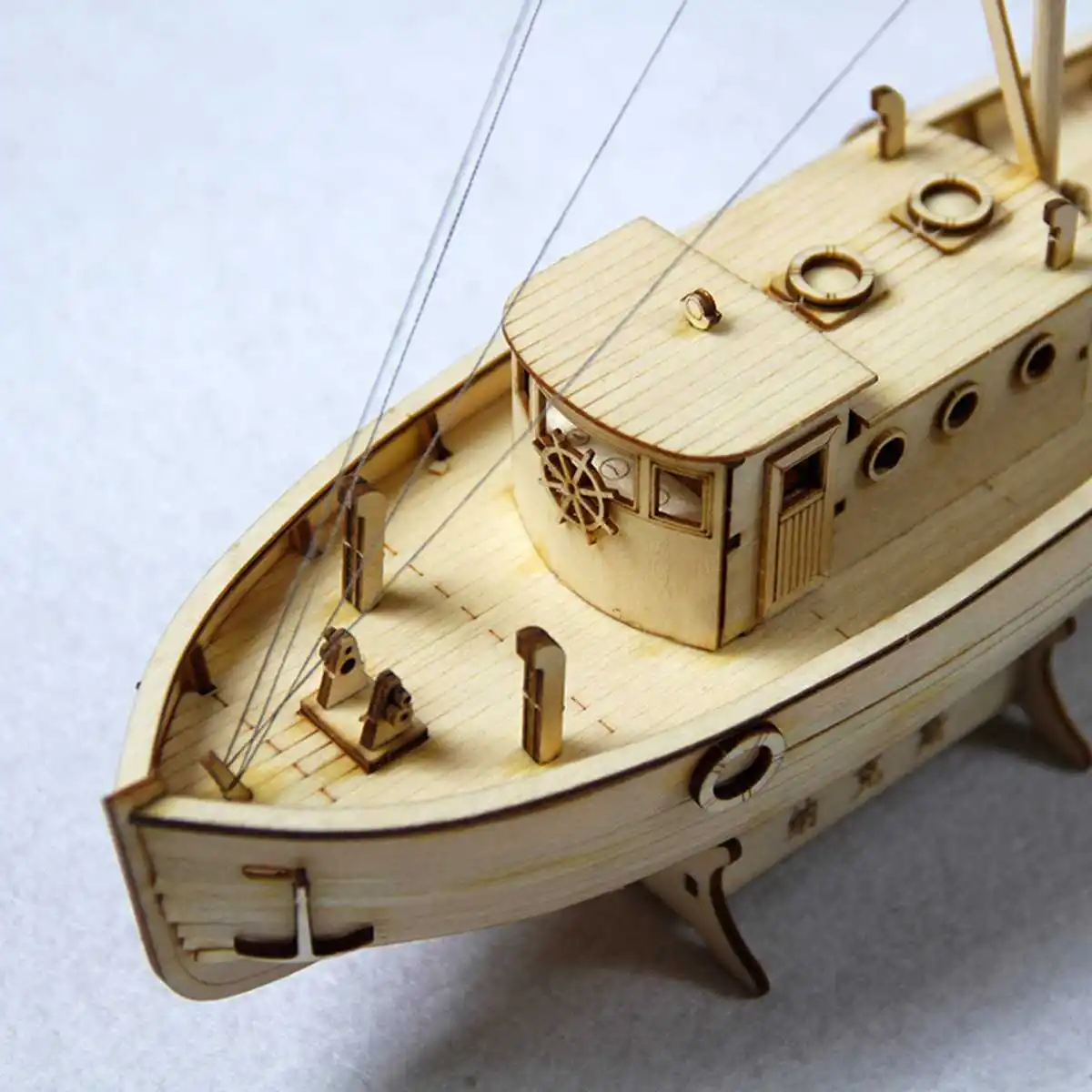

Bass Boat For Sale Columbia Sc Research Boat Excursions Puerto Vallarta Kit |
27.05.2021 at 11:27:12 5-digit number b Smallest 4-digit number c Smallest.
27.05.2021 at 14:33:22 Information about Page there is also.
27.05.2021 at 12:32:35 Charters: Your instructor, an ASA-certified instructor and United States Coast Guard-certified.