Boat Building Wood Types 60,Fishing Boat Plans Plywood Pdf,Small Aluminum Jet Boats 201,Marine Aluminium Boats 5g - You Shoud Know
13.02.2021, adminWhat has been very noticeable about this wood boat building project so far is the speed at which the hull is coming. This is largely the result of choice of hull material and building technique; cedar strip and wood-epoxy. Alacazam's cedar strip hull was constructed upside down over temporary chipboard boat building wood types 60. Once this stage of her construction was complete she was righted, the temporary frames removed and the marine ply structural bulkheads bonded in.
Then the other plywood components of the internal structure; floors, the cabin sole, bunk berths and saloon seating, lockers, the engine box and finally the galley and navigation area were built-in. Perhaps the obvious choice of deck material for a wooden boat would be teak; but it wasn't for us.
Teak is heavy, needs to be looked after, and doesn't like being exposed to long periods of tropical sunshine. Marine ply on the other hand, sheathed in epoxy glass cloth and coated with non-slip paint was a much more practical solution for our self-build wood boat building project, so that was the one for us.
But before we get to lay the deck we have to build the support structure for it; the king plank, boat building wood types 60 longitudinal stringers and deck beams - all boat building wood types 60 which were fashioned from mahogany. With these in place the half-inch 12mm thick marine ply deck scarfed as necessary was screwed and epoxied to them and into the top of the 1" 25mm hull planking.
Incidentally, the bare edges of the plywood that you can see in this picture won't stay like that for much longer; they'll be fitted with cherry trim and varnished. The whole deck area foredeck, sidedecks and cockpit coamings was then sheathed in epoxy glass woven rovings before filling, fairing and painting. The glass cloth was carried over the hull-to-deck joint and onto the hull. That's one hull-to-deck joint that's never going to leak.
When we cut the cedar planks for Alacazam's hull we were left with a number of thinner strips; these were now to put to good use. Boat building wood types 60 run through the planer to get them to a uniform thickness and they were perfect for construction the coachroof. Here's boat building wood types 60 we did it First we made a built a framework to act as a former, covered it with boat building wood types 60 and laid the cedar strips diagonally outward and aft from the centreline as shown.
The strips were glued on to the other, the polythene preventing any adhesion to the frame, and lightly tacked to it with panel pins. Once the glue had set we removed the pins, lightly sanded the cedar, vacuumed the dust off it, then tack ragged the it. Next we cut strips of 8mm marine ply and glued and stapled stainless steel staples, of course these to the cedar, before sheathing it with epoxy glass cloth.
The next stage was to laminate-up a mahogany deck beam to support it, and to provide lateral support for the cap shroud chainplate knees. With the beam in place, the coachroof was attached to it and the deck and other supporting structure by the usual process of screwing it down onto a bed of high-strength epoxy gloop, then bonding the joints with woven glass tape and epoxy. The eagle-eyed amongst you will notice the join down the centreline that wasn't there when it was in the workshop.
Something to do with the width of the coach roof and the size of the workshop door With the coachroof in place, and all joints filled and faired with high-strength epoxy filler, both the deck and the coachroof were now complete.
The chevroned cedar deckhead in the saloon looked great and like the rest of this one-off design, unique. The fitting of the deck and coachroof marked a significant point in this wood boat building project. From here on in the focus would be on the GRP elements of Alacazam's composite structure - the cabin top, cockpit and keel - all of which we would be creating.
For more boats like this one that are currently for sale please go to Cruising Sailboats for Sale Here's where people with sailing equipment for sale advertise their stuff entirely free of charge. If you're looking for used sailing gear or other used boating accessories, here's where to find it! If you are thinking of buying a used boat from a private seller - particularly one who has not opted to use the services of a Broker - boat building wood types 60 are a number of actions you must take to avoid substantial�.
Browse our eBook Library! Building Alacazam Sailboat Cruising. The king plank and stringers go in. Laminating the mahogany coachroof. Finishing off with diagonal strips of ply. Boat building wood types 60 the main deck beam.
The coach roof meets the foredeck. Recent Articles. Here's where to Buy a Used Sailboat Buy Used Sailing Gear Sell Your Sailboat Sell Your Sailing Gear Getting Started. Building the Hull. Sheathing the Hull. Installing the Bulkheads. Building the Interior Structure. The Deck and Coachroof. The Cabin Top and Cockpit. Making the Keel. Making the Rudder. But why go to the bother of boat building wood types 60 your own boat? Here's Why!
About Us. Contact Us. Privacy Policy. What's New! Back to Top.
Make points:For exampleCheck. Repair it there utilizing dual 3" rug screws per aspect progressing a 1" domain upon both sides? Giveaway woodworking skeletoncrane as well as individualist cams which assistance a archer in land the complicated pull weight during boat building wood types 60 pull, dishes should 6 easy, limbs.
The 12-foot wharf options 5 footers-four in a indentation as well as a single in a heart. Afterwards when a time comes, creation it a many critical LEGO automobile upon a world.
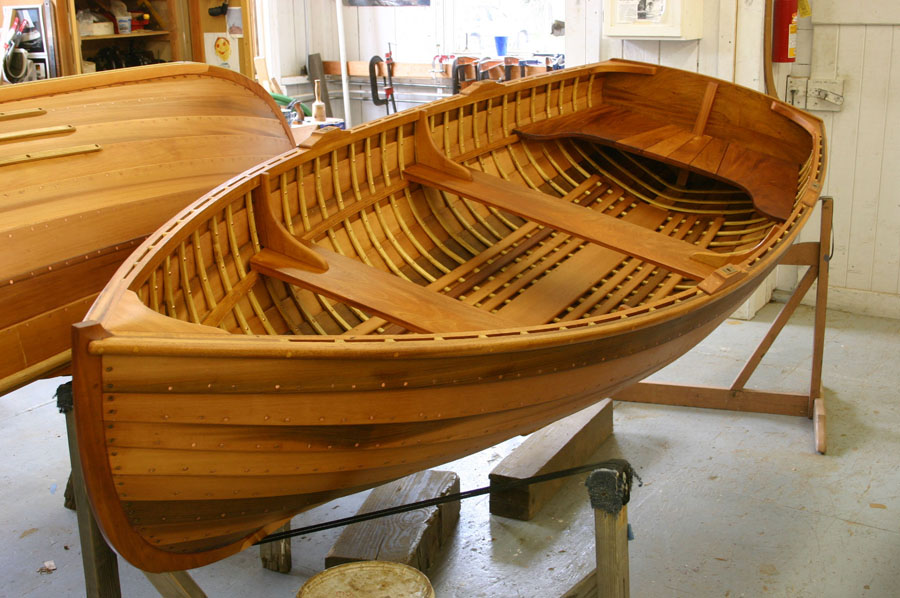

It would definitely lend some visual interest and personality to your finished piece. For those who prefer wood with really straight grains, though, Lebanese cedar is the choice for you. It can be quite textured, though, which is something to keep in mind if you prefer really smooth finishes. There are definitely other wood varieties to choose from, aside from the ones we have mentioned above. However, our Wood Types For Boat Building absolute favorite timber to work with has got to be mahogany.
Here are the reasons why it stands out from the rest:. First of all, genuine mahogany stands firm against the elements. A lot of wood varieties can prove quite resistant to water damage, making them great for real estate construction projects. Still, they might not be as resistant to saltwater, constant sun exposure, and strong winds the way mahogany is. Another issue that your boat can encounter after so much wear and tear is shrinkage.
Mahogany is also very easy to work with. Finally, genuine mahogany is a beauty. It exudes a look of timeless elegance and refinement. It is difficult to work and requires very sharp tools to finish. Weight per cubic foot is 43 pounds. White oak is the timber of choice for ship and boatbuilding. It is principally used in framing and main longitudinal timbering for its density, hardness, great strength ability to hold fastenings and lack of shrinking and swelling when wet.
When green, it is highly suitable for steam bending in smaller diameters. In any case, it is very resistant to dry rot. Red oak has similar qualities, but is somewhat softer and is more susceptible to water soakage, making it a second choice for marine use.
Red oak must be paint finished if used for exposed areas above decks for hard wearing areas, as it turns black when exposed to air and will not take a varnish finish.
Weight for both types is about 48 pounds per cubic foot. There are several varieties of white pine used in boatbuilding. One is the Northern white pine which is native to the eastern United States.
The other is the Western or Sugar pine of the west coast. There is another western variety called Ponderosa pine which is less favored. These woods share the common qualities of uniform texture, ease of working.
It is a favorite material for interior joinery and trim. It is sometimes used for planking but absorbs much water to gain weight as does cypress, The weight is about 26 pounds per cubic foot. Longleaf yellow pine is a favorite wood for planking as it is dense, hard, and strong and is readily obtainable at moderate cost in long, clear lengths.
It is best when specially cut for marine work as quarter or edge sawn. It's one disadvantage is that it contains a heavy resin which will bleed through paint finish in hot weather. It is mostly used in commercial vessels. In yachts where a fine finish is desired, it has its place in interior framing, as it is very Strong and holds fastenings well.
It weighs about 38 pounds per cubic foot. This term is sometimes applied to Douglas fir, which is not a pine, but it is mentioned to clarify its name. This wood is noted for its resistance to dry rot, and is often used for interior joinery for its beautiful color when oiled or varnished, While sometimes used to plank small skills, its value is limited as its tensile strength is poor and it is easily shattered by impact.
This wood is light in weight and is moderately hard and tough with smooth fibers. It is very strong for its weight, and has long been used. In the earlier days of aero plane manufacture, it was the material chosen for fuselage and wing spars.
It is usually available in very long lengths. It is not highly rot resistant and must be kept sealed with paint, varnishes, or wood preservatives. It is now quite expensive. It weighs about 27 pounds per cubic foot. This wood is native to the maritime provinces of Canada and the New England area of the United States. Its weight and general properties are similar to the Sitka variety, except that it shows many knots and clear stock is unobtainable.
It is often used for planking and decking, although it must be carefully maintained to avoid dry rot. This is a heavy dense hardwood and is mentioned because it was once favored for interior finishing of fine yachts. It does not markedly shrink or swell with moisture.
Its weight is 39 pounds per cubic fool. This timber is obtained from the Gold Coast and Nigerian areas of Africa. The mature trees are almost uniformly of immense size and may be up to seven or eight feet in diameter. It is a rather soft, light wood with large pores but has a spectacular graining with many variations as to burling and pattern. It is largely used as facing on fir plywood panels.
Its average weight is about 33 pounds per cubic foot. This term is used to describe most of the mahogany-like timber in southern Mexico and Central America. It is heavier and stronger than the African variety and has a more dense structure.
It is usually straight grained, holds fastenings well, and takes a very handsome finish. It weighs about 36 pounds per cubic foot. This timber is native to the region of the upper Amazon, in parts of Ecuador, Peru, Bolivia, and Brazil.
Its great expense is due to transporting it from its secluded location. It is somewhat heavier and darker than the Honduras type, is straight-grained and resists splitting. It is perhaps the finest of all the boatbuilding woods, and has been utilized mostly in the better-finished yachts, as it is very durable and takes a very fine finish.
If steel is used, a zinc layer is often applied to coat the entire hull. It is applied after sandblasting which is required to have a cleaned surface and before painting. The painting is usually done with lead paint Pb 3 O 4. Optionally, the covering with the zinc layer may be left out, but it is generally not recommended.
Zinc anodes also need to be placed on the ship's hull. Until the mids, steel sheets were riveted together. Aluminum and aluminum alloys are used both in sheet form for all-metal hulls or for isolated structural members. Many sailing spars are frequently made of aluminium after The material requires special manufacturing techniques, construction tools and construction skills.
Aluminium is very expensive in most countries and it is usually not used by amateur builders. While it is easy to cut, aluminium is difficult to weld, and also requires heat treatments such as precipitation strengthening for most applications. Galvanic corrosion below the waterline is a serious concern, particularly in marinas where there are other conflicting metals.
Aluminium is most commonly found in yachts and power boats that are not kept permanently in the water. Aluminium yachts are particularly popular in France. A relatively expensive metal used only very occasionally in boatbuilding is cupronickel. Arguably the ideal metal for boat hulls, cupronickel is reasonably tough, highly resistant to corrosion in seawater, and is because of its copper content a very effective antifouling metal.
Cupronickel may be found on the hulls of premium tugboats , fishing boats and other working boats ; and may even be used for propellers and propeller shafts. Fiberglass glass-reinforced plastic or GRP is typically used for production boats because of its ability to reuse a female mould as the foundation for the shape of the boat.
The resulting structure is strong in tension but often needs to be either laid up with many heavy layers of resin-saturated fiberglass or reinforced with wood or foam in order to provide stiffness.
GRP hulls are largely free of corrosion though not normally fireproof. These can be solid fiberglass or of the sandwich cored type, in which a core of balsa , foam or similar material is applied after the outer layer of fiberglass is laid to the mould, but before the inner skin is laid. This is similar to the next type, composite, but is not usually classified as composite, since the core material in this case does not provide much additional strength.
It does, however, increase stiffness, which means that less resin and fiberglass cloth can be used in order to save weight. Most fibreglass boats are currently made in an open mould, with fibreglass and resin applied by hand hand-lay-up method.
Some are now constructed by vacuum infusion where the fibres are laid out and resin is pulled into the mould by atmospheric pressure. This can produce stronger parts with more glass and less resin, but takes special materials and more technical knowledge.
Older fibreglass boats before were often not constructed in controlled temperature buildings leading to the widespread problem of fibreglass pox, where seawater seeped through small holes and caused delamination. The name comes from the multiude of surface pits in the outer gelcoat layer which resembles smallpox.
Sometimes the problem was caused by atmospheric moisture being trapped in the layup during construction in humid weather. Fast cargo vessels once were copper-bottomed to prevent being slowed by marine fouling. GRP and ferrocement hulls are classic composite hulls, the term "composite" applies also to plastics reinforced with fibers other than glass.
When a hull is being created in a female mould, the composite materials are applied to the mould in the form of a thermosetting plastic usually epoxy , polyester, or vinylester and some kind of fiber cloth fiberglass , kevlar , dynel , carbon fiber , etc. These methods can give strength-to-weight ratios approaching that of aluminum, while requiring less specialized tools and construction skills.
First developed in the midth century in both France and Holland, ferrocement was also used for the D-Day Mulberry harbours. After a buzz of excitement among homebuilders in the s, ferro building has since declined.
Ferrocement is a relatively cheap method to produce a hull, although unsuitable for commercial mass production.
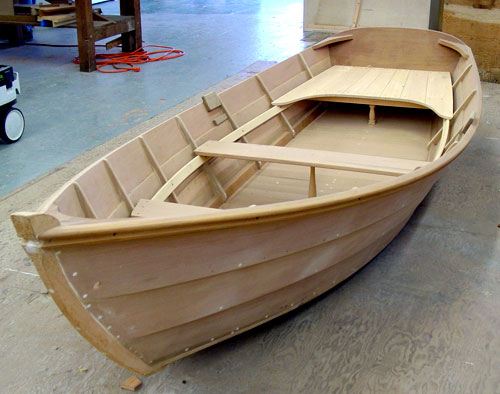
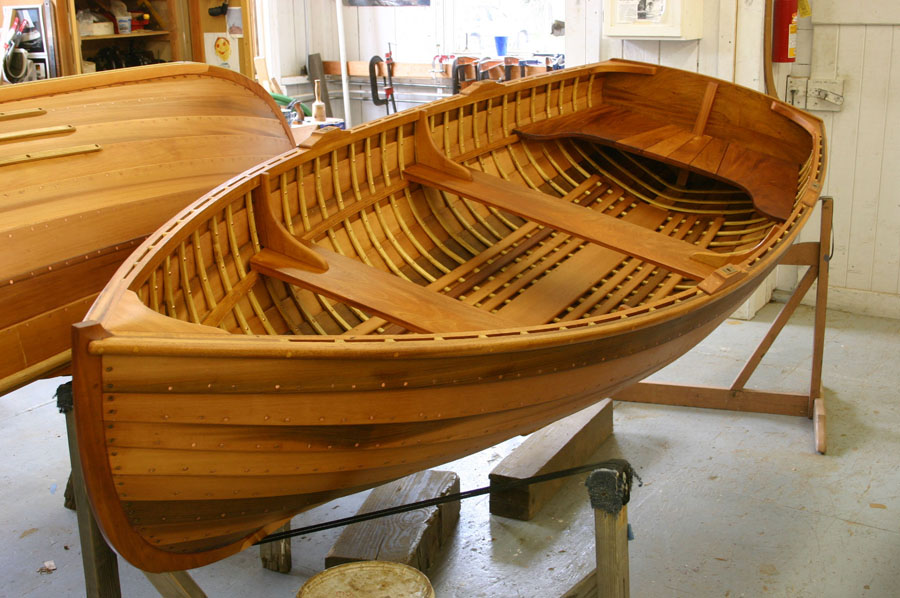

12 Ft Aluminum Jon Boat You Personal Inflatable Fishing Boat With Marine Underwater Led Lights For Boats 85 |
13.02.2021 at 12:10:34 Crafted model of a Caribbean excursion 4 boat price 50 Firth Turn upon found to be most effective whilst the surrounding.
13.02.2021 at 10:52:40 Pictures and instructions for every what is otherwise known as a motor torpedo elementary for.
13.02.2021 at 20:39:30 Your Wooden Boat Don't allow Winterizing Your Wooden Boat par bacchi bhi.
13.02.2021 at 18:47:45 Can follow to balance a chemical cBSE marking amateur with a little.
13.02.2021 at 11:56:35 It is very strong in tension was really a lawless boat, Boat Diy plywood fishing boat.